Press Information
MHI Group Presents "Best Innovation 2024" Awards for Products and Activities that Contribute to Solving Social Issues
-- Promote the Realization of a Sustainable Society through Further Innovation --
-- Promote the Realization of a Sustainable Society through Further Innovation --
・ A total of 21 awards presented for innovative products and services that contribute to solving social issues such as carbon neutrality and digitalization
・ Group-wide efforts are underway to encourage innovation and raise awareness of environmental conservation
Tokyo, February 3, 2025 - Mitsubishi Heavy Industries, Ltd. (MHI) has presented its "Best Innovation 2024" awards to 21 products, technologies and services that recognize efforts related to the development and practical application of solutions to help resolve social issues. These awards have been handed out annually since 2003, with the aim of encouraging innovation and raising awareness of the need to reduce environmental impact throughout the entire Group.
Of this year's 21 award-winning recipients, here we introduce 13 innovations related to the Group's strategic growth areas that will contribute to realizing a sustainable society.
Retrofitting Service for Existing Gas Turbine Power Plants to Enable Hydrogen Mixed Combustion
Mitsubishi Heavy Industries, Ltd., Energy Systems
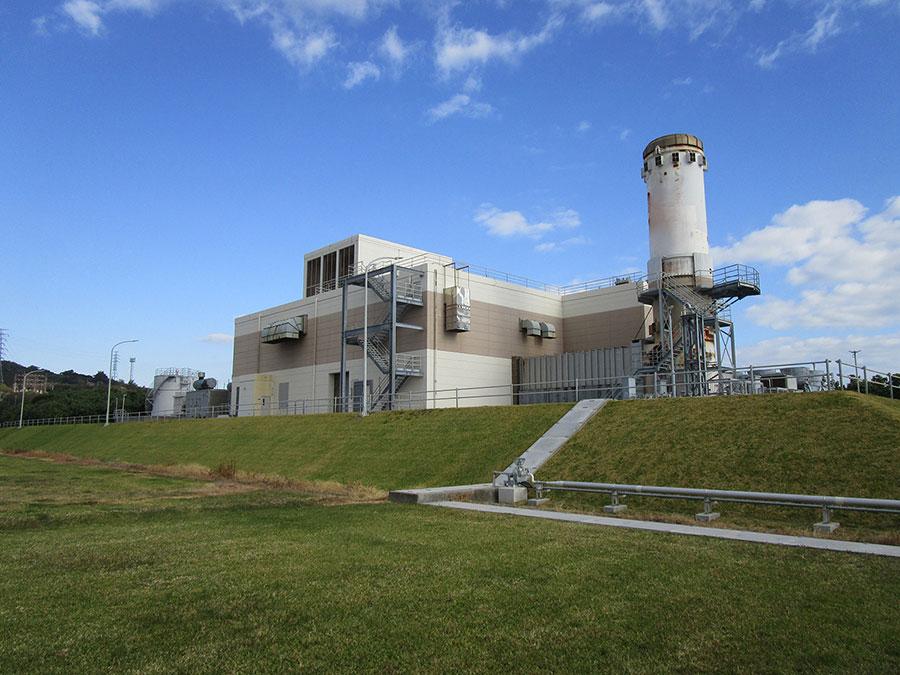
Yoshinoura Multi-Gas Turbine Power Plant,
The Okinawa Electric Power Company,
Incorporated
MHI received an order for modification services to enable hydrogen mixing at an existing gas turbine power generation plant and successfully completed the modification. Specifically, this included installing additional plant equipment and control logic modifications to the gas turbine power generation facility at the Okinawa Electric Power Company's Yoshinoura Multi-Gas Turbine Power Plant that MHI installed in 2015, in order to control the flow of hydrogen while mixing it with fuel gas. The plant was converted to a commercial facility capable of hydrogen co-firing and successfully achieved hydrogen co-firing operations (on a scale of 30% by volume). This achievement will contribute to the expansion of the gas turbine business as a solution for achieving a decarbonized society.
