CO2 COMPRESSOR SOLUTIONS FOR CARBON REDUCTION INITIATIVES
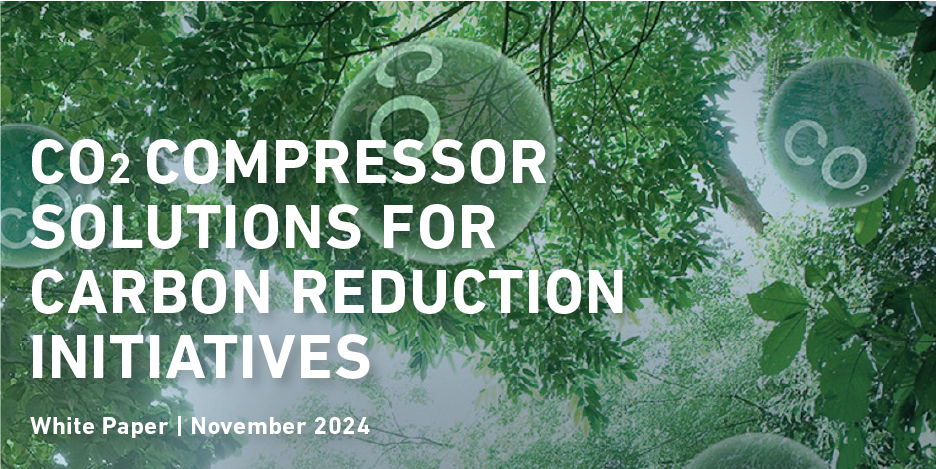
Introduction
Achieving a carbon-neutral world is one of the most significant challenges of our time, seeking collaborative efforts across governments, industries, and non-profit organizations. The urgency to reduce greenhouse gas emissions at both local and global levels has led to innovative approaches such as Carbon Capture, Utilization, and Storage (CCUS). This range of technologies aims not only to capture carbon dioxide (CO2) emissions but also to utilize or store it in a safe and effective manner. A critical component of the CCUS value chain is the use of high-pressure compressors, which play a vital role in the transportation and storage of CO2 — a gas that poses unique technical and economic challenges due to its corrosive properties and varying states under pressure.
Mitsubishi Heavy Industries Compressor Corporation (MCO) stands at the forefront of this technological advancement, bringing extensive experience in high-pressure, high-capacity CO2 compressors previously applied in industries such as urea production and gas processing. In this paper, we will explore the multifaceted challenges associated with handling CO2, the advanced technologies within MCO's growing portfolio and how our expertise is driving the transition towards a carbon-neutral society.
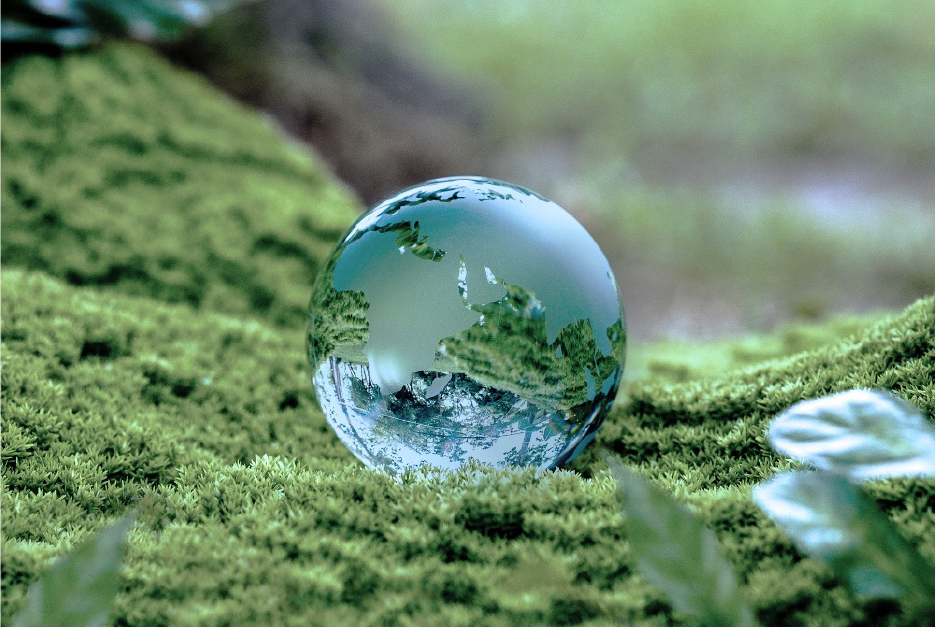
CONTENTS
TOPIC | PAGE |
---|---|
Carbon Net-Zero - A global imperative | 3 |
MHI's strategy to support a carbon neutral world | 4 |
Technical features of CO2 compression system | 6 |
CO2 compressor line-up and experience | 7 |
Comparison of CO2 compressor | 8 |
MCO's technology of CO2 compressor system | 9 |
Conclusions | 14 |
Carbon Net-Zero - A global imperative
Achieving a carbon neutral world is a global challenge. It will require participation from both the public and private sectors as well as international collaboration.
At COP21 in December 2015, in Paris, approximately 200 countries agreed to form the Paris Agreement. This landmark agreement succeeds the Kyoto Protocol and aims to limit the increase in global average temperature to well below 2 °C above pre-industrial revolution levels, with a commitment to pursue efforts to limit it to 1.5 °C .
To achieve this, the long-term objective has been set: achieving Net Zero global greenhouse gas emissions as early as possible, ideally by the end of the 21st century — a commitment to decarbonization.
