EX ROVR "ASCENT", the autonomous, explosion-proof, plant inspection robot : Products
Distributors :
Products
EX ROVR, the autonomous, explosion-proof, plant inspection robot
- Fully autonomous operations across multiple floors with advanced stair climbing and obstacle avoidance functionality
- Acquisition of asset data through visual imaging, thermal scans, acoustic mapping, and gas concentrations with its suite of advanced sensors
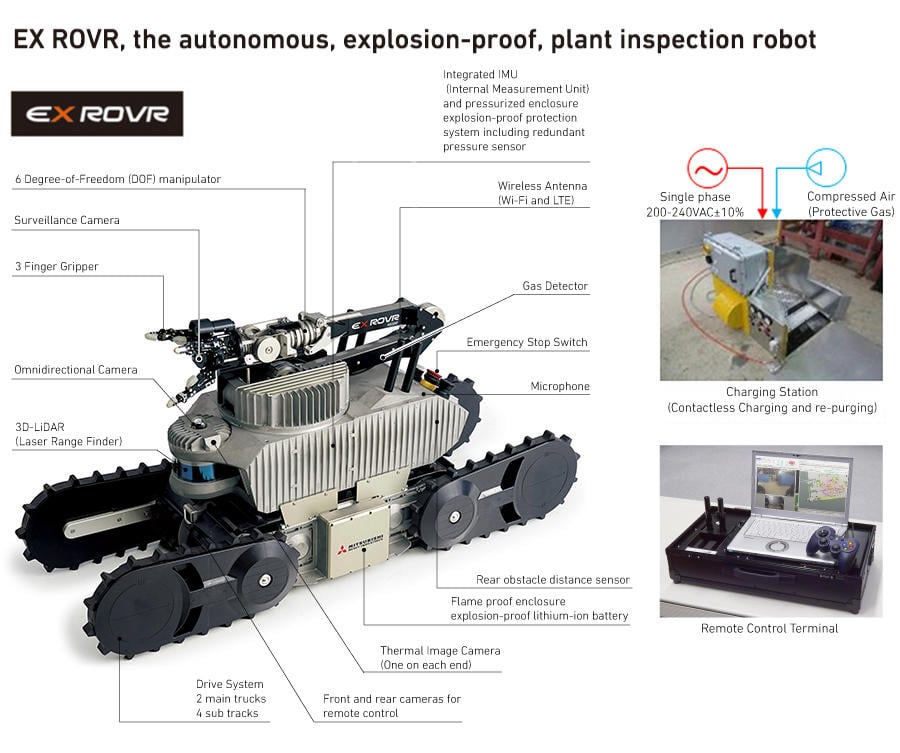
EX ROVR “ASCENT” Hardware outline
- ATEX and IECEx Zone 1 explosion-proof certified featuring a large capacity, explosion-proof lithium ion battery and contactless charging in the hazardous location
- Fully autonomous operations across multiple floors with advanced stair climbing functionality up to 46 degrees in pitch both up and down
- Surveillance camera with 6 DOF manipulator for capturing images in optimized position to targets
- Acquisition of asset data through visual imaging, thermal scans, acoustic mapping, and gas concentrations with its suite of advanced sensors