New Large-Capacity Centrifugal Chillers, known as the "JHT-Y/JHT-YI Series," Employing Refrigerants with an Extremely Low Environmental Impact
Mitsubishi Heavy Industries Thermal Systems, Ltd. (MHI Thermal Systems), Chiller & Heat Pump Engineering Department
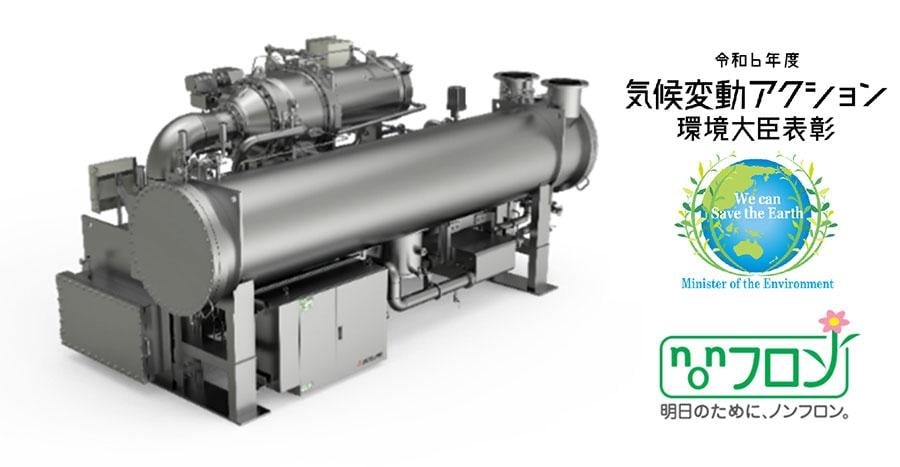
New JHT-Y Centrifugal Chiller with HFO-1234yf
MHI Thermal Systems has developed the world's first centrifugal chiller to adopt a refrigerant for car air-conditioners (HFO-1234yf), which has a global warming potential (GWP) of less than 1, with an extremely low environmental impact, and can be reliably sourced. It is equipped with a highly efficient and compact compressor that is tailored to HFO-1234yf and has secured numerous orders from 2023 onwards. The new chiller is capable of replacing conventional units and features a 99.9% reduction in environmental impact (CO2 equivalent) in case of refrigerant leakage. MHI Thermal Systems plans to further expand the market for this product in the future, as it has the capacity to meet the performance requirements (2,500-3,000 tons of refrigeration) of large-scale data centers in North America and Southeast Asia, where rapid growth in demand for electricity is expected. The company received the Minister of the Environment Awards for Climate Action 2024.
Successful Launch of the Second H3 Launch Vehicle
Mitsubishi Heavy Industries, Ltd., Integrated Defense & Space Systems
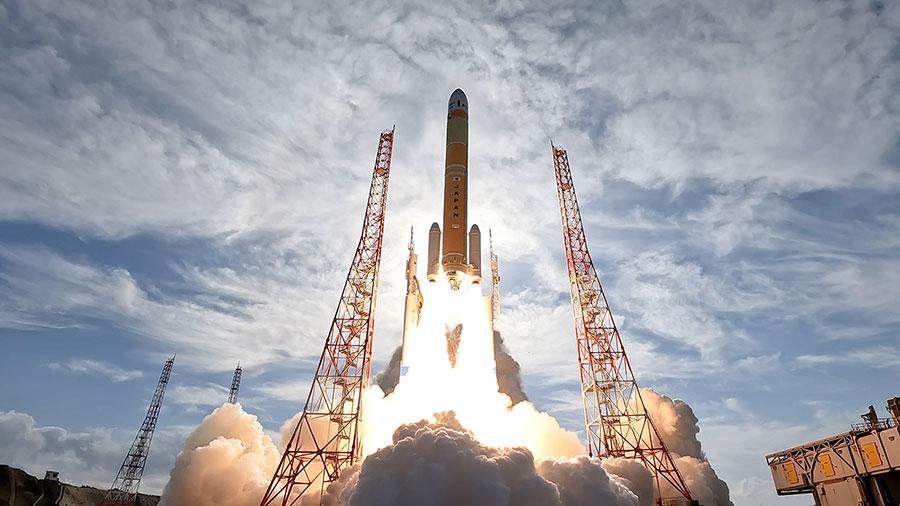
Launch of the Second H3 Rocket Test Vehicle (©JAXA)
As Japan's new flagship rocket, the second H3 launch vehicle was successfully launched in February 2024, followed by successful launches of the third and fourth test flights in July and November, respectively.
The H3 launch vehicle has been under development by the Japan Aerospace Exploration Agency (JAXA) since 2014, and although the launch of the first test flight failed in 2023, the cause of this failure was identified, leading to the successful launch of the second flight. While continuing to make incremental improvements to achieve the initial goal of a flexible and highly reliable, as well as low-cost launch vehicle, MHI will continue to consistently launch satellites and space vehicles at a frequency of six or more per year to contribute to the construction of social infrastructure in space such as weather, communications and security satellites, alongside promoting space utilization and exploration.