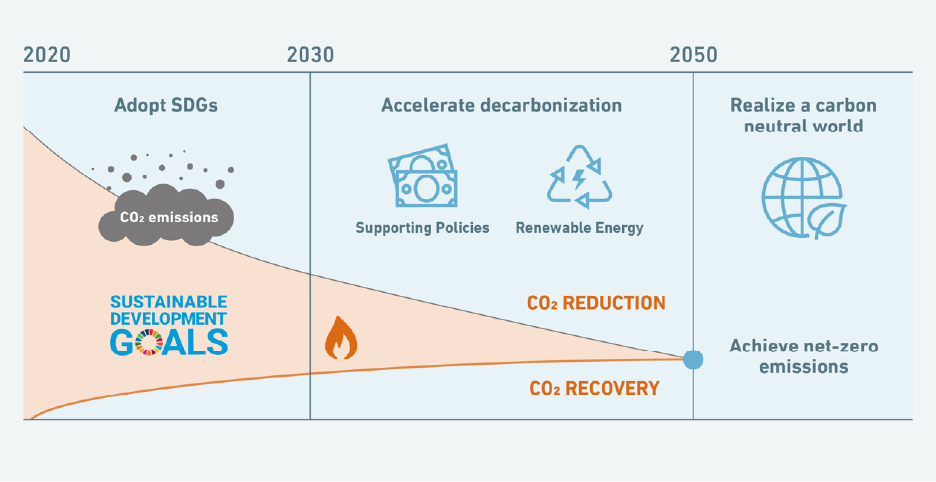
MHI's strategy to support a carbon neutral world
In October 2021, MHI Group announced its commitment to “MISSION NET ZERO.”. As a proven leader in decarbonization, we recognize our responsibility to lead the way in combating climate change.
To achieve Net Zero, we will leverage a wide range of products, technologies and services to reduce CO2 emissions. Specifically, we aim to achieve a 50 percent reduction by 2030 and reach Net Zero by 2040.
MHI Group has developed a comprehensive strategy to contribute to the transition towards a carbon-neutral society. This approach focuses on curbing rising social costs while advancing new decarbonization technologies alongside existing solutions.
The first step is decarbonizing coal and gas power plants, while utilizing nuclear power generation systems. MHI Group excels in advanced next-generation technological development, having already. implemented our technology that optimizes facility operations and controls overall emissions through digitization and expanded use of AI.
We plan to expand the application of our digitization technology to support customers in the industrial sector, where efficient use of assets, improvement of production efficiency and decarbonization are key goals. We believe that by contributing to the growth of our customers' businesses, we can also expand MHI Group's own offerings, including asset operations support, maintenance services and facility upgrades.
However, reducing CO2 emissions alone is not enough to achieve carbon neutrality. In areas where CO2 emissions are unavoidable, the importance of technologies for capturing and using CO2 will increase. MHI Group has a track record in CO2 recovery, and we will continue to promote carbon recycling initiatives.
We will also work to build a hydrogen value chain that addresses society's decarbonization needs by leveraging the technologies we have developed across various fields.
Despite challenges like economic efficiency, achieving net-zero carbon by 2050 is within reach. This can be accomplished by establishing a long-term vision and driving technological innovation and business development through our accumulated resources.
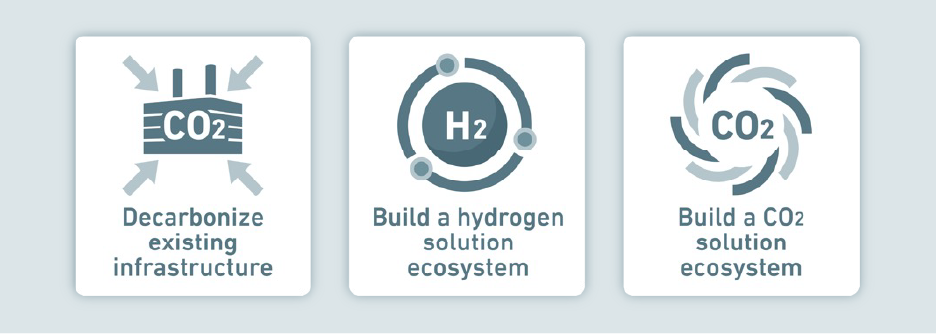
Simply reducing CO2 emission is not enough to achieve carbon neutrality. As a result, CCUS and associated technologies are gaining significant attention.
MHI Group provides core technologies essential for CCUS, including CO2 capture, transportation and compression. We aim to expand our business in large, liquefied CO2 carriers and CO2 compression, which will become important as the volume of captured CO2 increases over time. MHI is helping to establish a robust CO2 value chain by offering a wide variety of CCUS-related technologies.
MCO, a long-time manufacturer large special-purpose compressors, serves various applications in oil & gas, petrochemical and energy. The compressors manufactured by MCO play an important role in capture, transportation and utilization/storage of the CCUS value chain.
