Keep a drink delicious and fresh!
A carbon coating that evolves PET bottled beverages.
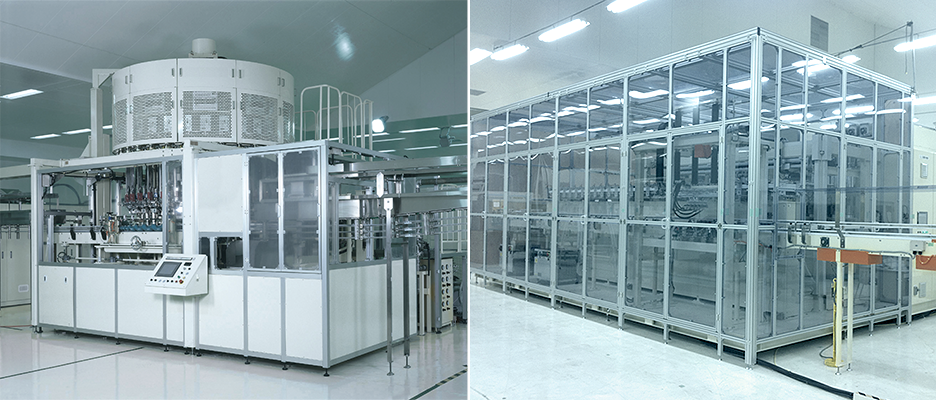
Tea, alcoholic drinks, and carbonated drinks are sold in PET bottles! The DLC coating inside the bottles is now an ever-present part of daily life.
PET bottled beverages are sold in convenience stores, supermarkets, and just about everywhere else. They are now ubiquitous, living in many of our refrigerators and day bags.
Did you know that the inside of the PET bottle is coated with a thin carbon film to keep the beverage delicious?
The DLC (note) coating is an innovative technology to protect beverage quality. Why do PET bottles need to be coated? Let's think about the reason.
- A type of carbon with properties similar to diamond
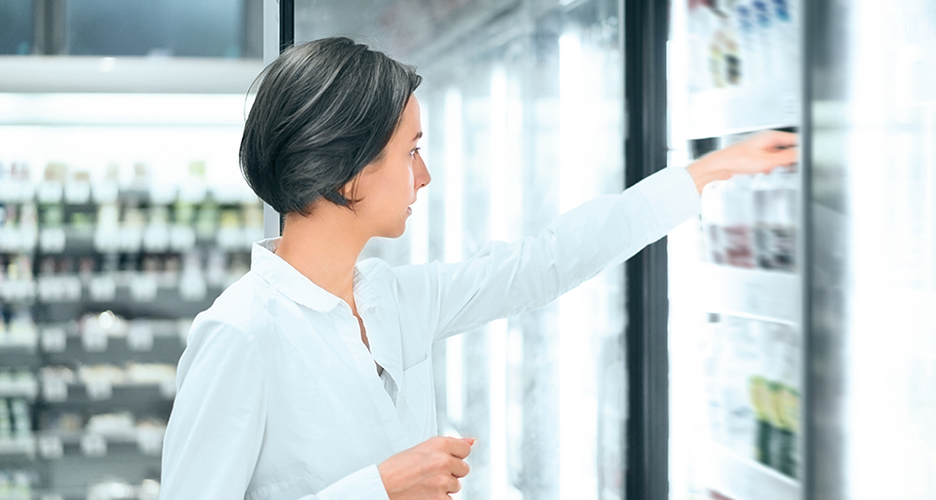
Highlights!
Can air easily permeate a PET bottle?
PET bottles were first used as soft drink containers in around 1982, when Japan’s Food Sanitation Act was amended. Glass-bottled juice was common at the time, but the new PET bottles offered advantages such as a sturdiness, a light weight, good portability, and caps with distinct designs. Consumers everywhere began to choose PET bottles for convenience.
Yet PET bottles are more permeable to oxygen and carbon dioxide than cans or glass bottles. Oxygen can therefore easily flow into a PET bottle, and carbon dioxide gas or water can easily flow out. The gas permeability of the plastic material made it difficult to use the bottles for tea, carbonated drinks, and alcoholic drinks like wine.