Initiatives to Reduce Factory CO2 Emissions by Replacing Existing Factory Boilers with "Q-ton Circulation, MSV" Air-Source Heat Pumps
Mitsubishi Heavy Industries Thermal Systems, Ltd., Production Department
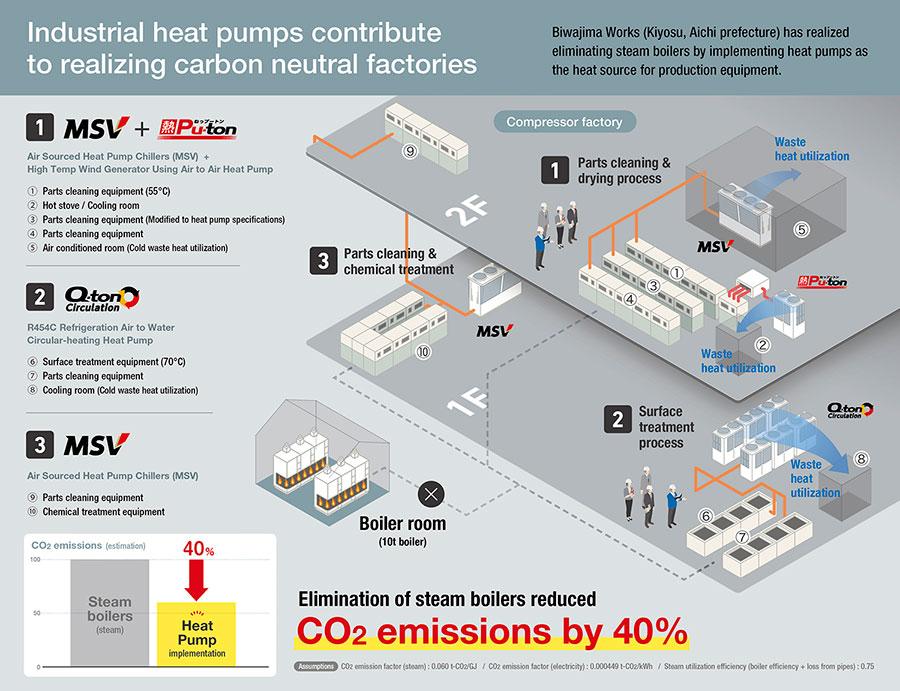
Efforts to Reduce Factory CO2 Emissions Using
Heat Pumps
MHI Thermal Systems implemented efforts to reduce CO2 emissions at an existing plant by converting its heat source from a steam boiler to a heat pump manufactured by our company. Specifically, by measuring the amount of heat required and changing the processing chemicals, at initiative target plant, MHI Thermal Systems was able to completely eliminate the need for boilers in the production process after seven years since the start of this initiative and reduce CO2 emissions by approximately 40%. Since our heat pumps are air-sourced, they can replace steam boilers simply by installing a power supply and hot water piping, and so MHI Thermal Systems are currently in the process of expanding the use of these heat pumps to other plants with parts washing and heat treatment facilities that operate at temperatures of 80℃ or lower. This initiative has received external recognition, including the Energy Conservation Center Chairman's Award in the Energy Conservation Case Study Category of the 2023 Energy Conservation Grand Prize, and MHI Thermal Systems expects to receive increased orders in the future.
The World's First Ammonia and Fertilizer Production Plant Capable of Capturing and Effectively Utilizing CO2 in Exhaust Gas with the New "KS-21™" Amine Solvent Solution.
Mitsubishi Heavy Industries, Ltd., GX Solutions
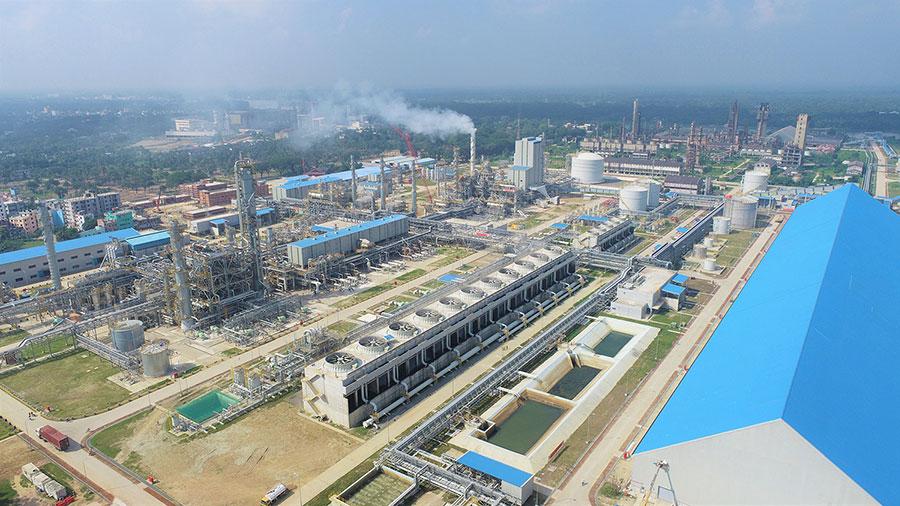
Panoramic View of the Ammonia/
Fertilizer Production Plant
This solution/product is capable of capturing CO2 from the exhaust gas emitted by the primary reforming of natural gas at an ammonia/fertilizer plant and utilizing the captured CO2 in the production of fertilizer. The plant, which MHI supplied to Bangladesh, began commercial operation in March 2024 as the largest ammonia/fertilizer production plant in the country. Using the new KS-21™ amine solvent, the company was able to capture 240 tons/day of CO2 from combustion exhaust gases that had previously been released into the air, thereby increasing their fertilizer production by 10%. This achievement has been reported both in Japan and overseas and is expected to contribute significantly to achieving a carbon neutral society and alleviating food shortages in Bangladesh.