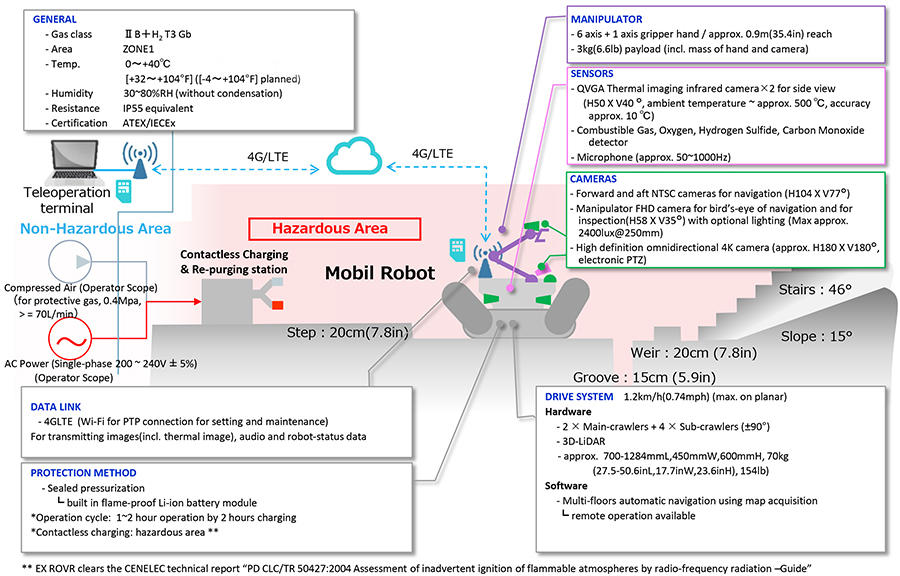
Explosion Proof
Complies with regulations in various countries, IECEx, ATEX, Ex2018
- Gas Class: II B + H2 T3 Gb
- Area: Zone1
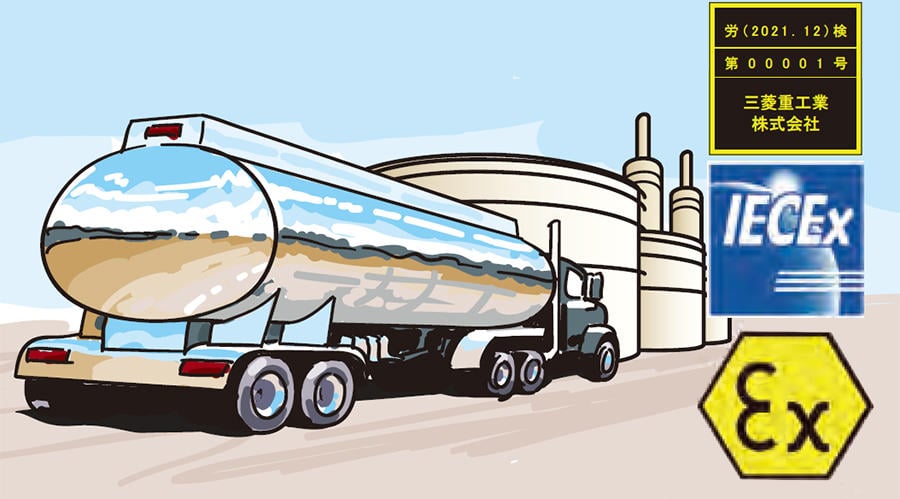
Explosion-proof standard | IECEx | ATEX | Japan (Ex2020(2018)) |
---|---|---|---|
Explosion-proof rating | Ex db ib pxb IIB+H2 T3 Gb | II 2G Ex db ib pxb IIB+H2 T3 Gb | Ex db pxb IIB+H2 T3 Gb |
Type approval certification number | IECEx TIIS 22.0002X | SCA 22 ATEX 140X | No. TC22783X |
ASCENT consists of a single internally pressurized explosion-proof enclosure for the main body, and includes main and sub tracks for movement and motor for the manipulator.
The built-in battery that powers the various components is housed in an explosion-proof case together with a lithium-ion battery control unit. ASCENT is equipped with LED lighting, gas detector, optical surveillance camera, microphone and speaker with independent explosion-proof specifications.