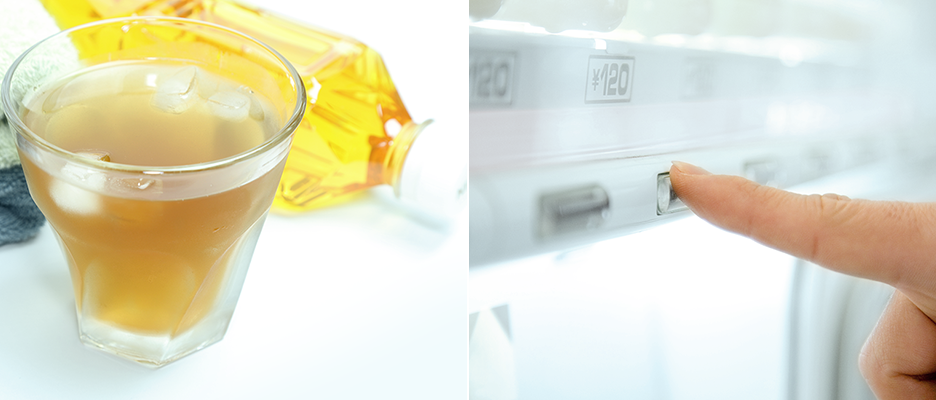
A PET bottle that inoxidizes or retains its contents was born.
To solve this problem, Mitsubishi Heavy Industries Machinery Systems (MHI-MS) developed its Mitsubishi DLC Coating Equipment jointly with a leading beverage manufacturer.
DLC is an acronym for diamond-like carbon. The material has a molecular structure similar to diamond, a gemstone. The DLC used for DLC coating is composed of carbon and hydrogen, and can flexibly follow the deformation of a PET bottle. It therefore retains a high gas barrier performance to block oxygen, carbon dioxide, and gas without reducing the transparency of the bottle material.
How can a thin film be coated on the inside of a PET bottle?
In the food packaging industry at that time, it was considered difficult to deposit a DLC film onto a PET resin (note) bottle.
We tackled the challenge by devising our Mitsubishi DLC Coating Equipment, a technology to deposit film coatings capable of reducing gas permeability to less than one-tenth of that of the original bottle material. Below we summarize the steps to develop the technology and the epoch-making technical points we discovered along the way.
- The petroleum-derived resin commonly known as PET (Polyethylene Terephthalate) excels in strength and transparency but performs poorly in resisting heat.
DLC coating step
Step1 : Evacuate the air from inside the electrode chamber containing the PET bottle with a vacuum device.
Technical point : Vacuum state generated at super high speed
It generally takes from several minutes to several tens of minutes to generate a vacuum state. PET bottles, on the other hand, are produced at ultra-high speeds on the order of several hundred bottles per minute. After researching the technologies of pump manufacturers the world over, MHI-MS used a cutting-edge technology to create an ultrafast vacuum system for PET bottle processing. The system is capable of evacuating air from inside a bottle in as little as two seconds.
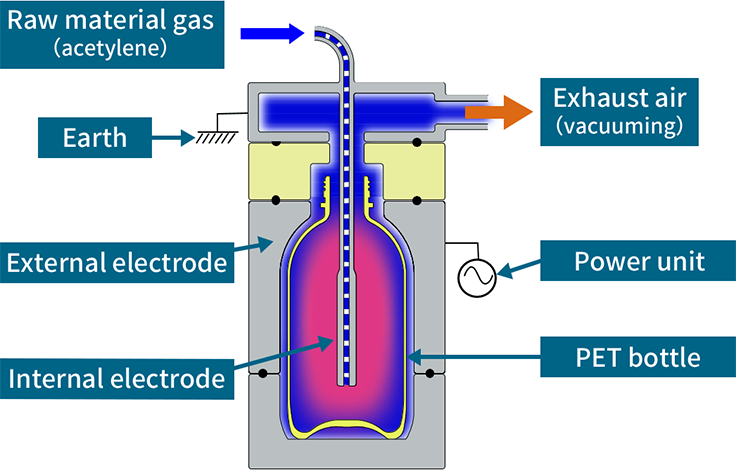
Step2 : Dispense an acetylene gas composed of carbon and hydrogen into the PET bottle
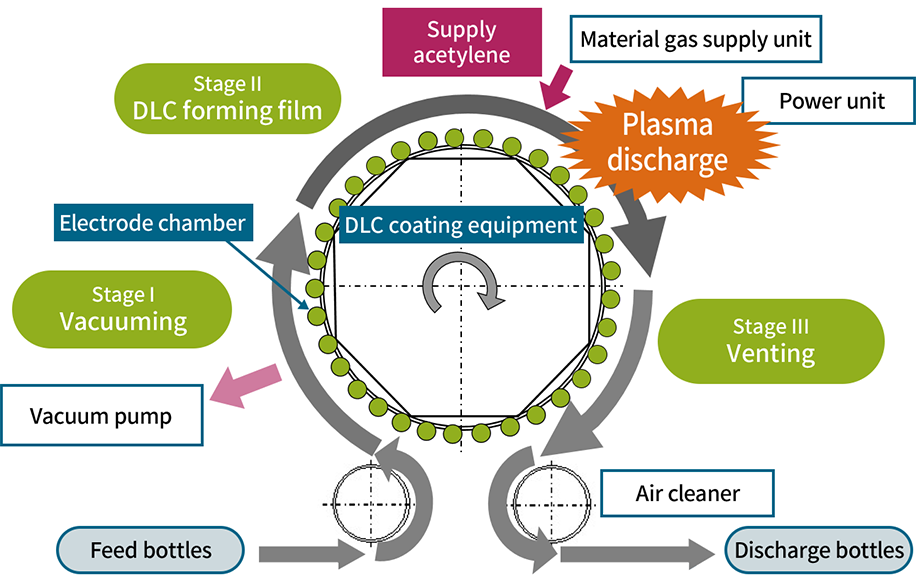
Step3 : The gas molecules are decomposed by applying a high-frequency wave to the electrode chamber to produce an ionized plasma.
