Next-Generation Multistory Parking Lot installed underground in the inner-city - Birth of the Mitsubishi Cell Park (Two-Lift Type) -
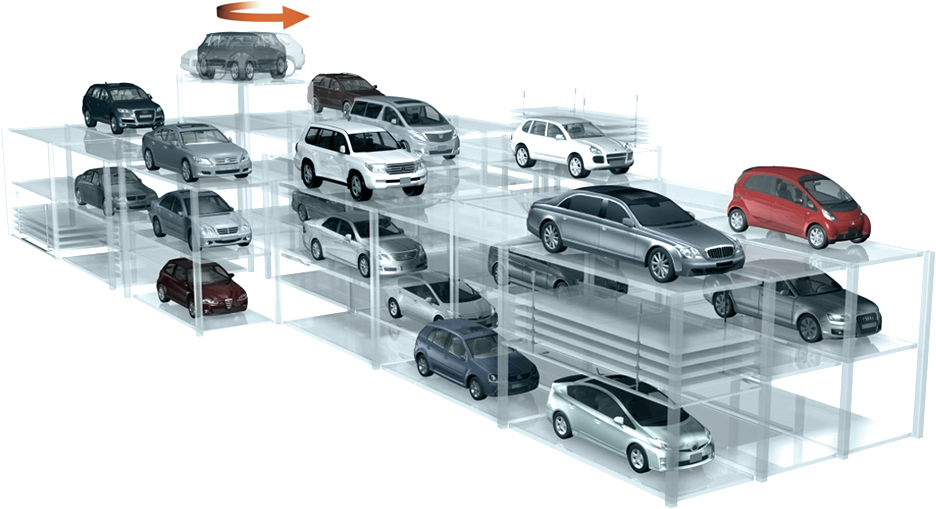
Story1
The evolution required to realize a cell park with higher parking efficiency
Multistory parking lots have become a key transportation infrastructure offering improved user convenience in commercial complexes and office buildings in inner cities.
Wide-ranging parking capabilities are required to enable the various functions of buildings. Important among them are the elimination of traffic backup during the loading and unloading of vehicles for busy users and the effective use of limited space in dense urban cores. Mitsubishi Heavy Industries Machinery Systems (MHI-MS) has been expanding its lineup of multi-level parking systems that deliver the capabilities now required.
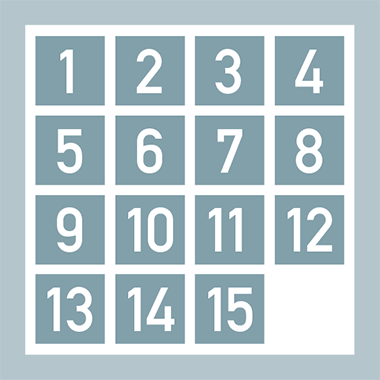
The pallet is transferred to the destination position through vacant cells, moving like a number in a number alignment puzzle.
Within this parking lineup, the Cell Park, our underground-type multi-level parking systems, is the optimal choice for narrow-footprint buildings. Cell Park offers high parking efficiency and flexible layouts, as well as a key transfer mechanism called the “horizonal circulation system.”
After the driver parks the car on the pallet (the steel tray that conveys the car) in the boarding/de-boarding zone, the lift transfers the loaded pallet to the underground parking space. As the pallet travels, it repeatedly shifts in lateral and vertical directions, finding the most efficient route to reach its destination.
With help from the advanced mechanical design and control technology, the system layout can be flexibly rearranged to achieve the optimal parking efficiency for the building serviced. Some Mitsubishi Cell Parks, for example, locate their parking cells away from the columns and walls of buildings, avoiding structural obstacles that have created difficulties in the past.
Story2
The system achieves double the car storage capacity of a conventional facility without keeping customers waiting.
What type of car park matches the requirements of a large-scale compound building in an inner city?
Back in 2014, MHI-MS launched a project to introduce the Cell Park into a large-scale compound building in central Tokyo. A further evolved Cell Park was completed in 2016.
