Press Information
"MEISTeR" Remote Control Robot Completes Demonstration Testing At Fukushima Daiichi Nuclear Power Station
-- Performs Decontamination Work and Concrete Core Sampling --
-- Performs Decontamination Work and Concrete Core Sampling --
Tokyo, February 20, 2014 - Mitsubishi Heavy Industries, Ltd. (MHI) has begun demonstration testing of its "MEISTeR," a remotely controlled robot, at the Fukushima Daiichi Nuclear Power Station operated by Tokyo Electric Power Company, Incorporated (TEPCO). The highly advanced two-armed MEISTeR - named from "Maintenance Equipment Integrated System of Telecontrol Robot" - has now completed demonstration testing of decontamination work and concrete core sampling. The robot was developed to perform maintenance, repair and other tasks at disaster or severe accident sites. Its work performance at the site has confirmed the robot's sophisticated work capability, and plans now call for the MEISTeR to assist in recovery work at the plant by performing tasks including decontamination and sampling.
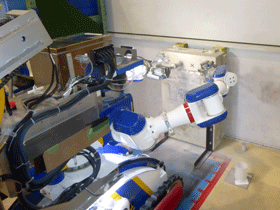
Whereas most disaster response robots available until now have primarily performed inspection, maintenance and similar tasks relying on cameras, etc., the MEISTeR can handle a broad array of tasks by changing the tools attached to its arm ends. In addition to inspection and maintenance, the MEISTeR can perform decontamination work, concrete core sampling, cutting of obstacles blocking pathways, etc.
Each robot arm has seven freely articulating joints. By attaching a different tool to the left and right arms, two types of work can be performed simultaneously: for example, grasping an item with one arm and cutting with the other. Inside a nuclear power plant, the MEISTeR is capable of tasks including concrete drilling, cutting of handrails and piping, removal of obstacles, decontamination, repair work, etc.
Inside the Unit 1 plant at the Fukushima Daiichi Nuclear Power Station, the MEISTeR carried out demonstration testing of two decontamination processes since late last month: one whereby radioactive material in the plant is sucked up through a dedicated nozzle, and another in which a jet of abrasive blast material is used to scrape off a thin layer of a contaminated surface. It also confirmed travel capability inside the plant's narrow passageways, and performed concrete core sampling aimed at investigating the level of contamination inside the reactor building. The latter process involved taking concrete samples from the structure's walls and floor, at a depth of approximately 70 millimeters (mm) from the surface; this was carried out by remotely controlling the robot's arms, to which a specially developed drill and hand were attached. Concrete core sampling is now also scheduled for the Unit 2, to determine the level of contamination of the operating floor.
Going forward, MHI intends to proceed with development of even more sophisticated remote control robots and tool attachments of various kinds, to meet the diverse needs of the Fukushima Daiichi Nuclear Power Station and other plants.
General specification of MEISTeR
Dimension (length x width x height): 1,250mm x 700mm x 1,300mm
Weight: 440 kg
Moving system: Using 4 crawlers
Moving speed: 2 kilometers per hour
Travelling performance: Capable to climb up to 40-degree angle slopes and steps with up to a 220mm gap.
Communication: Wired and wireless
Electric source: Wired and buttery (go for 2 hours on a single charge)
Robot arms: Double arms with 7-axis control system. Each arm can carry objects weighing up to 15kg.
MEISTeR performing suction decontamination work inside the Unit 1
at Fukushima Daiichi Nuclear Power Station
Travel testing on an entry slope to the Unit 2 operating floor
(photographed during in-house demonstration testing)
About MHI Group
Mitsubishi Heavy Industries (MHI) Group is one of the world’s leading industrial groups, spanning energy, smart infrastructure, industrial machinery, aerospace and defense. MHI Group combines cutting-edge technology with deep experience to deliver innovative, integrated solutions that help to realize a carbon neutral world, improve the quality of life and ensure a safer world. For more information, please visit www.mhi.com or follow our insights and stories on spectra.mhi.com.