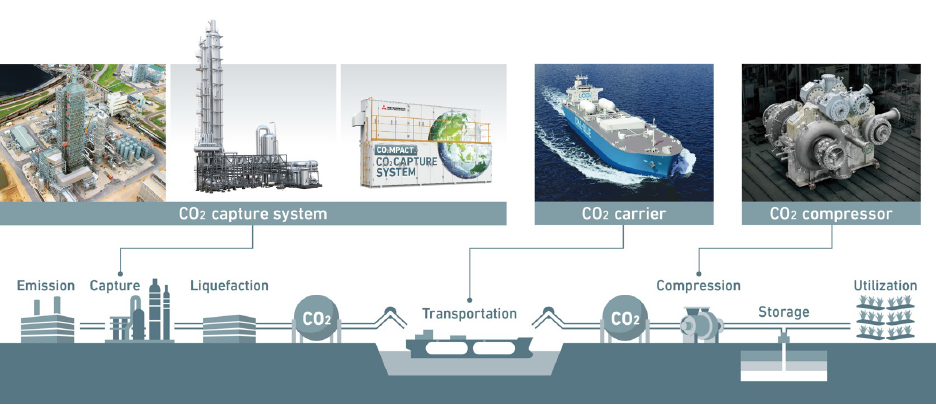
Technical features of CO2 compression system
Due to the characteristics of CO2 gas, there are several technical challenges that need to be addressed. To tackle these issues, it is necessary to use a robust CO2 compressor to overcomes them.
Performance prediction:
CO2 exists in various states: gas, liquid and solid. As the pressure and temperature of CO2 are increased, it reaches acritical point where it can exist as either a liquid or a gas. Beyond this point CO2 becomes supercritical fluid, in which the supercritical fluid has special properties that combine the density as a liquid and viscosity as a gas. Near the critical point, the composition of the gas can change rapidly, making accurate performance predictions particularly challenging.
Vibration:
CO2 becomes a high-density fluid (approaching the density of water) when it is pressurized, and the fluid excitation force increases, which can cause unstable vibrations, so sufficient care must be taken when designing the rotor system.
Material Corrosion:
CO2 gas is often in a saturated state at the compressor inlet. CO2 dissolves easily in water and becomes weakly acidic, leading to corrosion of metals. At higher pressures, corrosion becomes more severe. Corrosion prevention measures are necessary for all parts of the compressor that are in contact with the CO2 gas.
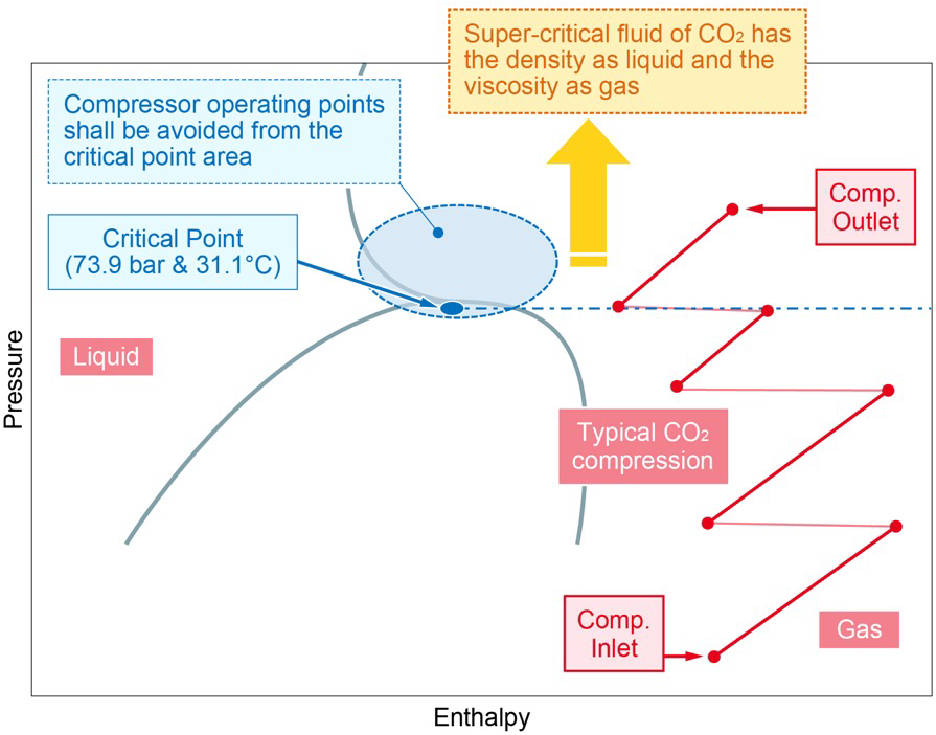
CO2 compressor line-up and experience
The compressors required for the CCUS value chain apply the same technology as CO2 compressors used in urea plants and CO2 reinjection systems in gas processing facilities. High-pressure compressors are essential for the transport and storage of CO2. CO2 gas is highly corrosive and difficult to handle. MCO has extensive experience in high-pressure, high-capacity CO2 compressors used in urea plants and gas treatment facilities.
Urea (CH4N2O), a key raw material for chemical fertilizers, is synthesized from ammonia (NH3) and carbon dioxide (CO2). During this manufacturing process, CO2 compressors are used to pressurize the CO2. MCO has delivered more than 100 CO2 compressors to fertilizer plants and reinjection compressors for gas treatment plants, establishing a strong track record in the area.
Since the early 2000s, MCO has applied technology developed for urea and gas processing facilities to supply CO2 compressors for injecting CO2 for storage underground and Enhanced Oil Recovery (EOR). This is the beginning of its application in the decarbonization field. Since 2021, when the world has made a shift toward carbon neutrality, demand for CO2 compressors for CCUS has increased and our focus on the decarbonization sector continues to grow.
MCO offers two types of CO2 compressors. The first is single-shaft multi-stage type compressor, often referred to as “between bearing” or “inline.” The second is a geared type, often referred to as “integrally geared.” MCO's single-shaft multi-stage compressor, MAC, or Mitsubishi Advanced Compressor , has horizontal split type and vertical split type. The geared type, which features multiple pinion shafts combined with a gear wheel, is referred to as MAC-G, or Mitsubishi Advanced Compressor Geared.
A few of MCO's notable CO2 references are shown in below.

