Meeting the needs of global logistics!
The EVOL box making machine enables the high-speed mass production of corrugated board boxes.
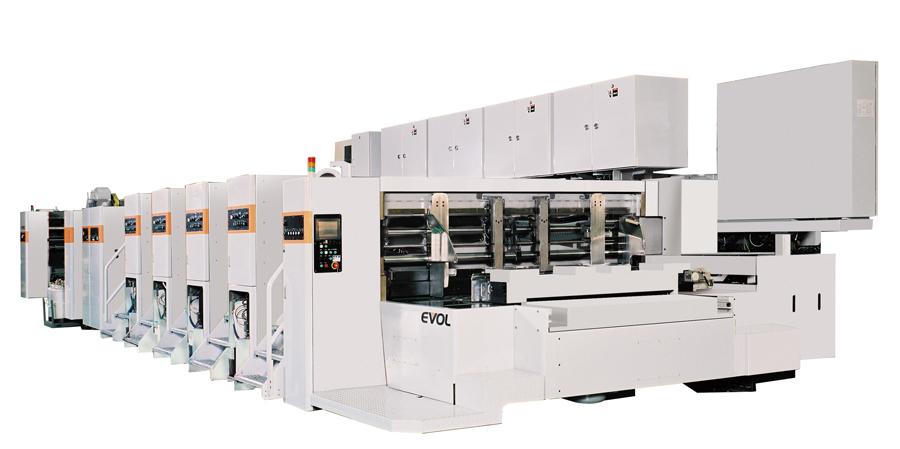
A history spanning more than 60 years! The machine used to manufacture corrugated board box, which is one of the most familiar pieces of logistics infrastructure.
With the rapid spread of the Internet commerce, global demand for logistics is rapidly increasing. You probably use these services regularly to deliver a variety of products to your home or office.
Everyone knows that products cannot be delivered without corrugated board boxes, their significant properties are light, sturdy, easy to handle, and recyclable.
Mitsubishi Heavy Industries Machinery Systems (MHI-MS) has been developing and manufacturing box making machines for corrugated board boxes since 1955. As a supplier of box making machines, we have abundant experience in supporting logistics in Japan and the world for more than 60 years.
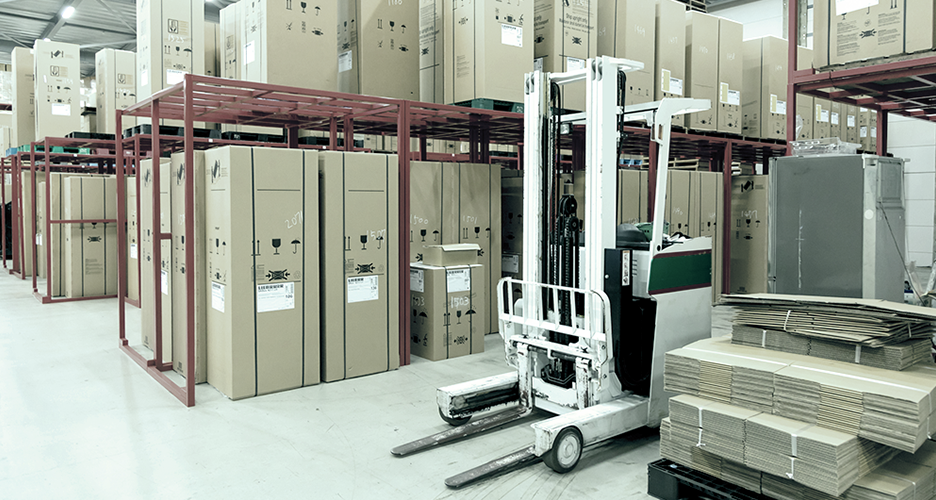
Highlights!
Most people know little about box making machine or the mechanisms that make it work.
Paper converting machinery is roughly classified into two categories.
- Corrugator
- Makes large sheets of corrugated board from converting paper (rolled paper).
- Box making machine
- Prints on corrugated board sheets (blanks) made by corrugator, and forms them into corrugated board boxes.
MHI-MS develops and manufactures these paper converting machineries. Here we provide a close-up look at the box making machine and its features. We begin below brief explanation of the basic mechanism of the machine, and box making process.