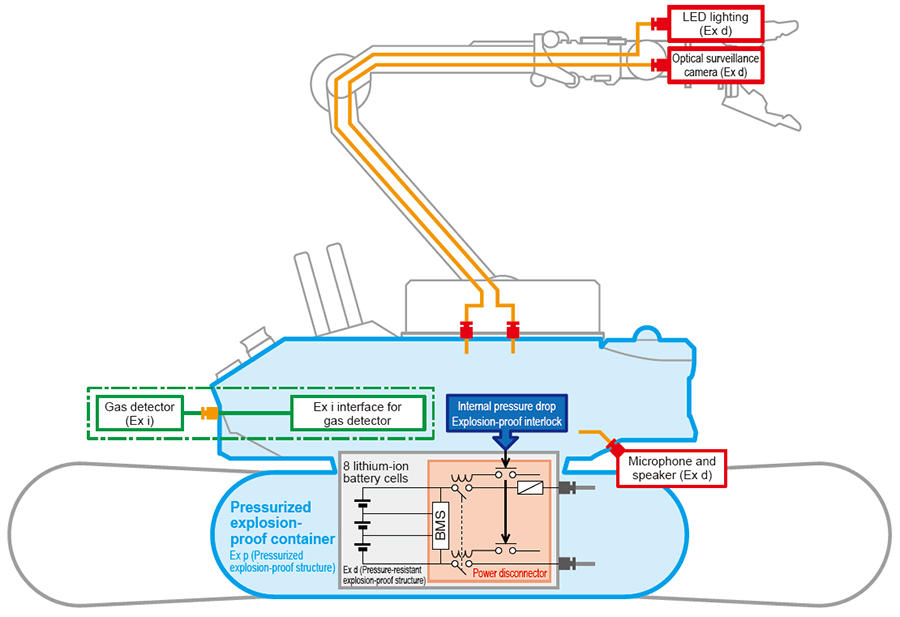
Autonomous Navigation
Performance of autonomous operator rounds even in the complicated environments and low light conditions
- Localization through advanced 3D LiDAR maps
- Fully autonomous obstacle recognition
- Fully autonomous stair climbing ability
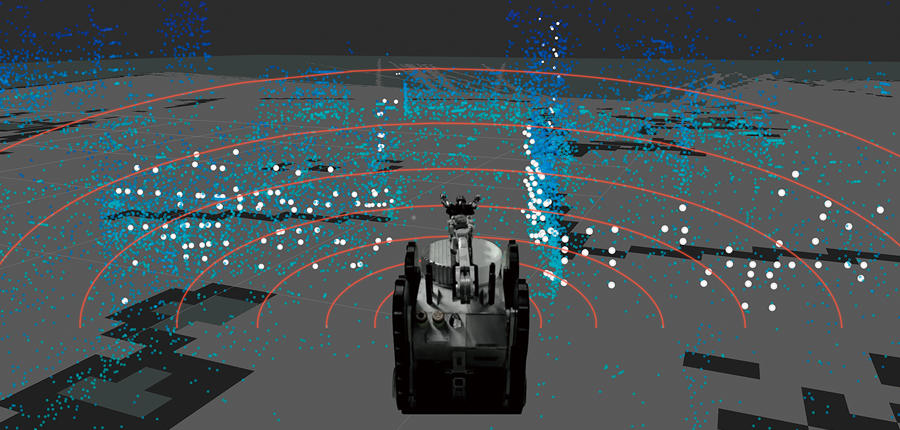
EX ROVR “ASCENT” Setup outline
Robot setup and control for mapping, routing, and autonomous traveling inspection are remotely implemented.
