Press Information
Joint Demonstration of Automated Picking Solution Launched in Collaboration with Kirin Group
-- Proposal of Logistical Solution for Manual Labor Dependency and Operator Shortages in Beverage Warehouses --
-- Proposal of Logistical Solution for Manual Labor Dependency and Operator Shortages in Beverage Warehouses --
Tokyo, November 21, 2022 – Mitsubishi Heavy Industries, Ltd. (MHI) and Mitsubishi Logisnext Co., Ltd., a global player within MHI Group, engaged in logistic machinery and solution business, will launch joint demonstration of an automated picking solution for beverage warehouses in collaboration with Kirin Beverage Co., Ltd. and Kirin Group Logistics Co., Ltd. from the end of this month.
The demonstration includes establishment and verification of MHI’s automated picking system’s operating processes at “LogiQ X Lab”. The demonstration facility is located within Yokohama Hardtech Hub (YHH), a co-creation space operated by MHI in Yokohama. The ultimate aim is to install automated picking solutions(Note1) developed by MHI Group in beverage warehouses, which typically rely heavily on manual labor, placing a burden on logistics operators. The joint demonstration will continue through the end of June 2023.
Until now, warehouse workers have borne the bulk of responsibility for pursuing increased efficiency in their picking operations. Going forward, with MHI Group’s automated picking solutions, automation and intelligence can be introduced into the picking process through application of the “ΣSynX” (Sigma Synx) solution concept(Note2) currently under development by MHI. Optimized engines and an integrated control system, all developed in-house, together enable efficient coordination of multiple automated guided forklifts (AGFs), automated guided vehicles (AGVs) and palletizers(Note3). This results in fewer picking and transfer operations, optimized picking processing, and higher throughput.
Within Kirin Group, automation is steadily being introduced on production floors, but logistics in the company’s warehouses continue to rely heavily on work performed by manual labor and use of manned forklift trucks. The need to improve the work environment, especially through measures for picking heavy loads, and shortages of logistics operators, pose significant challenges. In the demonstration now underway, AGFs, AGVs and palletizers are being coordinated under Kirin Beverage’s warehouse operation conditions, and optimized control under ΣSynX is being verified in a quest to solve the challenges inherent in warehouse distribution with optimal safety.
Going forward, through the coordination with Kirin Group in this demonstration program, MHI Group will continue to work to solve the diverse distribution challenges faced by the beverage industry.
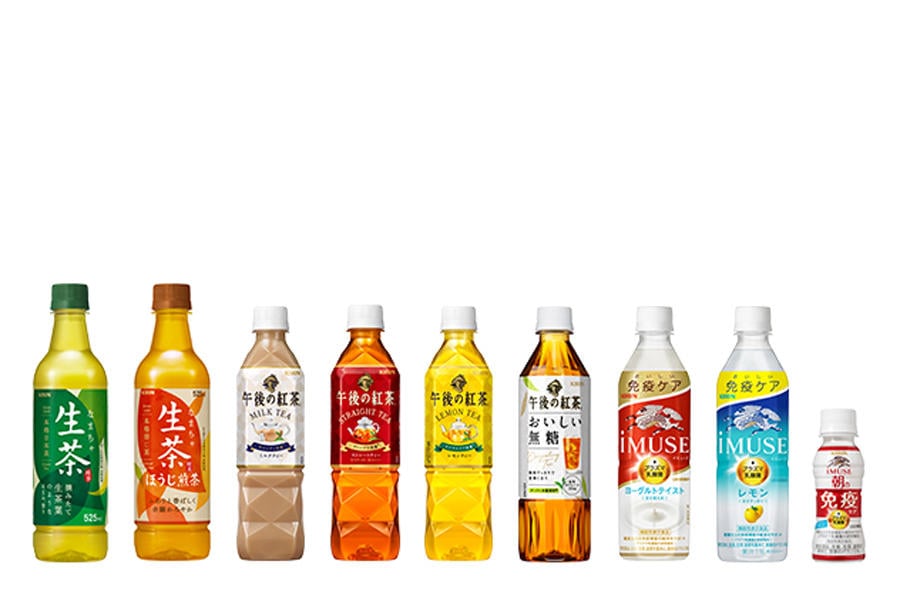
Kirin Beverage’s core product lineup
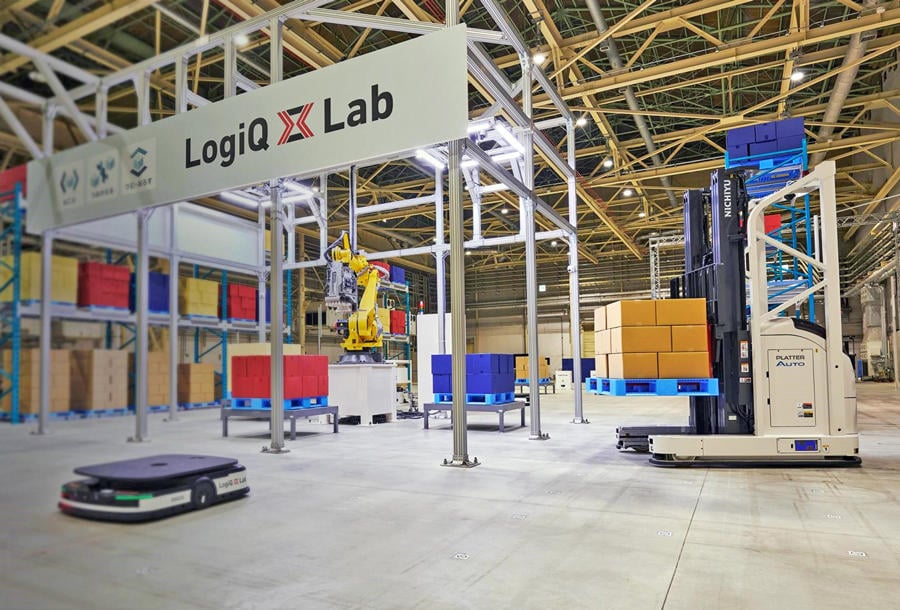
“LogiQ X Lab,” a demonstration facility at YHH
- 1For details, refer to: https://www.mhi.com/news/22083102.html
- 2ΣSynX is MHI’s standard platform for synchronizing and coordinating various types of machinery systems. It consolidates a host of digital technologies that enable optimized operation by making machinery systems intelligent.