K.K, a planner and designer in the project, relates his experience:
“The client wanted a car park that would never keep customers waiting. They proposed a system that loaded and unloaded cars by dividing the traffic at the loading entrance and unloading exit into two lanes. We developed the Cell Park (Two-Lift Type) to meet their request.”
The target parking capacity was about 70 vehicles, almost twice the capacity of a conventional cell park. As a parking facility to be installed in a large-scale compound building in the inner-city, the Cell Park had to accommodate larger vehicles produced by overseas carmakers.
Our conventional product, the large-scale IPS parking facility, consisted of two gateways and a two-lift configuration as standard. The IPS could load and unload simultaneously, which gave it the highest processing capacity in our product lineup at that point of time. But for the inner city project in Tokyo, we soon realized that the IPS was a poor fit for the building space where the system was to be installed.
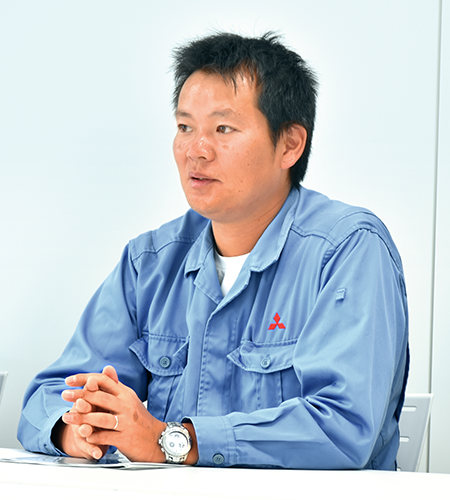
Parking System Design No. 1 Section
Parking System Engineering Department
Infrastructure Facilities Business Division
The key lies in the control system to solve the loading efficiency puzzle.
“The demand trend now calls for parking capacities of up to 50 to 100 vehicles, even in sites too narrow for conventional parking facilities,” says K.K. “Soaring land prices in urban areas are tightening the capacity squeeze. We see this tendency in many projects, not just the one I worked on here.”
The Cell Park, with its space-saving design and excellent parking efficiency, was the optimal solution to the client’s needs. There were many challenges, of course, in actually delivering the system.
The conventional Cell Park had one loading/unloading gate and worked together with only one lift.
“From a design viewpoint, it wouldn’t have. been so difficult to simply double the storage capacity,” says S.T, the chief of mechanical design from the beginning.
“The difficulty came when we began to work on the control system coding to rapidly move the cars as they loaded and unloaded in and out of the cell. We had to solve the puzzle for a moving Two-Lift system, in addition to the very complicated puzzle of the vehicle transfer.”
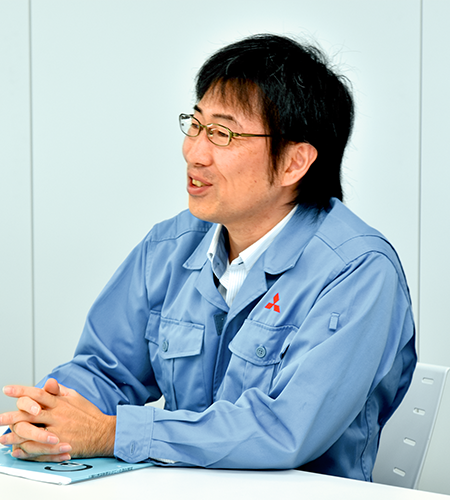
Parking System Design No. 3 Section
Parking System Engineering Department, Infrastructure Facilities
Business Division
Story3
Construction of the Two-Lift Control System, a challenge equivalent to developing a new product
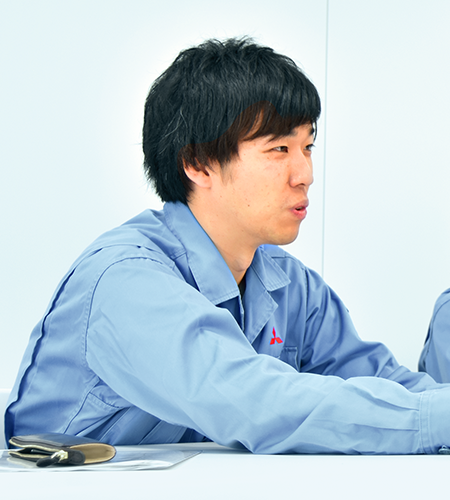
Parking System Design No. 3 Section
Parking System Engineering Department, Infrastructure Facilities
Business Division
H.F, an engineer assigned to the electrical and control design, described some of the difficulties the project team faced in development:
“For a one-lift system, all we need to do is sequentially process the task for each car individually. For the two-lift system, we have to simultaneously process multiple tasks from each of the boarding de-boarding zones.”