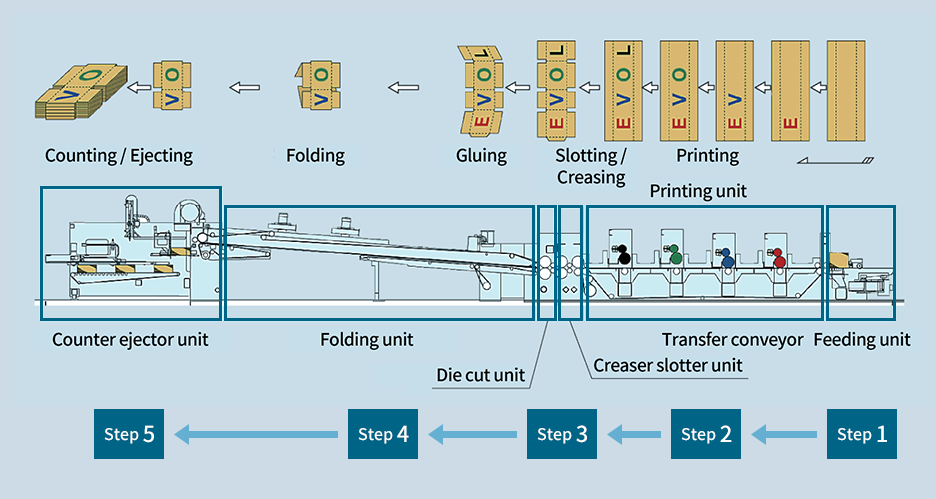
Corrugated board box making process
Step1 : Feeding unit
Feed flat corrugated board sheets (blanks).
Step2 : Printing unit
Print necessary information and/or design on upper surface of the sheets while transferring the sheets on the transfer conveyor.
Step3 : Creaser slotter unit
Crease and slot the sheets to fold properly.
Step4 : Folding unit
Glue and fold the sheets to form boxes.
Step5 : Counter ejector unit
The boxes are piled up while counting the produced number, and the boxes are ejected for each predetermined number.
As described above, a box making machine that performs everything from the printing of sheets to the forming of boxes with a single machine has a unique function of producing a large number of corrugated boxes at low cost and at high speed.
The world's fastest box making machine! What are the differences between the latest EVOL and conventional models?
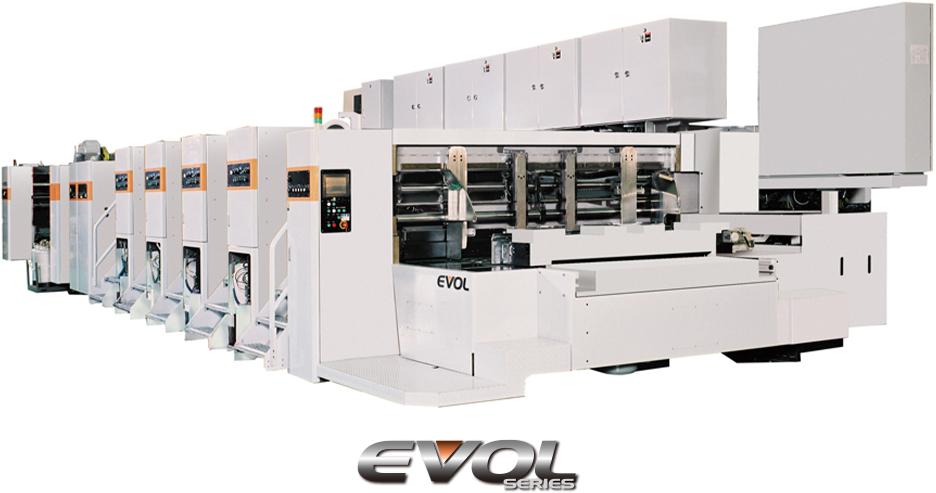
Continuous pursuit of productivity, box quality, and operability
The EVOL series, which MHI-MS released in 2003, has been a long-selling hit machine all over the world. The main reasons for this are the high box quality and high production efficiency that conventional box making machines cannot achieve.
Point1 : High productivity, high efficiency
EVOL has achieved the world's fastest production speed (400 blanks per minute), 1.6 times that of the previous model.
In addition, by adopting the automatic setup function, the machine setting change time for each type of box produced was reduced by 60%, and the production efficiency was also greatly improved.