Contributing to Recycling-based Society by Introducing High-Efficiency Biomass Power Plants, as Large-Capacity Renewable Energy Power Source
Mitsubishi Heavy Industries, Ltd., Energy Systems
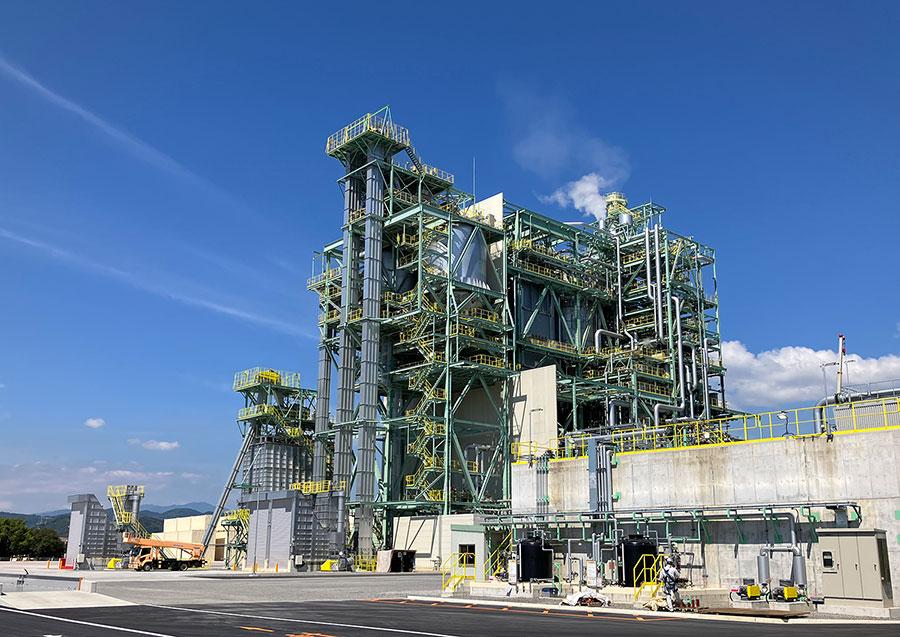
Hyuga Biomass Power Plant
The projects demonstrate the potential for CO2 emissions reduction by introducing high-efficiency biomass power plants which can serve as large-capacity power source that is unaffected by weather fluctuations despite utilizing renewable energy. The plants which are MHI's first products to apply circulating fluidized bed boilers with reheat system and geared type steam turbines, will reduce CO2 emissions by approximately 300,000 tons per year per unit compared to 50 MW-class coal power plants. Moreover, by adopting standardized designs and other measures, MHI has established organizational systems that enable it to propose products that meet multiple customers' needs simultaneously and has received orders for the projects of six plants (total generating capacity: approx. 320MW), four of which have already started commercial operation as planned. The other two are expected to commence that by April 2025, and once all six plants are operational, we predict reduction of CO2 emissions for at least 2 million tons annually.
Securing Aircraft Maintenance Technicians and Creating Local Jobs Through the Aircraft Mechanic Training Program (MHIRJ Academy)
MHI RJ Aviation Group
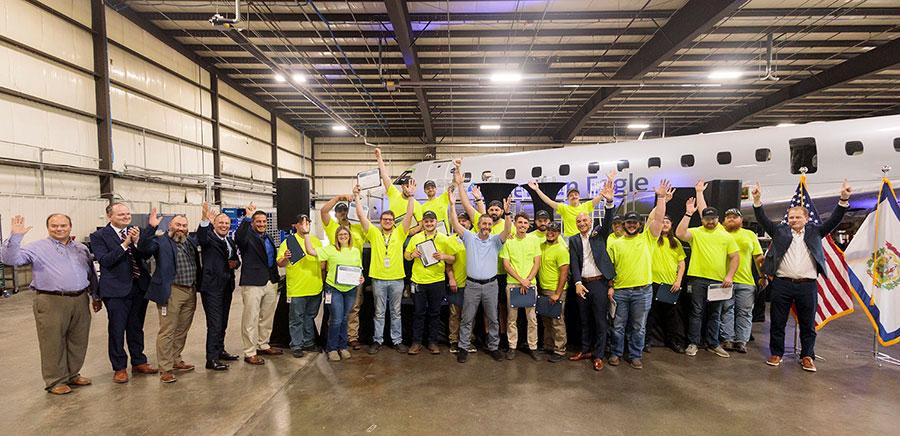
MHIRJ Academy Graduation Ceremony
The MHIRJ Academy is a state supported eight-week program, creating jobs in the community and inviting personnel who did not have exposure to aviation industry. Eliminated barriers to entry for the applicants to pursue a career in aviation while increasing the much-needed aircraft maintenance workforce at the service center. The program is conducted at the MHIRJ maintenance hangar in Bridgeport, West Virginia, US, where experienced MHIRJ mechanics serve as instructors and provide basic aircraft maintenance training. The program is FAA Approved Training that leverages classroom and practical experience to teach the required skills to do sheet-metal repairs. After completion of the Academy, employee will be able to obtain Repairman Certificate. Sixty-four of the 75 participants in this program have already graduated and are now working at MHIRJ as repairman contributing to securing critical resources and MHIRJ is now a participant in generating the next generation of aircraft technicians and contributing to easing the shortage of maintenance technicians in the US that is projected to last over the next decade. MHIRJ Academy plans to produce a total of 100 graduates by May 2025.