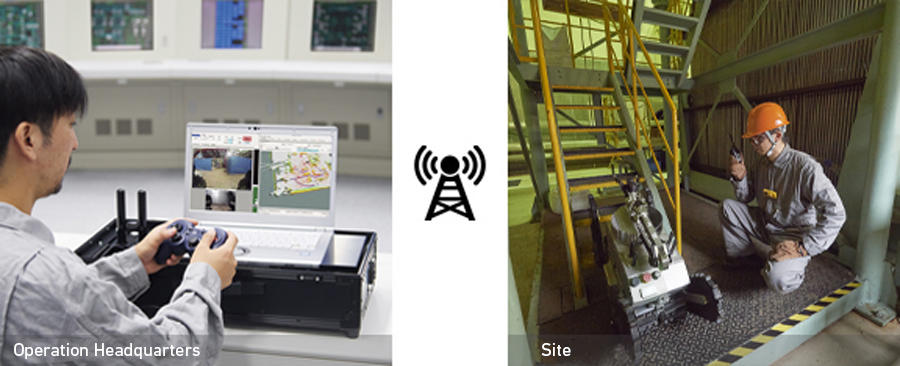
- Step 1
- Setting remote operator station, robot, and charging station
- Step 2
- Target area mapping by 3D-LiDAR through remote controlled EX ROVR
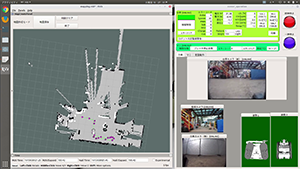
- Step 3
- Routing & inspection scenario setting through remote controlled EX ROVR
- Step 4
- Setting EX ROVR deployed inspection schedule and scenario

- Step 5
- Implementing autonomous traveling inspection
・Set inspection scenario implemented automatically according to the set schedule
・Plant field information and images gathered and stored
・Manual remote operation available as necessary by changing from autonomous

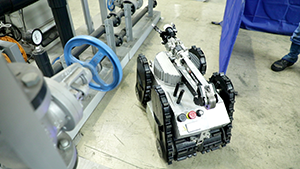
High Mobility
Able to negotiate narrow paths across multiple floors in a complex environment
- Can ascend and descend 46 degree staircases
- Can turn “on a dime” on a narrow staircase landing
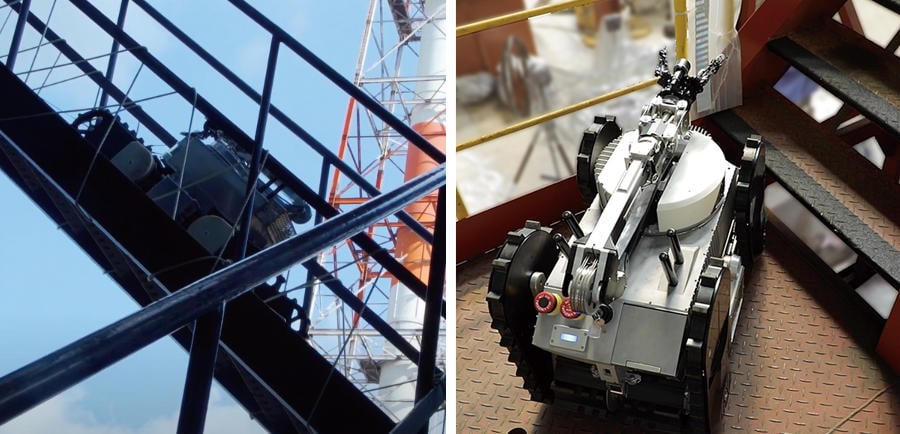
Driving performance of ASCENT
During autonomous patrol | During teleoperation | ||
---|---|---|---|
Slope | Depends on the nature of the obliquity (such as the coefficient of friction) | ||
Slope | See A. | Inclination of 46° or less | |
Bank | Water runoff slope or less (slope 1/50 to 1/100, or 0.57° to 1.15° in angular terms) | Slope for running without tipping over is 20° or less. | |
Stairs | Step height: 130 to 220mm Step depth: 210 to 310mm Step width: 900mm or greater For slope, see B. |
Step height: 130 to 220mm Step depth: 210 to 310mm Step width: 900mm or greater Inclination of 46° or less |
|
Landing | Capable of navigating landings of the following shapes and dimensions. U-shaped: Minimum dimensions of 1800mm (W) x 1000mm (D) L-shaped: Minimum dimensions of 1000mm (W) x 1000mm (D) I-shaped: Minimum dimensions of 900mm (W) x 900mm (D) |