“Simply scaling up the software for the small-scale system is likely to cause system errors. Instead we had to reconstruct both the hardware and software for the control system almost from scratch.”
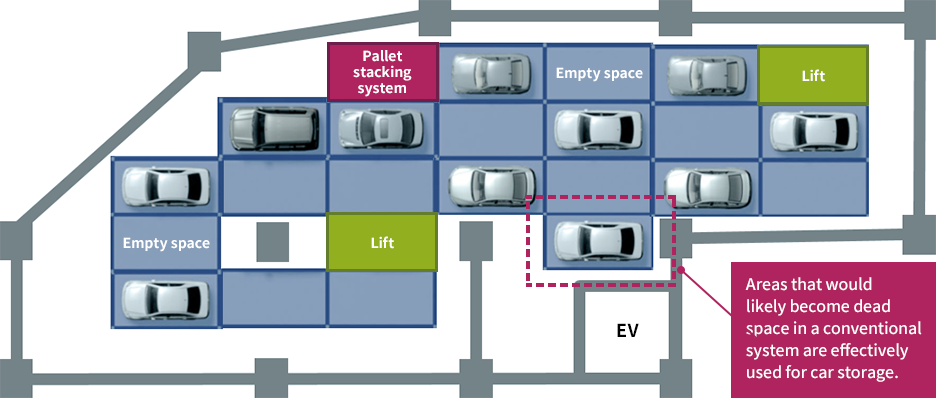
The outstanding features are a high car storage capacity and flexible layout.
The loaded parking cells in Mitsubishi Cell Park move laterally and vertically through vacant cells in a grid system. If only one cell is vacant, any of the parked vehicles can be moved through the system to the boarding/de-boarding zone. The advanced control system and mechanical design realize a flexible layout and the maximum car storage possible in the site area.
The core technical criterion to meet in a multistory parking lot is a loading/unloading latency time of no more than 5 minutes. Any system that fails to cross this hurdle is a non-starter.
Determined to reach the same level in the new product developed, H.F insisted on collaborating with software engineers from the Research & Innovation Center at Mitsubishi Heavy Industries, Ltd., external specialist manufacturers, and core members of his own company. A team specialized in control system development with diversified know-how resolved the issues one by one.
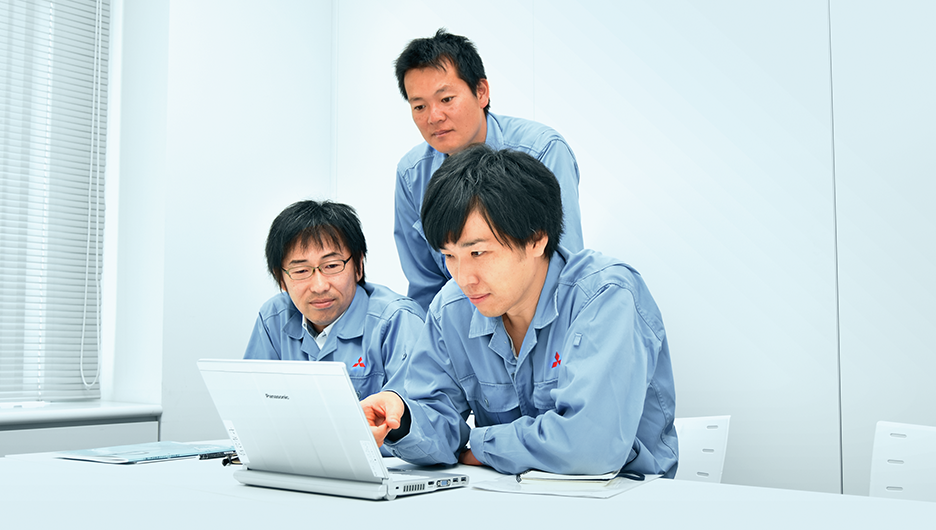
The most difficult problem was to rapidly and safely transfer the cars being loaded and unloaded at the same time. The members of the Research & Innovation Center proposed a "constraint programming technology" for the processing of multiple tasks.