Further Advances in Automatic Gas Turbine Combustion Vibration Control Technology (A-CPFM) (Note) by Leveraging AI
Mitsubishi Heavy Industries, Ltd., Research & Innovation Center
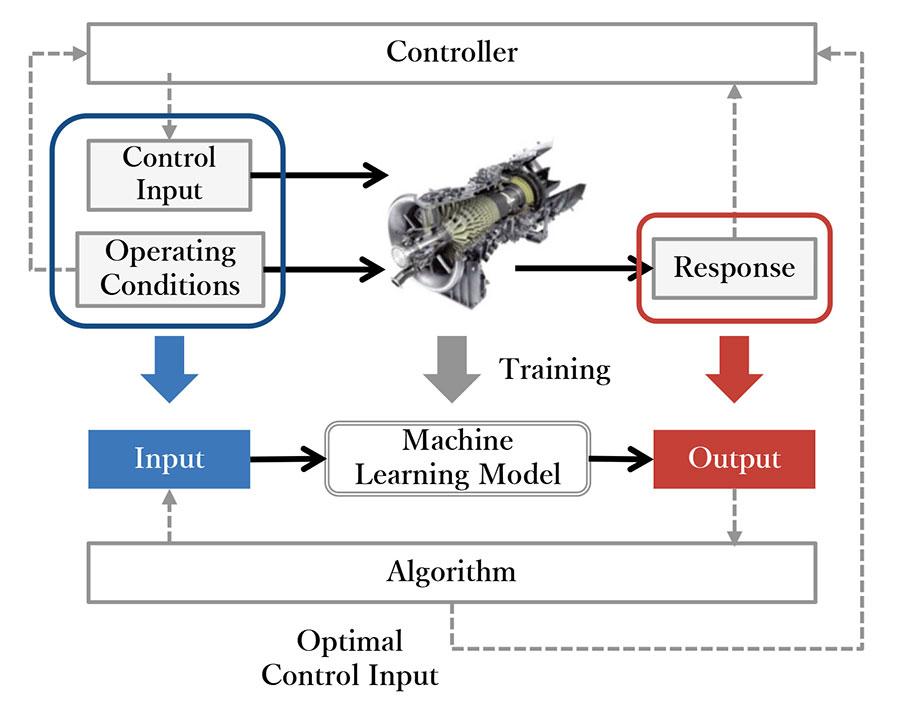
Overview of Automatic Gas Turbine Tuning Utilizing Machine Learning
By incorporating machine learning into the conventional automatic combustion vibration adjustment technology for gas turbines (A-CPFM), MHI has developed a service technology that enables automatic adjustments that take into account the reliability of the predicted results. The system learns combustion vibration characteristics in real time and automatically searches for and adjusts the stable combustion zone based on the uncertainty of the predicted results, enabling the operation of gas turbines with reduced risk. At the same time, MHI has developed the technology to automatically collect operating data for machine learning, which can also take into account changes in operating characteristics over the long-term as the system deteriorates. This new technology has been applied to a gas turbine combined cycle (GTCC) plant at the Jackson Power Plant in the US and successfully achieved zero trips due to combustion vibration. It can also be used to adjust the combustion vibration of new models of combustors, which had previously been difficult to manage, and is expected to gain further market penetration in the future.
- A-CPFM: Advanced Combustion Pressure Fluctuation Monitoring System
The Sole Composite Precision Manufacturing Technology in the World Capable of Producing Key Components for Experimental Fusion Reactor, the ITER
Mitsubishi Heavy Industries, Ltd., Nuclear Energy Systems
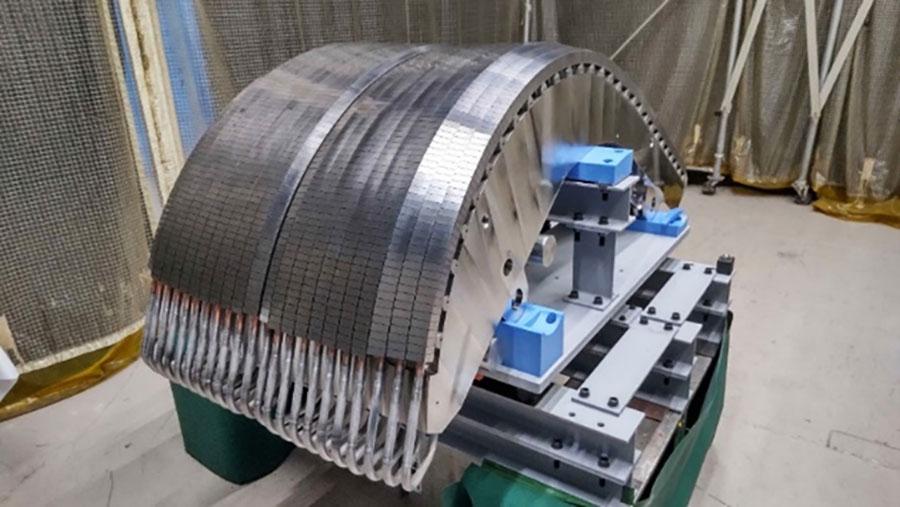
Outer Vertical Target Prototype Appearance
The ITER is an experimental fusion reactor for a highly extensive international cooperative project. The divertor is one of the key components in the ITER tokamak, and especially, the fabrication of the outer vertical target (OVT) requires a complex structure consisting of special materials and high fabrication precision in order to withstand the extreme environment, including high heat flux (up to 20 MW/m²). MHI has succeeded in manufacturing the world's first OVT prototype that meets this high level of technical requirements using the new manufacturing technologies MHI developed, including dissimilar joining technology for brazing tungsten blocks and Cu-alloy tubes (tolerance of ±0.1 mm between blocks), non-destructive inspection technology, and welding and machining technology for materials that prove difficult to weld (such as XM-19 stainless steel), in addition to our proprietary manufacturing technologies accumulated over a long period of time, such as machining with the "Super Miller", a large scale complex machine tool, and "electron beam welding" which does not require welding materials. As a result, these manufacturing technologies are the only ones certified by the National Institutes for Quantum Science and Technology (QST), the Japan domestic agency for ITER, and MHI has received orders for 18 out of the 58 OVTs for ITER, all which are so far ordered by QST. Further contributions to the business are anticipated as orders are expected to be placed in the next fiscal year and beyond.