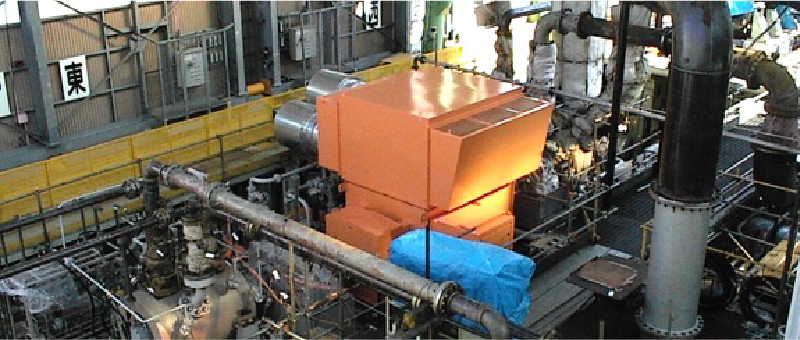
CO2 compressor for international large scale CCS Project
- Site
- Algeria delivered in 2003
- Capacity
- 2,200 ton/day x 2
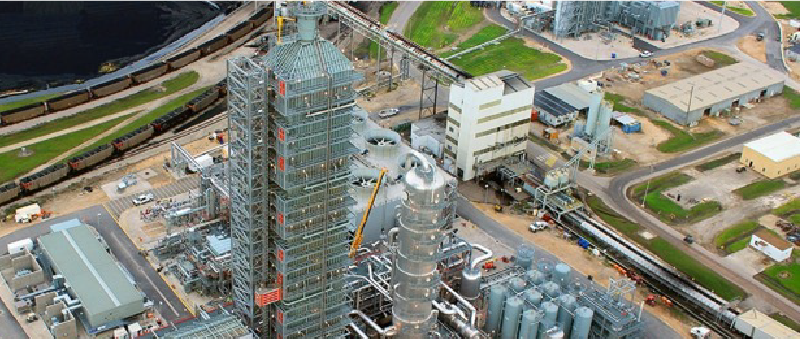
CO2 compressor for world's largest post-combustion CO2 capture project
- Site
- USA delivered in 2016
- Capacity
- 4,800 ton/day
Comparison of CO2 compressor
The MAC and MAC-G used for compressing CO2 each have their advantages and disadvantages. Therefore, the most suitable equipment is selected based on process conditions, customer requirements and other project drivers. Figure 7 shows an application map of MAC and MAC-G. While both solutions cover a wide-range of operating conditions, MAC can be used for high discharge pressures that exceed capabilities of a geared solution, while MAC-G is used when the suction flow rate is large.
Table.1 shows a comparison between MAC and MAC-G when used under the same conditions. The results of this comparison will vary depending on the conditions under which the equipment is used and where the plant is built. MCO can supply the most suitable equipment tailored to our customer's requirements.
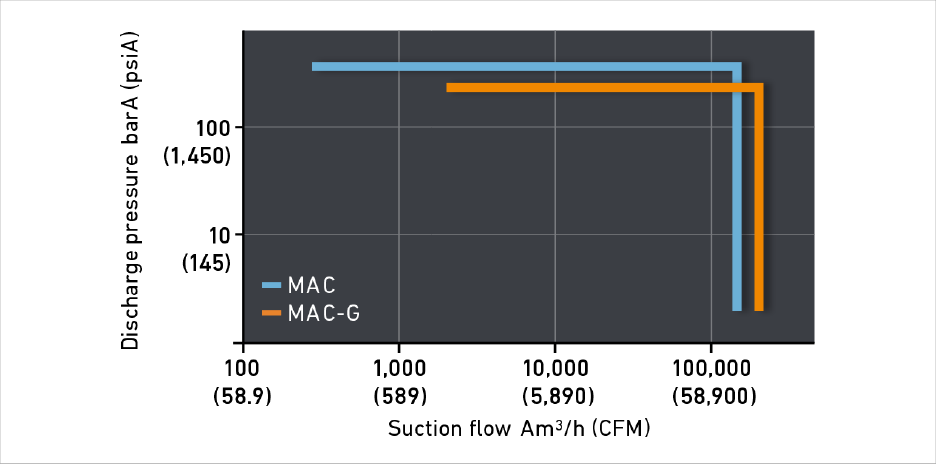
Table. 1 Comparison Table of advantages between MAC and MAC-G
MAC | MAC-G |
---|---|
Fewer seals Ease of maintenance (Simple disassembly/reassembly) Increased reliability |
Higher efficiency Fewer couplings Smaller footprint Modularized package |
MCO's technology of CO2 compressor system
CO2 compressors deal with high density gases which generate large excitation forces. Therefore, a rotor design with high stability that enables stable and robust operation under all on-site operating conditions is essential. To achieve this, our compressors feature a high rigidity shaft and enhanced the damping of the shaft system.
Anti-corrosion material selection:
MCO has established corrosion prevention technologies, such as stainless steel weld overlays, to deal with carbonic acid corrosion caused by to CO2 exposure.
High boss ratio impeller:
Figure 8 shows the concept of high boss ratio impeller. This design increases the shaft diameter and improves the rotor rigidity. Figure 9 shows the relationship between the impeller boss ratio and the rotor logarithmic decrement/the relative polytropic efficiency. The impeller boss ratio has been optimized so that high efficiency can be maintained while ensuring the API requirement of logarithmic decrement.