Point2 : Ability to handle a wide variety of boxes
The EVOL series enables the production of boxes with a wide range of sheet dimensions, from 220 mm to 1,150 mm in the flow direction, by aligning the different machine sizes.
In addition, by adopting unique servo control system and stacking method, boxes of various sizes can be stacked stably at high speed.
Point3 : High quality, high precision
The use of one piece suction belt in the transfer conveyor unit for the first time in Japan has eliminated printing deviation during high-speed operation and for short sheets, resulting in high printing register accuracy.
It also supports the production of high-quality, high-precision boxes by reducing ink and sheet losses during ink replacement and by achieving high folding accuracy that can be applied to automatic casers.
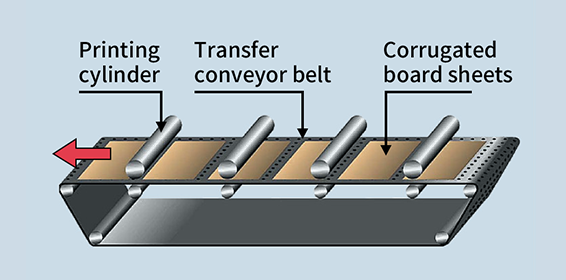
One piece suction belt type transfer conveyor with high sheet conveying accuracy
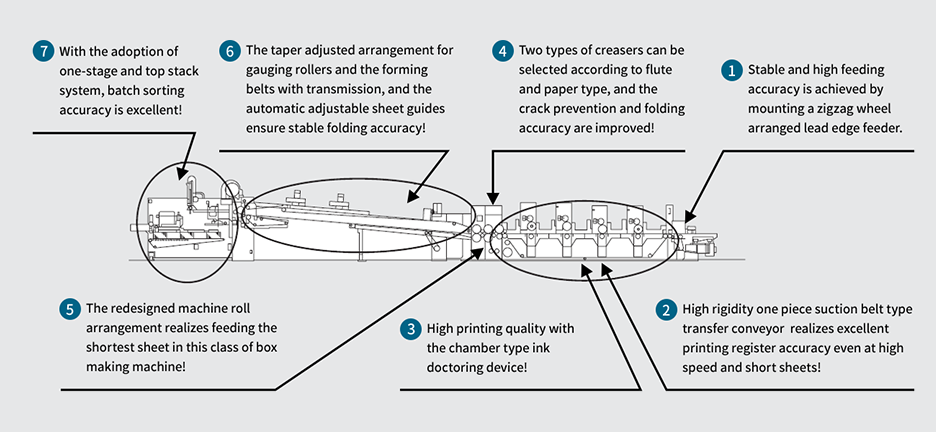
Since its launch, the EVOL series, with its dramatically higher performance, has met the needs of overseas customers for mass production and high-speed production, as well as the needs of Japanese customers for small-lot, high-quality boxes.
Climbing to a higher stage! What is a production system that doubles production capacity?
In 2018, the latest EVOL was born.
In recent years, the Internet commerce has expanded rapidly not only in Japan but also worldwide.
With the change in the distribution system, such as the spread of convenience store delivery, the demand for "small box" has increased, and the ability to produce them at higher speeds and in larger quantities has been required for box making machines.
The mission was to go for an unprecedented spec: to double production capacity from the world's fastest 400 blanks per minute to 2 times 800 blanks per minute.
Therefore, we worked on the development of a “2-Up Production” system. In this method, two boxes are manufactured from one corrugated board sheet.
That is, as shown in the figure below, printing for two boxes, creasing and slotting are performed on one sheet. Then, after the gluing, folding, forming, and the stacking process, it is finally divided into two in a subsequent process.
This method will theoretically double the production capacity.
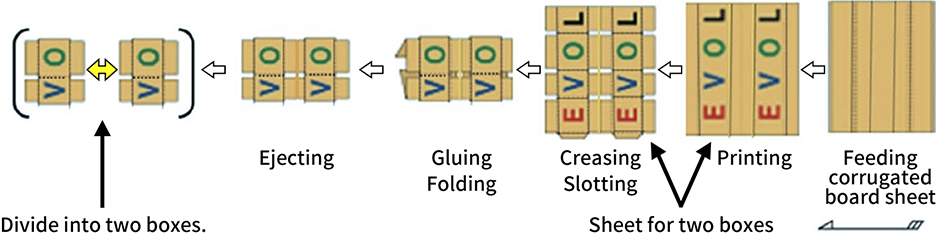
The newly developed “Dual Slotter Unit” solves a long-standing challenge.