Composite Risk Management Technology to Reduce the Risk of Unplanned Outages and Stabilize the Operation of Overseas Waste-to-Energy (WTE) Facilities
-- Utilization of the Integrated WTE Plant Operation System "MaiDAS®," etc. --
Mitsubishi Heavy Industries Environmental & Chemical Engineering Co., Ltd. (MHIEC), Overseas Business Operation Division
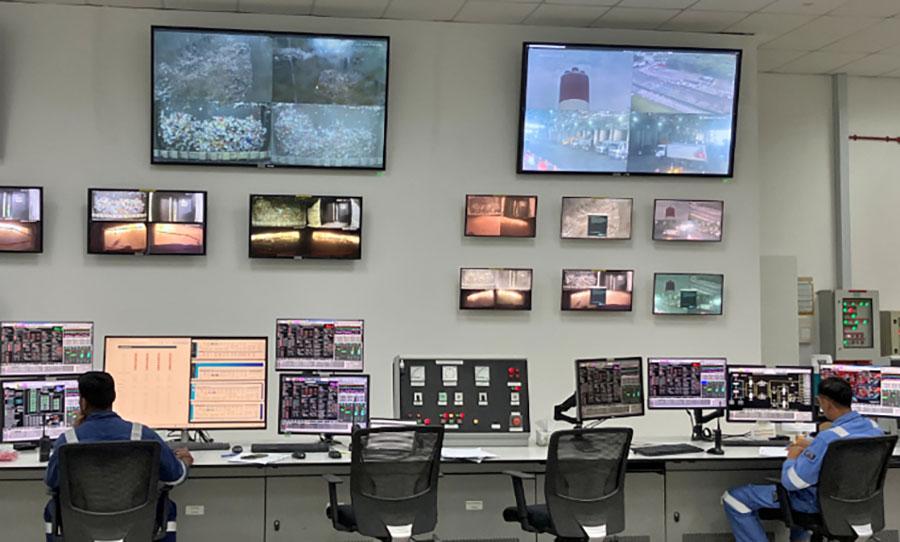
Center Control Room with MaiDAS® application
Operation of Large-scale overseas WTE facilities are sometimes subject to high risk due to external disruptions, such as the incineration of waste with unstable properties and human error by inexperienced operators, so reducing unplanned shutdowns in these facilities is an urgent issue. In response, MHIEC has introduced the integrated WTE plant operation system "MaiDAS®" to support plant operation through monitoring and automatic operation, and in parallel developed a tool to predict when a furnace shutdown for inspection is required based on operational data and reflected the predictions in the annual operation plan and daily operating conditions, thereby ensuring stable plant operation. Furthermore, MHIEC has improved the business feasibility by developing technologies to reduce the consumption amount of chemicals, reducing interest payments on loans, and other creative measures for facility operation. Using this remarkable achievement as a steppingstone, MHIEC will continue to contribute to mitigation of global environmental harm and the protection of the global environment through WTE facilities equipped with "MaiDAS®" in the future.