||
Difference in level | Height: 20cm or less (must have a rectangular cross section) | Height: 40cm or less (depending on form) | |
Ditches | Width: Within 15cm | Width: Within 30cm (depending on form) |
A: Slope that can be navigated during automatic patrol
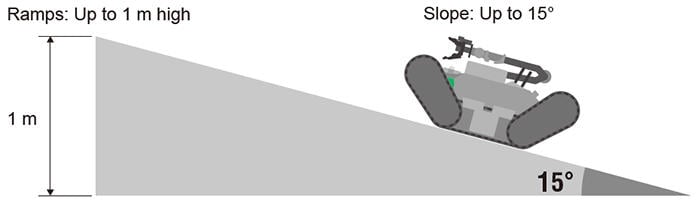
B: Inclination of stairway that can be navigated during automatic patrol
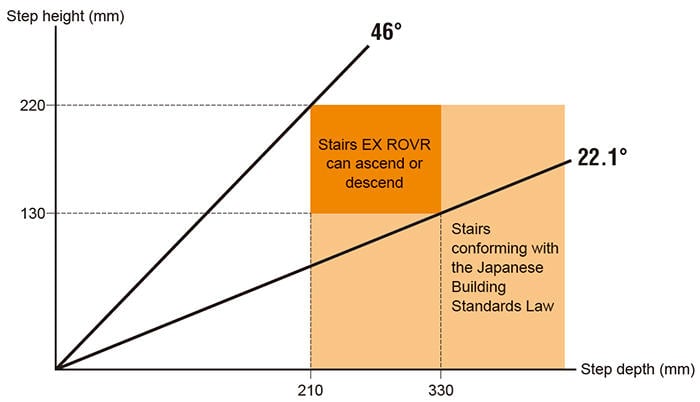
Driving route conditions
ASCENT cannot travel through aisles that are narrower than its own external dimensions. Allow enough space around ASCENT for a person to stand (approx. 900mm).
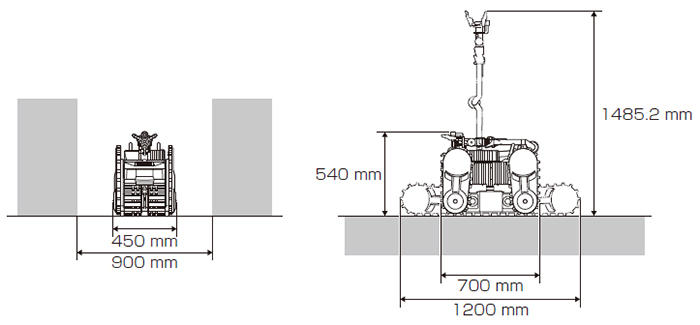
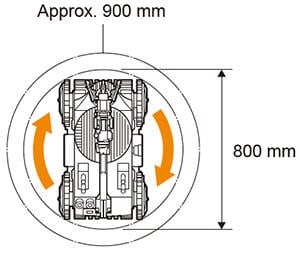
When turning in an aisle, available area must exceed the total length of ASCENT. Allow approximately 900 mm of space as shown in the figure at right.
Manipulator
Capable of complex articulation to position camera and end effector close to the target
- 6 degree of freedom
- End effector with 3 finger gripper for positive contact
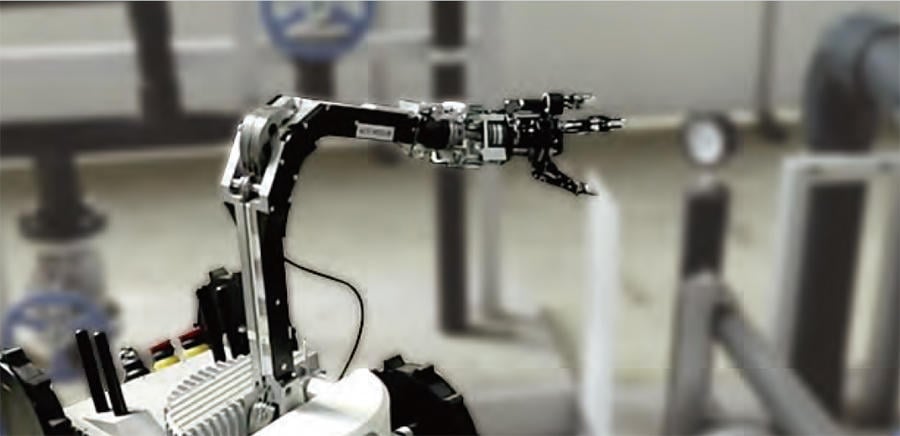
Drive system | Electric servo drive by AC servo motor |
---|---|
Degrees of freedom of movement | 6 axes (excluding hand axis) |
Axis configuration | Axes of rotation: 3 axes Pivot axes: 3 axes |
Range of movement | Reach: Approx. spherical R 1m semi-dome |
Max. velocity (horizontal and vertical from reference position in reference attitude(note)) | Approx. 100mm/sec. |
Carrying capacity (force generated in reference attitude(note)) | Approx. 3kg (including hand) |
Operation control | Control of each axis and position/attitude control |
Response to anomalies | Error processing |
Rated output of drive motor | 50W |
- The reference attitude is shown in the figure below.