With 6 slotter knives, high precision slotting is achieved for 2 boxes at the same time!
When we tried to make two boxes out of one sheet, the processing of the center slot holes was a major obstacle.
The outer slots may be cut out, but in the prior art, the center slot holes need to be punched out with a cutting die at the die cut unit after the creaser slotter unit.
In other words, there had been a concept of "2-Up Production" for a long time, but as long as a cutting die was used to form the center slot holes, the setup time for changing the cutting die and the arrangement and maintenance of many kinds of cutting dies became bottlenecks, and practical application was not achieved.
The key to putting the "2-Up Production" to practical use was a new technology that automatically cuts out the center slot holes with multiple slotter knives.
The newly developed “Dual Slotter Unit” mounted on the EVOL has 2 slotter devices. By adding this unit after the creaser slotter unit, there are now three slotter devices instead of one.
Since one slotter device has two knives, the slots are cut out by dividing the slots little by little with a total of six knives for one sheet, and highly accurate slots can be realized.
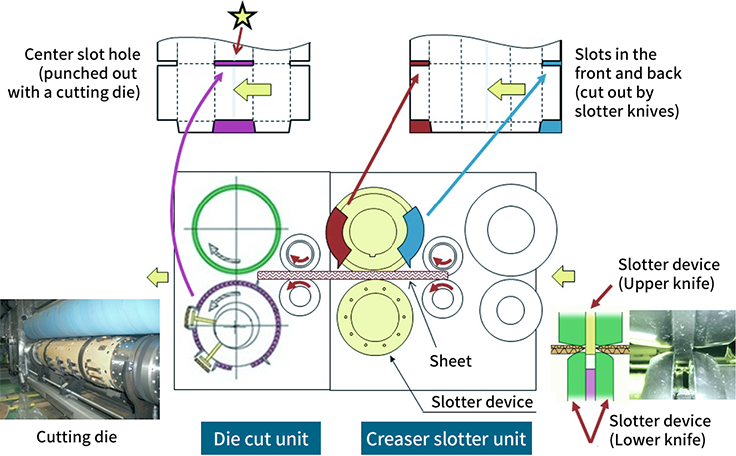
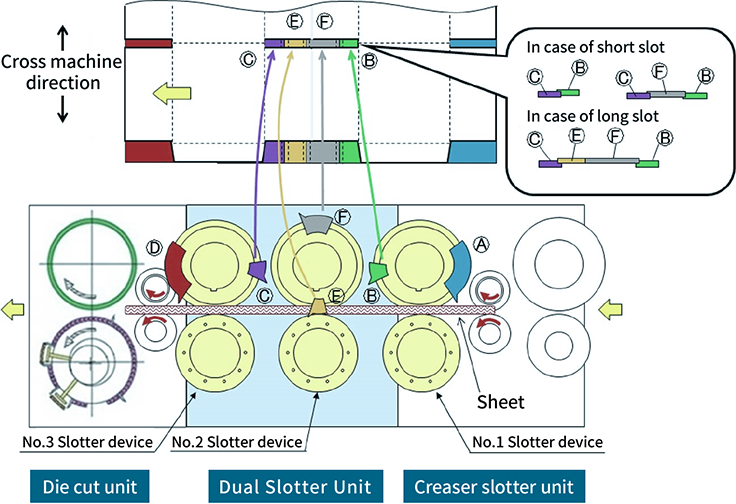
MHI-MS has succeeded in putting the "2-Up Production" into practical use for the first time in the world by utilizing its technical capabilities and experience.
However, it was not possible to achieve the 2-up production simply by adding the dual slotter unit.
A long period of study and verification has been repeated on the design of placing 2 slotter devices in a narrow space, and on the control mechanism for slotting with an accuracy of less than 0.5 millimeters.
Finally, by improving the accuracy of the sensor that determines the cutting point precisely, we have established a unique technology for slotting a single slot with multiple knives with high accuracy.