- Converting a substance into an ionized plasma state with a high-frequency wave.
Step4 : Decomposed gas molecules in a plasma state fly around inside the PET bottle at high speed, forming a film by hitting against the inner surface. A DLC film coating of 10 to 40 nm in thickness is thus deposited.
Technical point : The poor compatibility between the resin and plasma solved
The electricity used to decompose the gas molecules into a plasma state generates a high temperature that melts the PET bottle resin. By thoroughly studying the balance among the vacuum rate, gas amount, and electricity, we managed to develop a high-frequency plasma technology that achieves high-barrier performance without damaging the bottle.
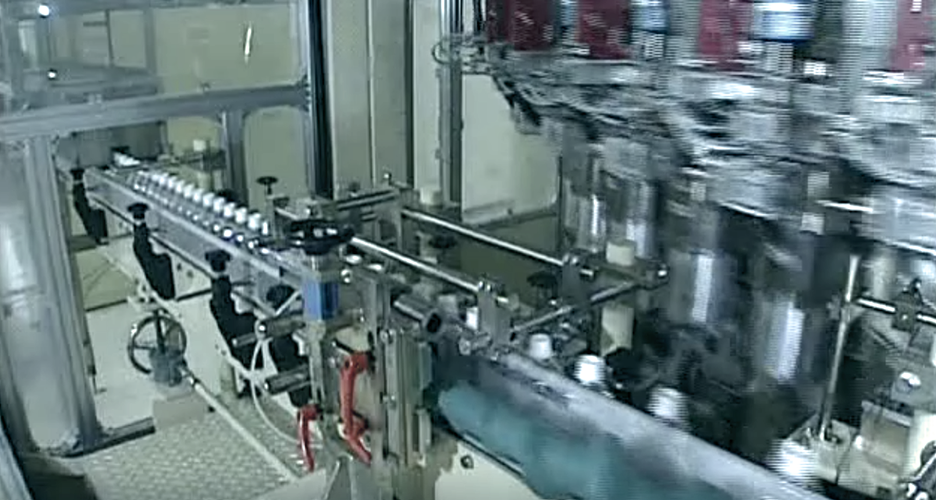
High barrier performance to retain carbon dioxide gas and water inside while blocking out oxygen.
The Mitsubishi DLC coating system was completed three years after the technical principle was conceived. The system achieves high productivity by depositing DLC film coatings in as little as 6 seconds per bottle, or from 12,000 to 18,000 bottles per hour.
With the advent of the system, DLC bottles came to be used for various other beverages and also non-beverage liquids previously sold in other types of containers. DLC-bottled hot green tea (350 ml) was released on the market, and DLC bottles of different sizes followed. DLC coatings are now applied in bottles containing products such as cooking oil and carbonated drinks (500 ml). In short, DLC technology has become indispensable in daily life.
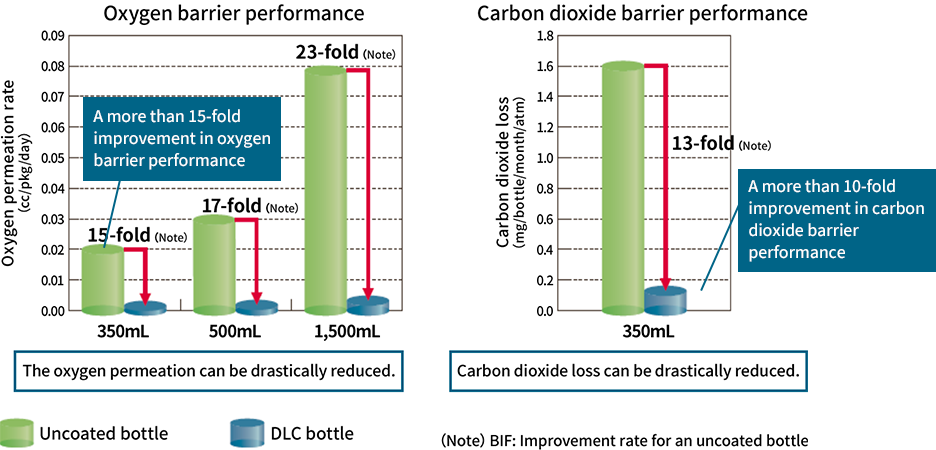
The emergence of DLC bottles drastically changed supermarket shelf spaces.