This is a state-of-the-art algorithm to automatically calculate the shortest route for loading and unloading while assuring safe processing and setting system limits such as the maximum electric power that can be simultaneously consumed, the maximum number of devices that can be simultaneously actuated, and the prohibition of dangerous actuations that can result in pallet collisions at intersections, etc.”
For double assurance, the development team designed a dedicated emulator to verify the software operation. Once the emulator was installed, they requested the engineers from other ITS (Intelligent Transportation System) departments to review it.
Their aim was to utilize the resources of the whole of MHI-MS to enhance the performance, safety, and reliability of the control system at every stage from the detailed design work to final verification.
Story4
A human engineering approach to respond to revised safety design legislation
A Pattern Design that enables everyone can identify "Safe Areas" intuitively.
One more hurdle had to be crossed in this project.
In 2015, the Ministry of Land, Infrastructure and Transport issued a revised Parking-place Regulation to strengthen the safety of mechanical parking systems, along with a set of certification criteria for safety features. The project team had to meet the new safety standard.
MHI-MS and other multistory parking lot manufacturers had applied various safety countermeasures over the years with the goal of achieving a zero-accident rate in their facilities. The revised law required even stricter safety measures.
K.K, the chief of the building and pattern design, took on the task of improving the safety of the boarding/de-boarding zones.
If the mechanical device is actuated while a person remains in a boarding/de-boarding zone, the person might accidentally get caught in the machinery. The new standard requires that users are clearly shown the safety evacuation area for worst-case risk situations.
“I consulted with the engineers in the Pattern Design Department of Mitsubishi Heavy Industries, Ltd. in order to adopt ergonomic knowledge in the pattern design. In the safe area, for example, I adopted line markings in universal colors and pictograms that anyone could understand at a glance. Our team also went through a series of repeated adjustments and verifications to find the optimal sizes for signs and characters that could be understood easily by instinct.”
Markings for the emergency stop button and safety evacuation area in the boarding/de-boarding zone
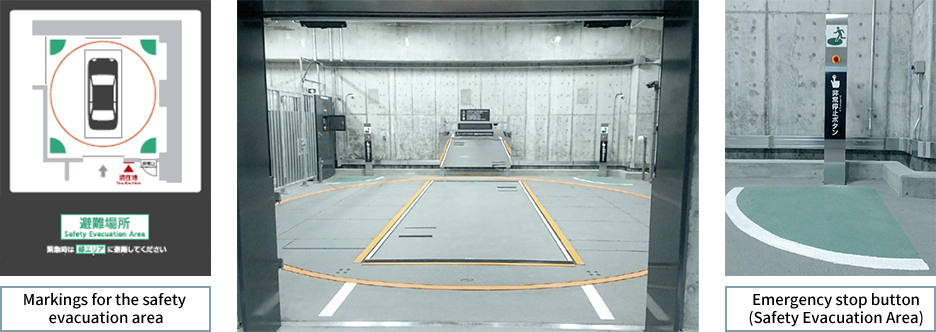
Accident factors in the boarding/de-boarding zones were resolved through collaborative thinking.