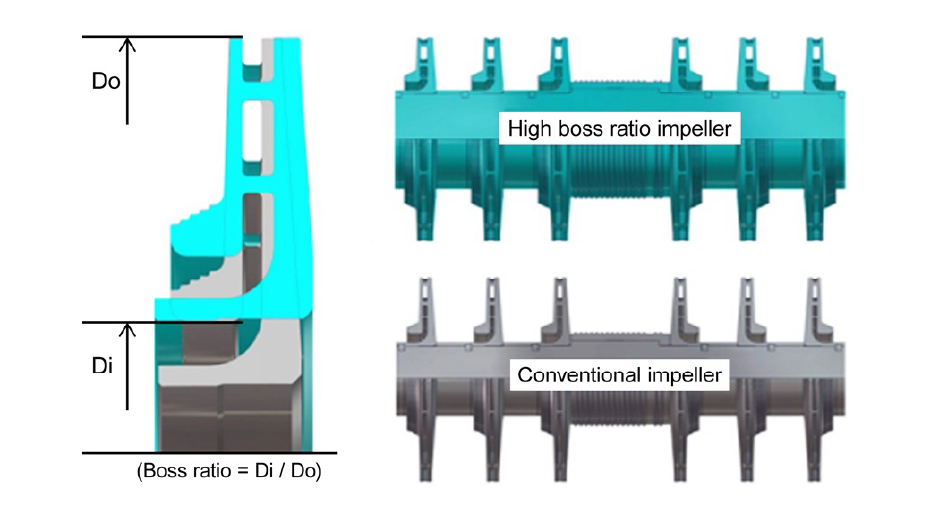
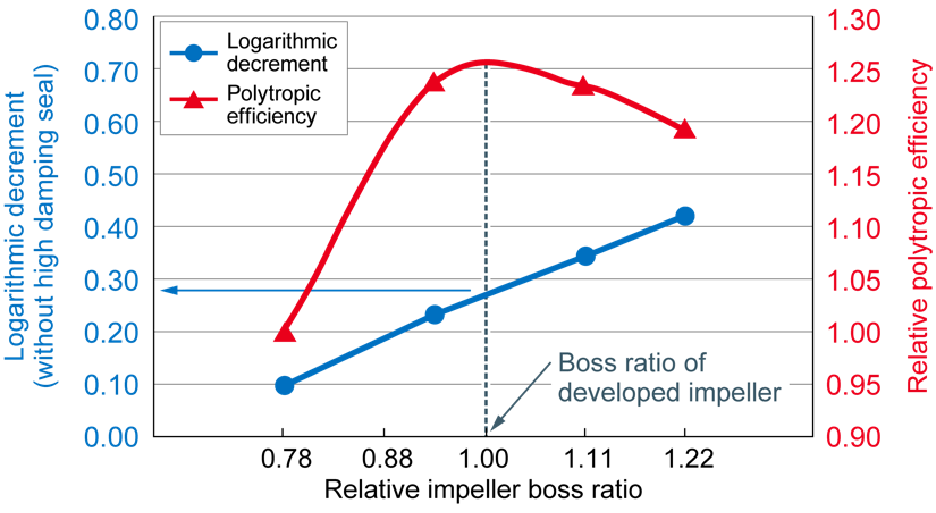
Overhung damper:
To improve the vibration damping characteristics of the rotor, an overhung damper featuring a squeeze film mechanism is added to the shaft end on the outside of the bearing. This design helps to prevent the generation of excitation forces, and MCO refers to this as an “overhung damper.”
Hole Pattern Seal:
Figure 10 shows a step hole pattern seal used for the high-pressure compressor to improve the damping of shaft system. The hole pattern seal used for the machine has a hybrid construction of a hole pattern seal and a step labyrinth seal in order to reduce the leakage rate.
In the evaluation of this seal, parameter studies, including hole diameter, hole depth, were performed using computational fluid dynamics (CFD) to determine the optimal seal shape for minimizing leakage and dynamic characteristics. In addition, a component test with the optimal shaped seal was performed in order to verify the accuracy of the CFD analysis.
Given that supercritical carbon dioxide in the high-pressure compressor are in the region between compressible and incompressible, and its density is close to water, the component test used water as the test fluid to evaluate the seal clearance, the existence of swirl at the seal inlet on the leakage rate and the dynamic characteristics of the seal.
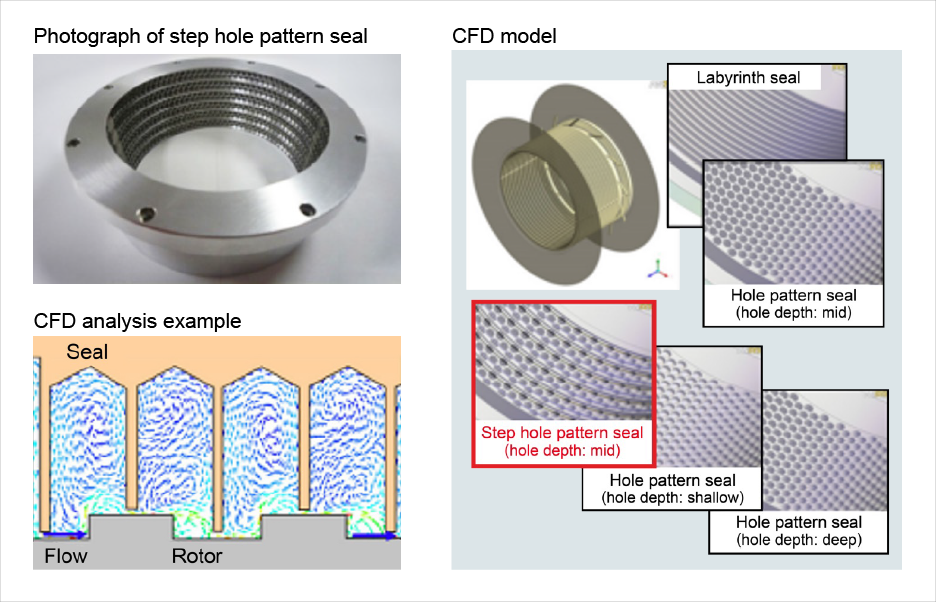
Figure 11 compares the component test results against the analytical CFD prediction, and indicates that the test results were favorably equivalent or better than the CFD analysis results for both the leakage and dynamic characteristics.