Many may wonder, “Can we tell a DLC bottle at a glance?” Most people cannot tell the difference. If you want to see what a DLC bottle looks like, go to a supermarket and look at the wine shelves. DLC coatings are used to guard the quality of most of the Japan-made wines bottled in plastic.
The wines in Japanese supermarkets used to be sold mostly in glass bottles or cartons. When DLC wine bottles appeared in 2010, these containers were changed to DLC bottles. The DLC wine bottle blocks oxidation and retains aroma and carbon dioxide gas. It also can be shaped into upscale designs that attract many beverage manufacturers.
In addition to full size 720 ml wine bottles, a 1.5 liter bottle is now on the market. This offers a significant advantage to retailers, as a glass bottle for the same volume would be too heavy. DLC bottles greatly contribute to the development of new products.
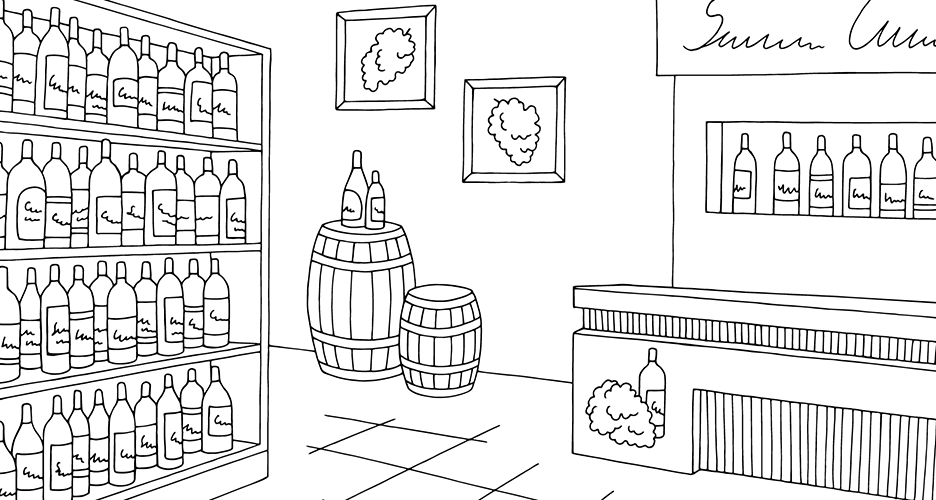
Make your life more fun and affluent with evolving diversified beverages
DLC coating technology is being applied to an expanding field of containers for products such as FOSHU (food for specified health use) beverages using tea catechin, Japanese sake, and coffee beans with appealing aromas.
The light weight and strength of PET bottles also offer logistic advantages. A new generation of 3-liter DLC PET bottles is now being developed to put those advantages to use.
Beverages with novel tastes and restaurant-quality flavors are emerging day after day, year after year. The carbon films in the DLC coatings protect these beverages as they flow through the supply chain to the everyday consumer.
Technological innovations from MHI-MS continue to spur the creation of delicious and joyful new beverages.
Strategic Innovation
R&D
- Research System and Development Base
-
Strategic Innovation
- The world’s first! A Next-Generation ERP to Realize the Roads of Tomorrow in Singapore
- Meeting the needs of global logistics! The EVOL box making machine enables the high-speed mass production of corrugated board boxes.
- Keep a drink delicious and fresh! A carbon coating that evolves PET bottled beverages.
-
From the research and development sites
-
Development Story
- Next-Generation Multistory Parking Lot installed underground in the inner-city - Birth of the Mitsubishi Cell Park (Two-Lift Type) -
- From the site of MC development, a new corrugated board box making machine that is responsible for the production of corrugated boxes that supports our lives and economy
- Closing in on the latest research on a tire inspection machine that underpins the growth of a motorized society.
-
Innovators
- A magnitude 7 earthquake is faithfully reproduced in every detail! “Advanced hydraulic and control technologies” to shake full-scale medium-rise buildings.
- Rapid, beautiful, economical! A newspaper offset press developed to lead the world.
- Generate novel experiences in large-scale facilities that inspire and amaze people and awaken them to new possibilities. Frontline “Moving Technology.”
-
Development Story
- Mitsubishi Heavy Industries Technical Review