A host of new modules were also added for safety verification, including cameras, monitors, and sensors of various types. Beyond the extra safety gained with these modules, the mechanical design chief S.T also integrated safety functions in the device used to turn the pallets in the loading boarding/de-boarding zone.
S.T studied the adoption of a conventional turning device that turns with the pallet lifted. To reduce the risk of accidents, he consulted with a senior expert designer to adopt a table-type turning device that turned together with the floor. Earlier in the design process, space constraints forced him to forgo a table-type device of the same type.
“Through repeated brainstorming sessions we came up with the idea of aligning the major diameter of the turning device and the diagonal dimension of the pallet. This design allowed us to not only eliminate accident risks, but also turn the pallet with the minimum required configurations.”
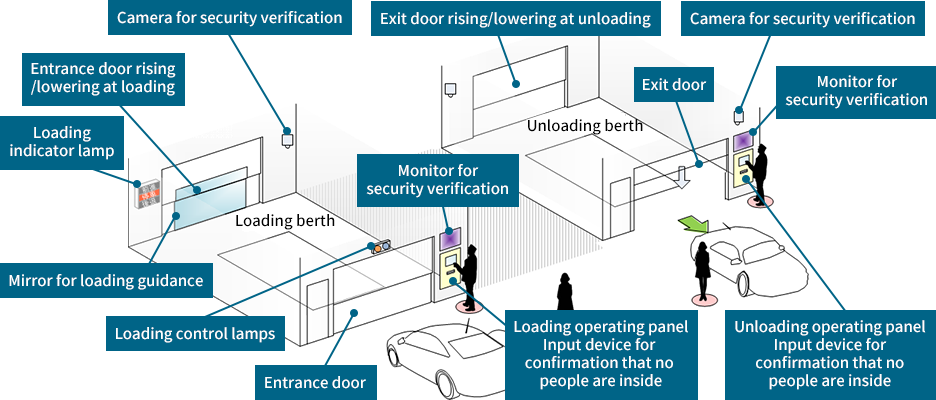
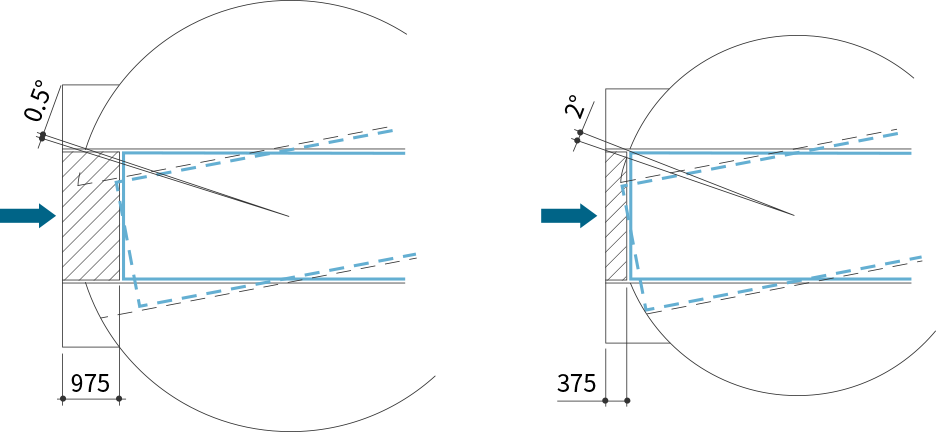
The ascending/descending deck (hatched area) lowers to a position where it will not interfere with the turning device, and the table turns together with the pallet. By matching the diameters of the turning device and diagonal dimension of the pallet, the dimension of the ascending/descending deck could be reduced by about 60% and the permissible deviation of the turning stop could be quadrupled. These improvements realized a safer, more space-saving design for the turning device.
