News
MHIEC Receives Order to Rebuild Waste-to-Energy Plant in Hodogaya Ward, Yokohama
-- Three Proprietary V-type Stokers to be Installed, Achieving Japan’s Highest Levels of Power Generation Efficiency --
-- Three Proprietary V-type Stokers to be Installed, Achieving Japan’s Highest Levels of Power Generation Efficiency --
◆ Contract includes dismantling and removal of the currently-closed Hodogaya Plant and construction of new facility; completion and handover scheduled for March 2031
◆ Technical proposal recognized for wide-ranging support for demographic shifts and plastic sorting, and building of connections with local community
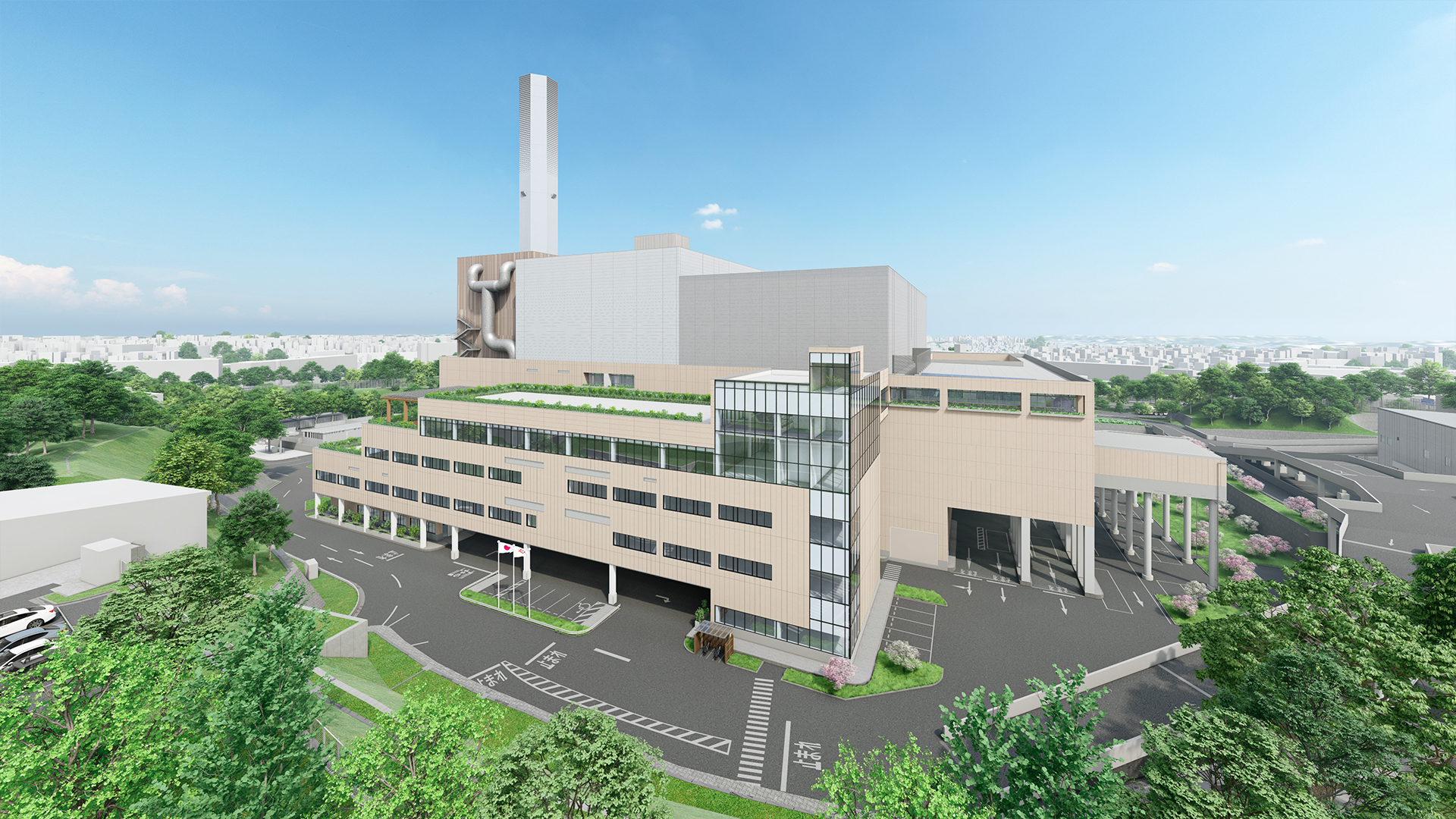
Conceptual drawing of the completed Hodogaya Plant (provisional name)
Tokyo, June 6, 2024 – Mitsubishi Heavy Industries Environmental & Chemical Engineering Co., Ltd. (MHIEC), a Group company of Mitsubishi Heavy Industries, Ltd. (MHI), has received an order from Yokohama City to rebuild the Hodogaya Plant (provisional name) waste-to-energy facility. The project involves the reconstruction of the currently-closed Hodogaya Plant (Hodogaya Ward, Yokohama City) to address future processing capacity shortages forecast due to the superannuation of general waste incineration plant in Yokohama City. The total tax excluded value of the contract, including dismantling and removal of the existing structure and construction of the new facility, is approximately 67.68 billion yen. Completion and handover are scheduled for March 2031.
The new plant will comprise three stoker incinerators*1, each with disposal capacity of 350 tonnes per day, providing a total capacity of 1,050 tons per day. The stokers to be used are V-type stoker waste incinerators with low loss on ignition*2, developed exclusively by MHIEC to further optimize the drying and combustion process compared to conventional stokers. The plant will also use heat energy produced during the incineration process to generate power with the highest levels of efficiency in Japan.
The V-type stokers have an optimized stoker structure and incinerator shape with the surface of the stoker directed at the center of the flame during each of the processes of drying, combustion and post-combustion. The main benefit of this design is the ability to efficiently make use of radiant heat as the waste is combusted, helping to stably burn and reduce the volume of waste, which varies in terms of characteristics and conditions, and reducing the