The stability under on-site operating conditions was calculated using the model shown in Figure 12. As a result, it was verified that the rotor had high stability that could maintain sufficient logarithmic decrement under all on-site operating conditions of CO2 concentration, pressure, rotating speed, changes in gas quantity. Additionally, the dynamic characteristics and the labyrinth exciting force of the hole pattern seal were derived from the CFD analysis results.
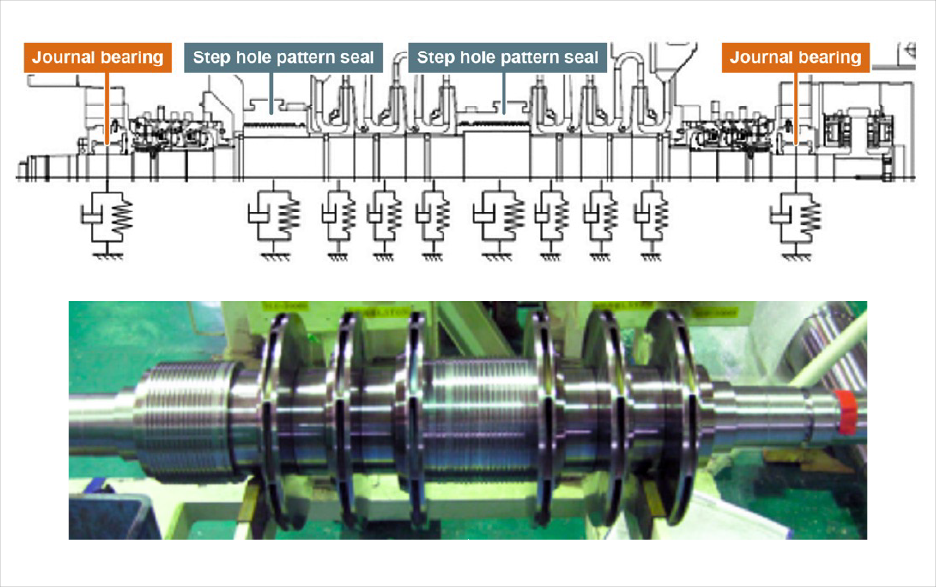
Module package:
High labor costs in facility construction have become a concern, especially in industrialized nations, where the introduction of CCUS is being promoted. To reduce the time required for on-site work, as shown in Figure 13, a compressor, seal system, and instrumentation devices are assembled into one module. The integrally geared compressor and its peripheral components are divided into four modules to accommodate transportation constraints, minimizing the number of parts that need to be transported to the site. In addition, pipes between devices and instrumentation devices are installed after the modules are set up and thus the number of days for site work greatly decrease.
Conventionally, the header of cooling water pipes was installed on the front of the gas cooler and placed on a pipe rack. To improve maintenance accessibility, we redesigned the layout, in which the cooling water pipes are buried or installed on the steel frame rack so that the bundles can be easily pulled out during maintenance of the gas coolers. Additionally, we minimized the presence of ancillary facilities that could obstruct maintenance efforts.
The pipes around the compressor were arranged together to optimize the maintenance space around the compressor. The auxiliary piping connected to the compressor, which must be disassembled at the time of maintenance, is then divided into blocks. This facilitates the disassembly and reassembly of the compressor at the time of maintenance. As a result, the new compact module has its footprint reduced by 20 percent and can be easily installed in a limited space.