Story5
To a coming generation of transportation infrastructures that connect city, cars, and people
Building design, mechanical design, and control design. The development collaboration of an All-Mitsubishi Team across department boundaries has brought forth fruit. A new iteration of the MHI cell park, the Mitsubishi Cell Park (Two-Lift Type), was born in March 2016, two years after the project commenced. The new facility is the very first from MHI-MS to fully comply with the revised law of safety countermeasures.
The unique mechanism, safety aspects, and design accommodated to central Tokyo were highly evaluated by the owners of the facility, as well as the construction companies involved in installation. No failures or troubles with the control system, the linchpin component, have ever occurred. H.F smiled when describing his relief.
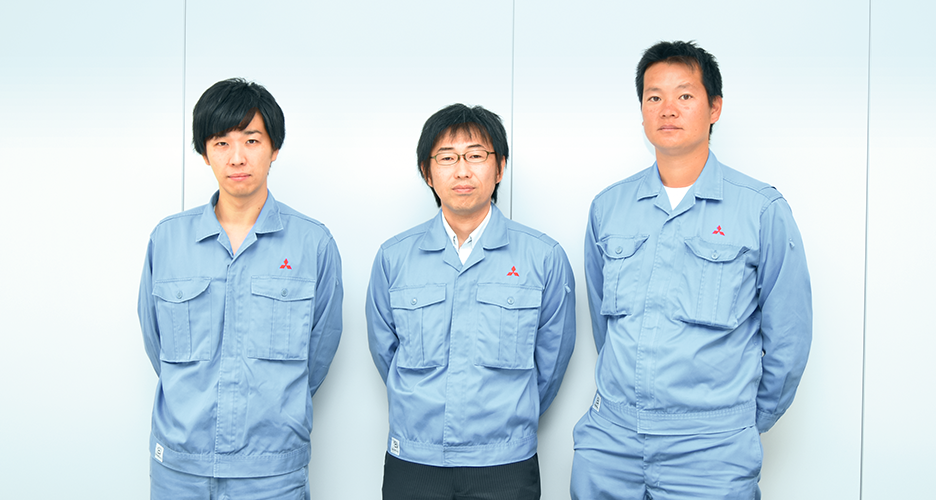
Car parking requirements in a changing society
The Cell Park (Two-Lift Type) was born through our whole-hearted efforts to satisfy the project with all of the strengths and resources at our disposal. The lineup achieved meets wider-ranging needs than anything before it.
Large-size redevelopments are now progressing in city centers. The demand for this Cell Park (Two-Lift Type) is expected to rise, especially for projects that require flexible layouts enabling the reuse of underground spaces. Multiple projects of this type are already underway.
Population density continues to increase in urban areas. As the car society comes to a drastic turning point with the advent of electric vehicles, automated driving, and the like, the multi-level parking systems will advance further as an important transport infrastructure in city centers.
MHI-MS continues to tackle the challenge of developing next-generation products to connect changing cities, cars, and people.
Development Story
R&D
- Research System and Development Base
-
Strategic Innovation
- The world’s first! A Next-Generation ERP to Realize the Roads of Tomorrow in Singapore
- Meeting the needs of global logistics! The EVOL box making machine enables the high-speed mass production of corrugated board boxes.
- Keep a drink delicious and fresh! A carbon coating that evolves PET bottled beverages.
-
From the research and development sites
-
Development Story
- Next-Generation Multistory Parking Lot installed underground in the inner-city - Birth of the Mitsubishi Cell Park (Two-Lift Type) -
- From the site of MC development, a new corrugated board box making machine that is responsible for the production of corrugated boxes that supports our lives and economy
- Closing in on the latest research on a tire inspection machine that underpins the growth of a motorized society.
-
Innovators
- A magnitude 7 earthquake is faithfully reproduced in every detail! “Advanced hydraulic and control technologies” to shake full-scale medium-rise buildings.
- Rapid, beautiful, economical! A newspaper offset press developed to lead the world.
- Generate novel experiences in large-scale facilities that inspire and amaze people and awaken them to new possibilities. Frontline “Moving Technology.”
-
Development Story
- Mitsubishi Heavy Industries Technical Review