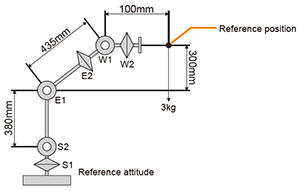
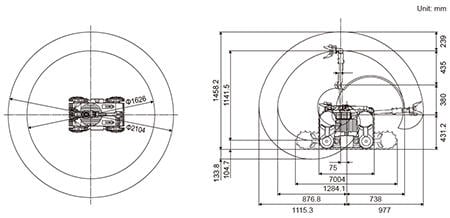
Autonomous Charging
Capable of long run times and quick charging
- Contactless induction charger is explosion proof and can be placed in the hazardous location
- Rapid charging allows for high availability with 2 hours of operation by 2 hours of charging
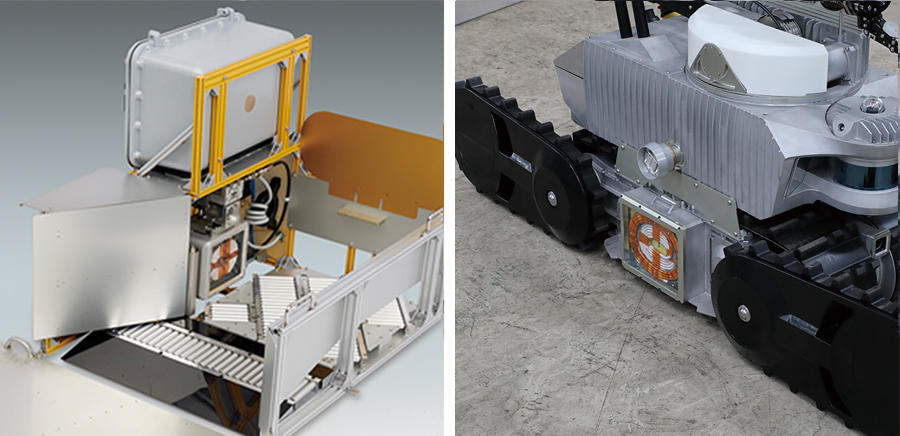
Main Dimensions (mm)
Unit Weight: 70 kg (excluding charging station)
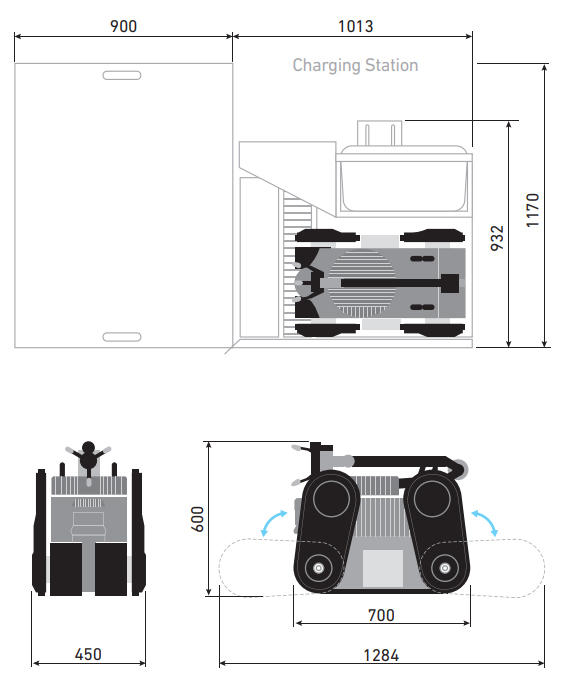
Data Management