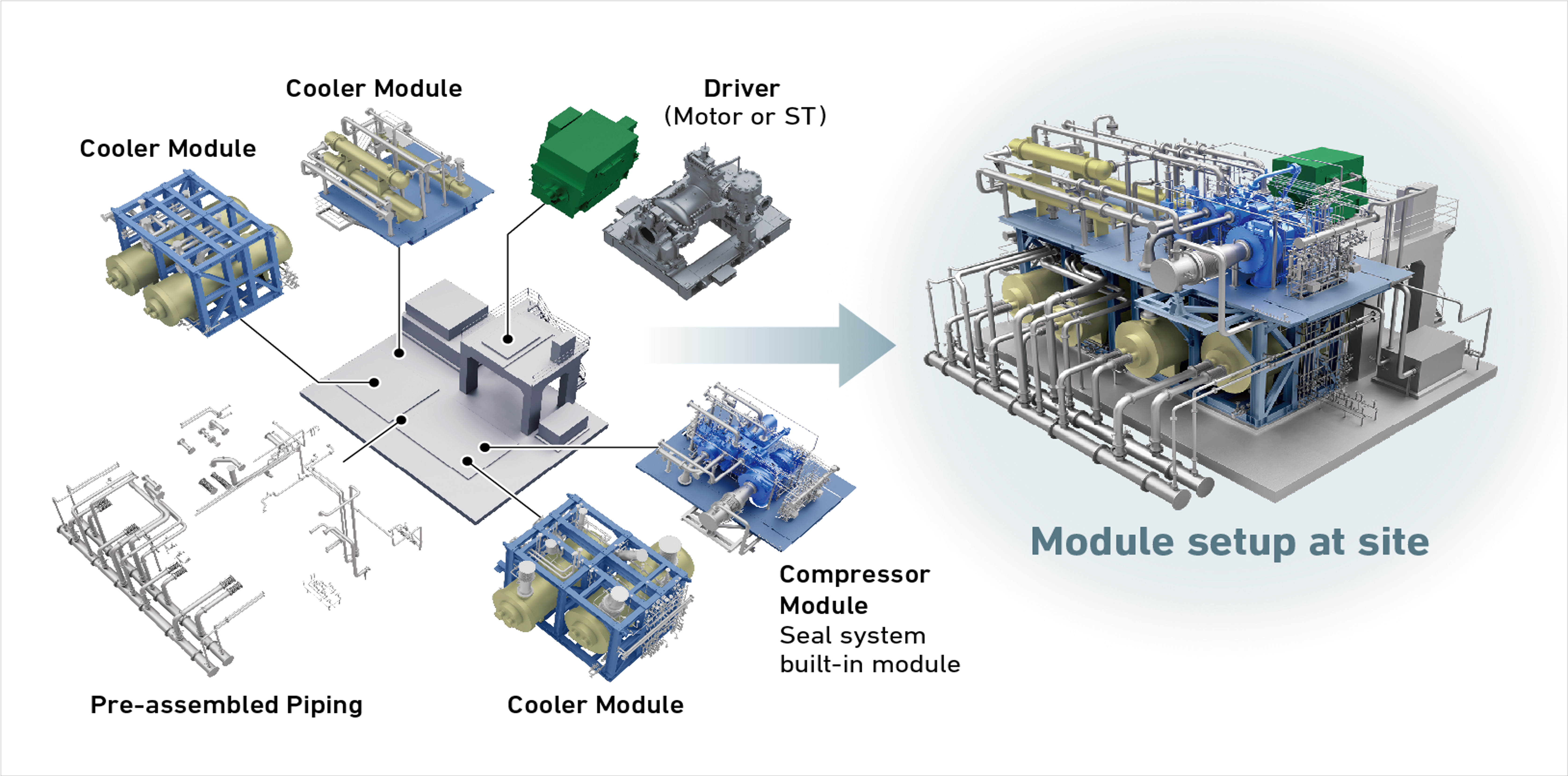
Carbon Floating Ring Seal:
Conventionally, labyrinth seals or dry gas seals have been used for compressor shaft end seals, which requires a sealing system that includes auxiliary equipment like ejectors and gas seal modules. Recently, carbon floating ring seals have been introduced as an alternative shaft end sealing technology. Carbon floating ring seals provide the advantage of a simplified sealing system that is relatively maintenance free, streamlining the sealing process and reducing the need for additional components.
Based on customer’s requirements, MCO can select the most suitable seal from labyrinth seal, dry gas seal or carbon floating ring seal.
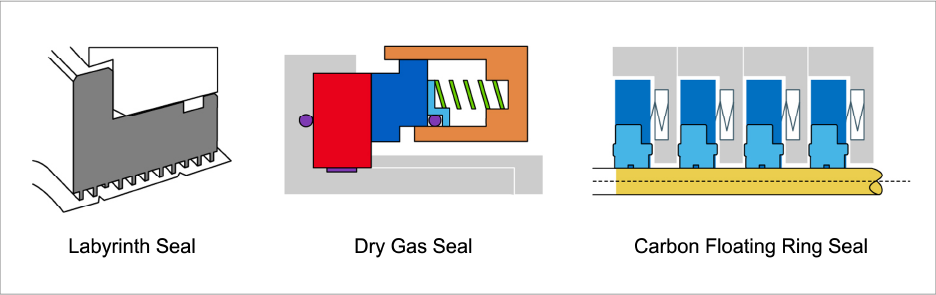
Hirth coupling:
A hirth coupling is a one of the mechanical connections for compressor shaft ends which has numerous advantages, summarized below. Based on our customer’s requirements and applications, MCO can select the most suitable mechanical configuration, such as a hirth coupling, integral flange and hydraulic fit coupling.
- Easy assembly (No skilled worker)
- Short assembly time
- Reduce risk of shaft damage during assembly / disassembly of hydraulic coupling hub
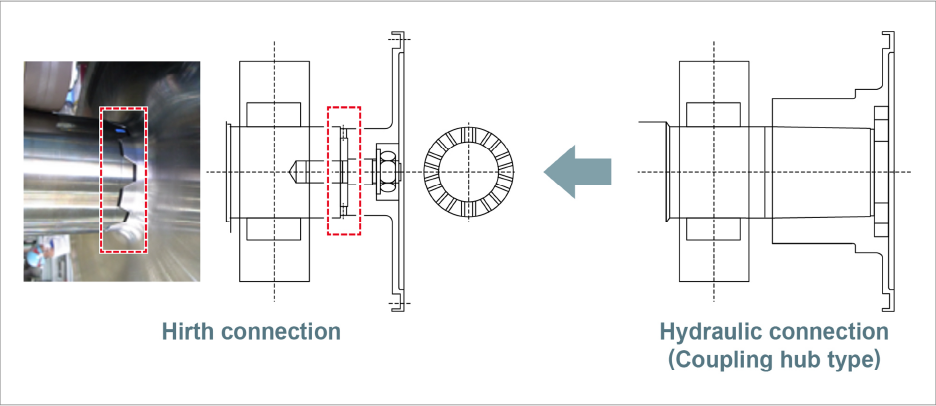
Conclusions
MHI Group is committed to fostering a carbon-neutral world through its comprehensive strategy, "MISSION NET ZERO." This strategy focuses on decarbonization technologies for coal and gas power plants, as well as the utilization of nuclear power and advancements in digitization and AI for emission control.