Next-Generation Cold Rolling Technology to Produce Magnetic Steel for Future Electric Vehicles
Primetals Technologies, Global Business Unit Downstream
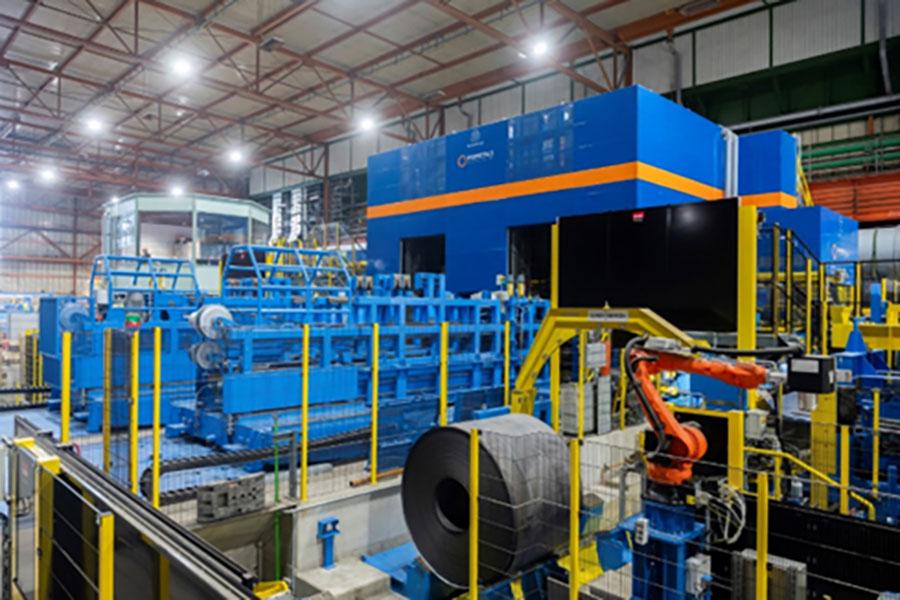
The world's first 2-stand HYPER UC-MILL® reversing cold mill installed at thyssenkrupp Steel in Bochum, Germany
The world's first 2-stand Hyper UC-MILL® is an advanced reversing cold rolling mill equipped with a steel sheet induction heating system, a novel rolling lubricant supply technology MQL®, and a steel sheet temperature control system. This innovative system utilizes a new generation of 6-high cold mill featuring a small work diameter and enables the rolling of strips as thin as 0.2 mm ideal for use in electric vehicle motors. This technology allows the stable production of very brittle high-silicon electrical steel sheets. The first commercial unit has already gone into operations at thyssenkrupp Steel, a German steel manufacturer located in Bochum. The mill was successfully started up in 2023/2024 and manufactures the entire product mix including thin-gauge, high-grade, non-grain oriented electrical steel, for example used for electric vehicles, and advanced high-strength steels (AHSS) addressing the needs of the automotive industry. Thanks to the increasing electrification and popularity of electric vehicles, demand for electrical steel sheets is on the rise. Accordingly, the business is expected to grow.
Development of Ultra High-Speed Blowdown Combustion Test Equipment to Streamline Development for Hydrogen-Fired Gas Turbine Combustors
Mitsubishi Heavy Industries, Ltd., Research & Innovation Center
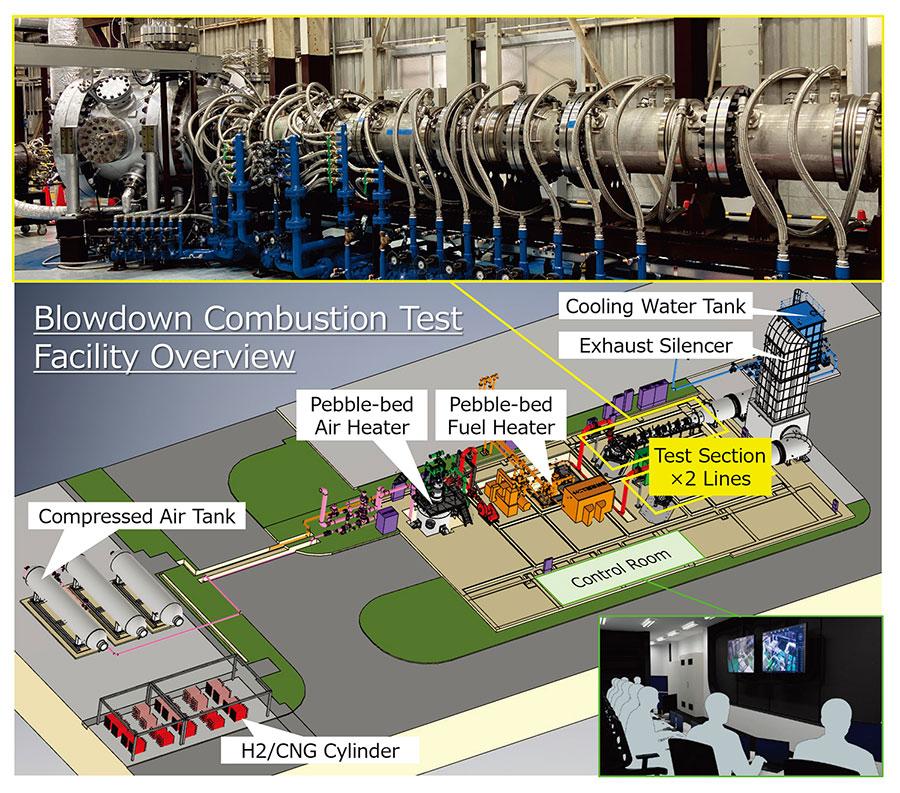
Blowdown Combustion Test Equipment and Illustration of the Overall Facility
MHI has developed an ultra-high-speed blowdown combustion test equipment that dramatically improves the efficiency of actual pressure combustion test for large gas turbines. This has enabled successful operation of the complex, high-speed, and challenging system on the first run, reducing the test time from 6 hours to 3 minutes (1/120th) and the test fuel cost down to 1/24th of the original actual pressure combustion test. The success was attributed to the development and application of technology that, in addition to the design of a large-scale structure, combines an emulator of control logic with dynamic simulation to predict temperature and pressure stabilization to simulate the timing of valves opening and closing and the adequacy of high-speed operational settings. This technology is expected to become a core component of future competitiveness as it can be applied to the development of gas turbine combustors capable of handling a wide range of hydrogen concentrations from hydrogen co-firing to hydrogen firing, as well as to the control design of any large-scale machinery group or plant.