Mission planning and data validation can be performed remotely from anywhere in the world
- Mission planning inspection waypoints can be set through secure connection via internet browser
- Inspection data is securely stored in the cloud and can be accessed on demand
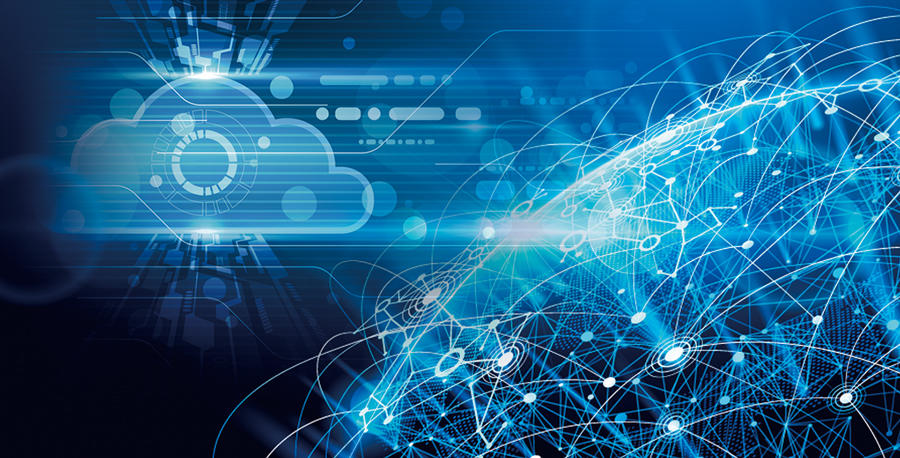
- Robot controlling and supervising via 4G/LTE network
- Robot gathered plant information storage and management on Cloud
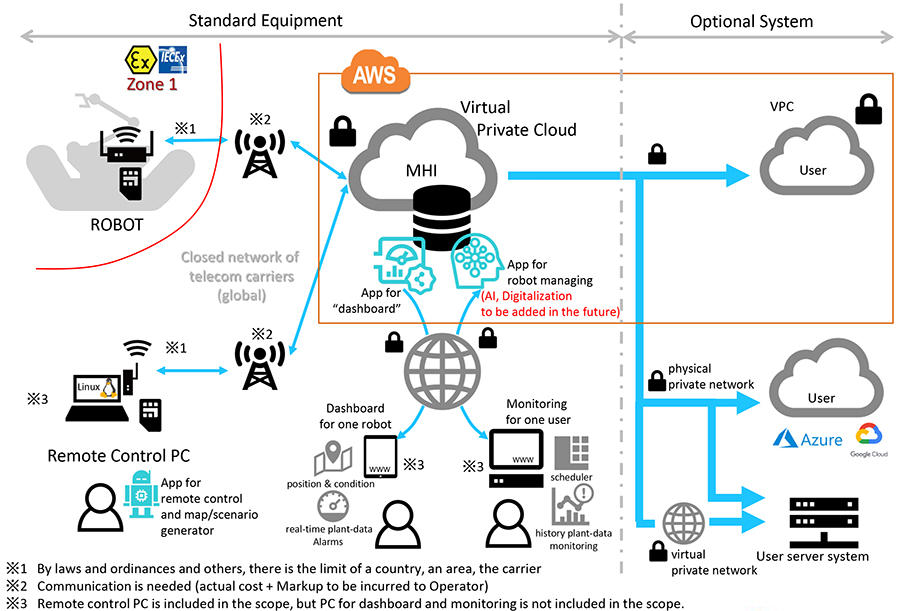
Business Contact
Please send to the inquiry form below or your email address.