Additionally, MHI is expanding its use of digitization technology to support customers in the industrial sector, while actively promoting carbon recycling and the development of a hydrogen value chain. In the field of CCUS, MHI provides essential technologies for CO2 capture, transportation, and compression. The company has a strong track record in delivering CO2 compressors for fertilizer plants and carbon storage projects.
Custom industrial compressors are designed to optimally balance conflicting design parameters, such as aerodynamic characteristics, vibration properties of high-speed rotating bodies, manufacturability, operability and maintainability, tailored to the requirements and applications of each project.
CO2 compressors are among the most challenging applications to find the optimal balance of specifications. In addition to the general characteristics of gases, these compressors have unique properties such as high density, high compression ratios, instability of fluid state near the triple point and corrosiveness, which are necessary for CCS applications.
Due to the high density of the gas, the vibration characteristics are severe, and the high compression ratio results in extremely narrow gas flow paths in the high-pressure section, requiring consideration of resistance in the flow path and manufacturing methods. Additionally, the shape of components must be considered according to the degree of corrosion progression over time.
To effectively balance these complex parameters, MCO has developed expertise in selecting optimal materials, combining component shapes, setting operating conditions and maintenance procedures. This knowledge is gathered through years of feedback from design, manufacturing, test runs and field operations, particularly in urea plants and enhanced oil recovery (EOR) applications. Overall, MHI Group is dedicated to advancing decarbonization technologies and leading the transition to a carbon neutral society.
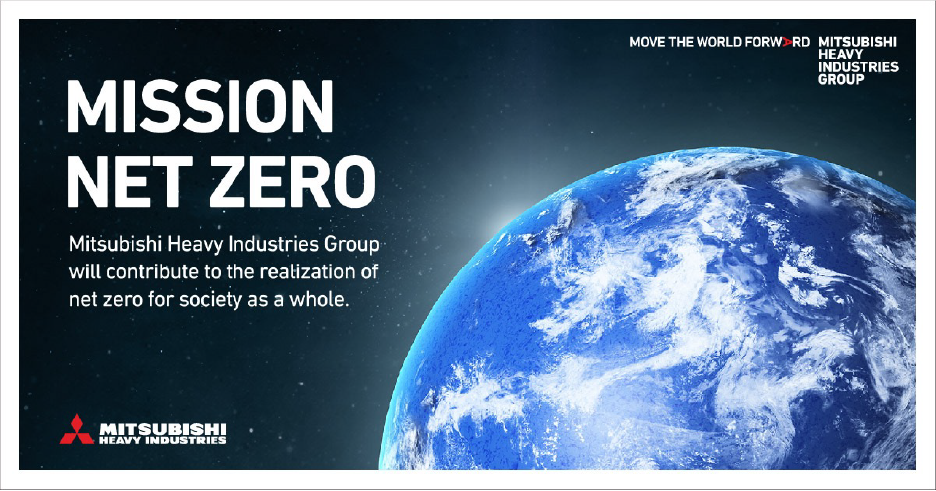
REFERENCES
- Yasuhiro Kawashima et al., Development of CO2 Compressor for Fertilizer Plant,
Mitsubishi Heavy Industries Technical Review, Vol.31 No.3, (Oct. 1994) - Shinichiro Tokuyama et al., Verification Test of 700 bar Super High Pressure Robust
Compressor, Mitsubishi Heavy Industries Technical Review, Vol.51 No.3, (Sep. 2014) - CO2 Compressors Contributing to Building CCUS Value Chain,
Mitsubishi Heavy Industries Technical Revies, Vol.60 No.1, (Mar. 2023)
ACKNOWLEDGEMENTS
We gratefully acknowledge the work of past and present members of MCO and related party.
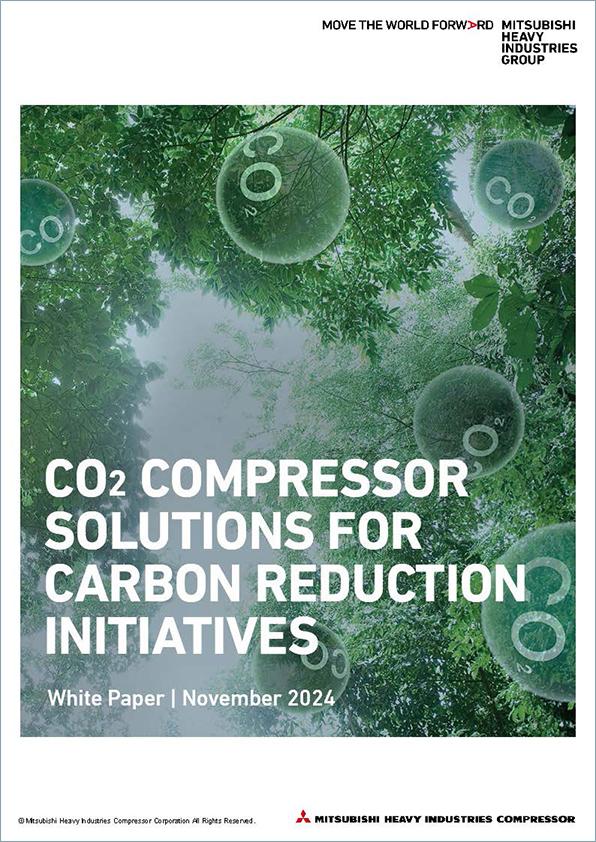