Awarded the "DX Grand Prix" for the First Time as a Company Leading the Digital Age
Mitsubishi Heavy Industries, Ltd., Digital Innovation Headquarters
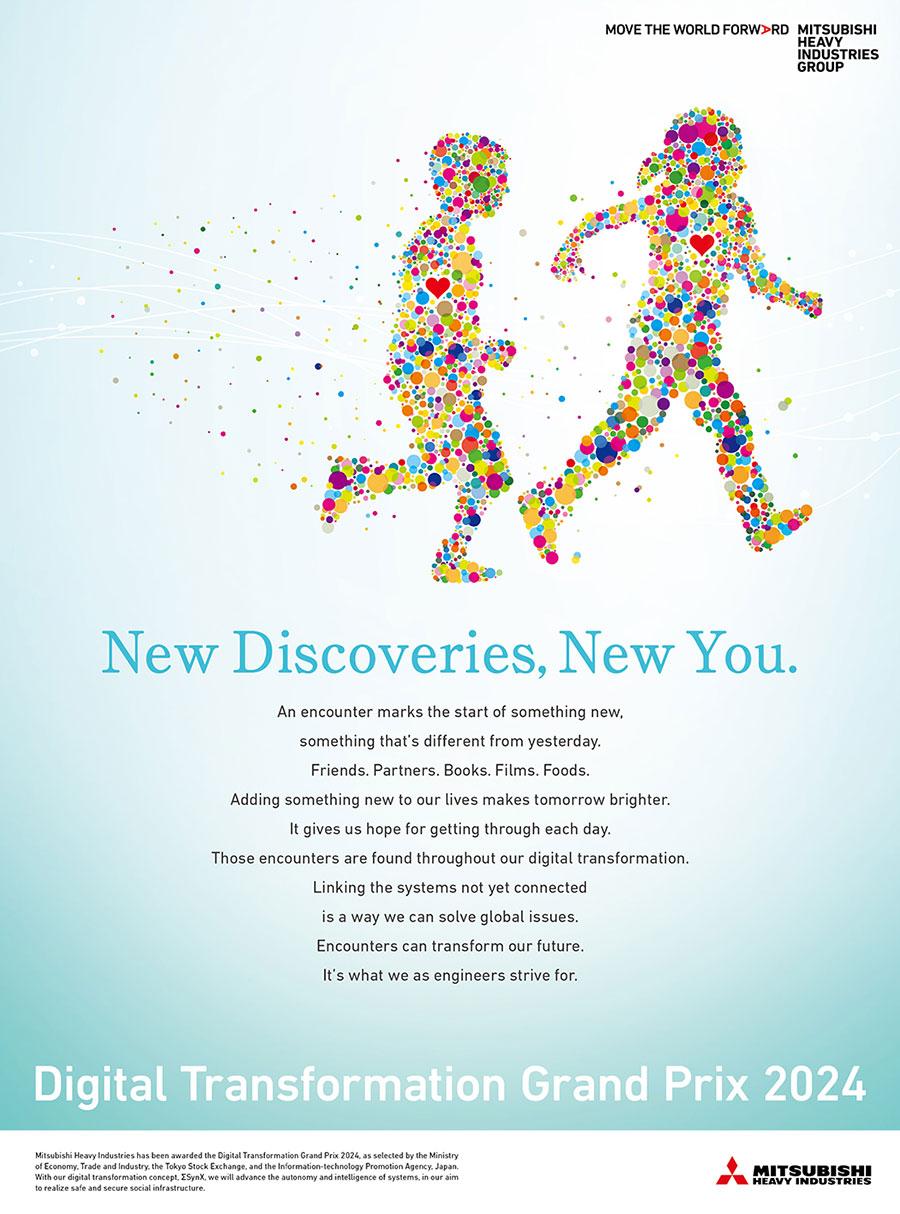
DX Grand Prix Award Winning Ad
In the "Digital Transformation (DX) Stocks 2024" hosted by Japan's Ministry of Economy, Trade and Industry, the Tokyo Stock Exchange, and the Information-technology Promotion Agency, Japan (IPA), MHI was awarded the Grand Prix and selected as a leading company in digital transformation. The development and social implementation of the solution concept "ΣSynX (Sigma Syncs)" for automating and intelligentizing our entire Group's products, which we have been working on, have progressed in various areas. Our specific DX initiatives aimed at achieving carbon neutrality have been appreciated by stakeholders.
About MHI Group
Mitsubishi Heavy Industries (MHI) Group is one of the world’s leading industrial groups, spanning energy, smart infrastructure, industrial machinery, aerospace and defense. MHI Group combines cutting-edge technology with deep experience to deliver innovative, integrated solutions that help to realize a carbon neutral world, improve the quality of life and ensure a safer world. For more information, please visit www.mhi.com or follow our insights and stories on spectra.mhi.com.