Another major problem in practical application was the generation of a large amount of scattering scraps by slotting on a large amount of corrugated board sheets at high speed. This is because the box will be defective if the scrap gets into the glued part of the box.
To cope with the problem of scattering scraps, scrap guides and air blows were installed at appropriate position, and the length and arrangement of the slotter knifes were optimized.
As a result of trial and error using all the experience and technology that we have cultivated over more than 60 years, we have succeeded in the practical application of the “2-Up Production”.
Following the North American market, also received orders in the European market!
Succeeded in one order after another. The lineup further expands.
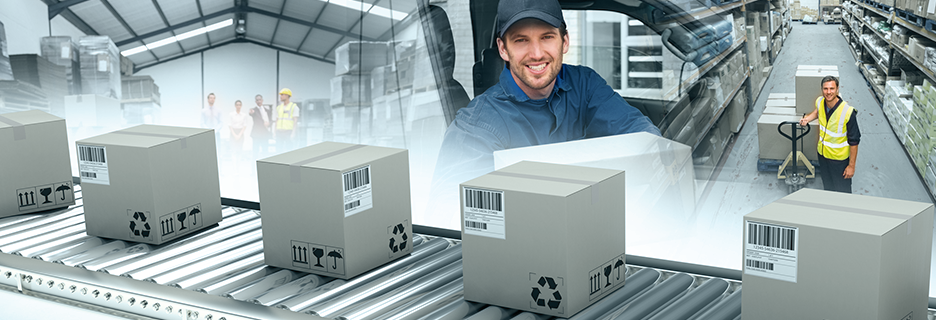
The latest EVOL with a "Dual Slotter Unit" went on sale in 2018, and has won acclaim in the North American market, where mass production takes priority.
For one customer, production increased from about 300,000 boxes per day to about 360,000 boxes per day with the introduction of the latest EVOL.
In addition, there have been many inquiries and orders not only from North American customers but also from European customers recently, and the response in the global market has been strong.
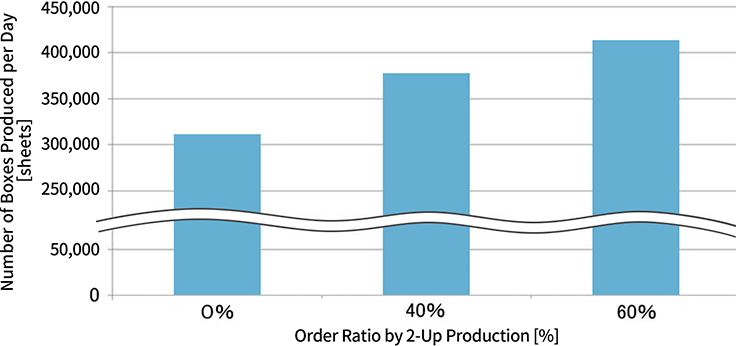
Simulation of daily box production
It can be seen that as the order ratio of 2-up production increases, the daily box production increases significantly.
MHI-MS aims to expand its product lineup to respond to the diverse needs of the world market, such as low-cost box making machines with limited functions in addition to high-performance, high-speed box making machines.
PRODUCTS COVERED
Strategic Innovation
R&D
- Research System and Development Base
-
Strategic Innovation
- The world’s first! A Next-Generation ERP to Realize the Roads of Tomorrow in Singapore
- Meeting the needs of global logistics! The EVOL box making machine enables the high-speed mass production of corrugated board boxes.
- Keep a drink delicious and fresh! A carbon coating that evolves PET bottled beverages.
-
From the research and development sites
-
Development Story
- Next-Generation Multistory Parking Lot installed underground in the inner-city - Birth of the Mitsubishi Cell Park (Two-Lift Type) -
- From the site of MC development, a new corrugated board box making machine that is responsible for the production of corrugated boxes that supports our lives and economy
- Closing in on the latest research on a tire inspection machine that underpins the growth of a motorized society.
-
Innovators
- A magnitude 7 earthquake is faithfully reproduced in every detail! “Advanced hydraulic and control technologies” to shake full-scale medium-rise buildings.
- Rapid, beautiful, economical! A newspaper offset press developed to lead the world.
- Generate novel experiences in large-scale facilities that inspire and amaze people and awaken them to new possibilities. Frontline “Moving Technology.”
-
Development Story
- Mitsubishi Heavy Industries Technical Review