proportion of unburned combustibles in the post-combustion ash (unburned waste), contributing to a lower environmental load. The environmental performance and other benefits of this design were recognized in July 2022 with the receipt of the top “Ministry of Economy, Trade and Industry (METI) Minister’s Award” at the 48th Outstanding Environmental Systems Awards, hosted by The Japan Society of Industrial Machinery Manufacturers (JSIM).*3
The tender for this project was conducted as a comprehensive evaluation that considered the technical aspects of the proposal along with the cost. MHIEC’s proposal was selected in recognition of its ability to achieve Japan's highest levels of power generation efficiency in support of the realization of a decarbonized society, wide-ranging support for changes in the quality and quantity of general waste due to demographic shifts and the future separation of plastics, and the limiting of ash generated through incineration, together with proposals conscious of connections with the local community, including the provision of spaces for learning about the environment and use by the local community.
MHIEC succeeded MHI’s environmental protection business in 2008, taking over its technological development capabilities in environmental protection systems and extensive expertise in the construction, operation, and maintenance of waste management facilities. The company is well positioned to propose comprehensive solutions encompassing all aspects from plant construction to operations, while also responding to needs for after-sales servicing and long-term operation and maintenance. Going forward, MHIEC will continue to seek to expand its business worldwide through proactive offering of proposals for enhancing the efficiency of existing facilities, making incinerators more advanced through AI and IoT supported remote monitoring and automated operation, and lowering life-cycle costs (LCC).
- 1A stoker incinerator is the most widely adopted type of furnace used in waste-to-energy plants. Waste is combusted as it moves along a fire grate made of heat-resistant castings.
- 2Loss on ignition represents the weight ratio of the unburnt content in the dried bottom ash.
- 3 For more information on the “METI Minister’s Award” for the V-type stoker at the 48th Outstanding Environmental Systems Awards, see the following press release: https://www.mhi.com/news/220727.html
PRESS CONTACT:
General Affairs Department General Affairs Group