- 3A palletizer is a device that performs automated placement and stacking of products, such as beverage cases, on pallets.
【Overview of the Joint Demonstration】
■ Implementation period: November 2022 to June 2023
■ Demonstration site: LogiQ X Lab demonstration facility at MHI’s Yokohama Hardtech Hub (YHH)
■ Items included in the demonstration:
- Verification of MHI’s automated picking solution under Kirin Beverage’s warehouse operating conditions
- Proposal of areas of the warehouse best suited to automation or manual labor; establishment of operating processes
- Proposal of equipment and system specifications for Kirin Beverage’s warehouses
■ Major characteristics of MHI’s automated picking solution
- Automated picking system centered on AGFs
In this fully automated work system, AGFs supply items removed from storage shelves to AGVs and palletizers. After picking, finished items are retrieved by AGV and AGF and transferred to storage shelves. - Proposal of the optimal equipment configuration through logistics simulation prior to system adoption
Logistical flows are simulated prior to system installation based on Kirin Beverage’s historical picking data. A proposal is then made of the optimal equipment configuration and layout. - Realization of optimal equipment coordination
AGFs, AGVs and palletizers are coordinated efficiently through use of MHI’s integrated warehouse control system. The adoption of optimized logic responds to the customer’s needs using the minimal number of palletizing operations.
<Conventional picking flowchart>

<Automated picking flowchart>
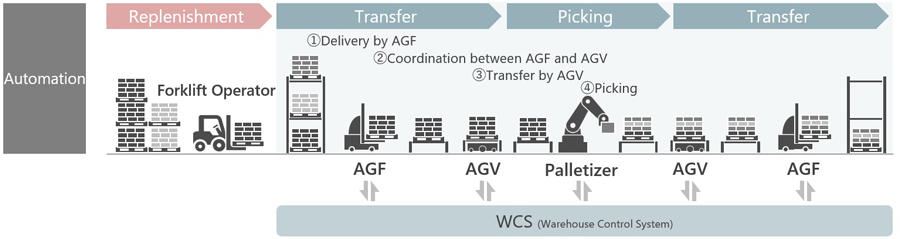
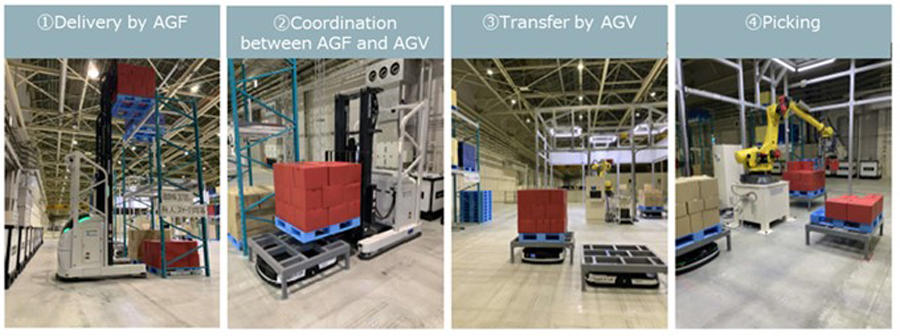
About MHI Group
Mitsubishi Heavy Industries (MHI) Group is one of the world’s leading industrial groups, spanning energy, smart infrastructure, industrial machinery, aerospace and defense. MHI Group combines cutting-edge technology with deep experience to deliver innovative, integrated solutions that help to realize a carbon neutral world, improve the quality of life and ensure a safer world. For more information, please visit www.mhi.com or follow our insights and stories on spectra.mhi.com.