FUSION ENERGY : Efforts for ITER
Distributors :
On Fusion Energy
About the ITER Project
The ITER project had been initiated in accordance with the USA-Soviet Summit (Reagan-Gorbachev) Joint Declaration of 1986 to build an international thermonuclear experimental reactor. In 1989, the ITER conceptual design activities (CDA) started with the following participants: USA, former Soviet Union (Russia), Europe, and Japan. This initial effort led to the engineering design activities (EDA) starting in 1992 and continued for nearly 9 years as there was a significant focus on the detail design, manufacturing verification testing, and additional technology development to support the goals of ITER. In 2005, its construction site was chosen at Saint-Paul-lès-Durance as where is adjacent to the Cadarache Research Center of CEA (the Alternative Energies and Atomic Energy Commission) in France. Pursuant to the ITER Agreement signed by all countries on November 21, 2006, an ITER Organization was to be established as an international legal entity, which was realized on October 24, 2007. Through agreement, an in-kind contribution system was adopted and at present manufacturing of equipment/facilities are underway by the following participants: Japan, Europe, USA, Russia, China, Korea, and India.
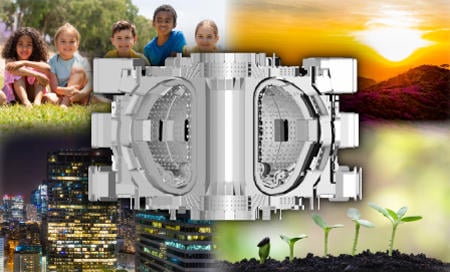
Components and Equipment procured by Japan
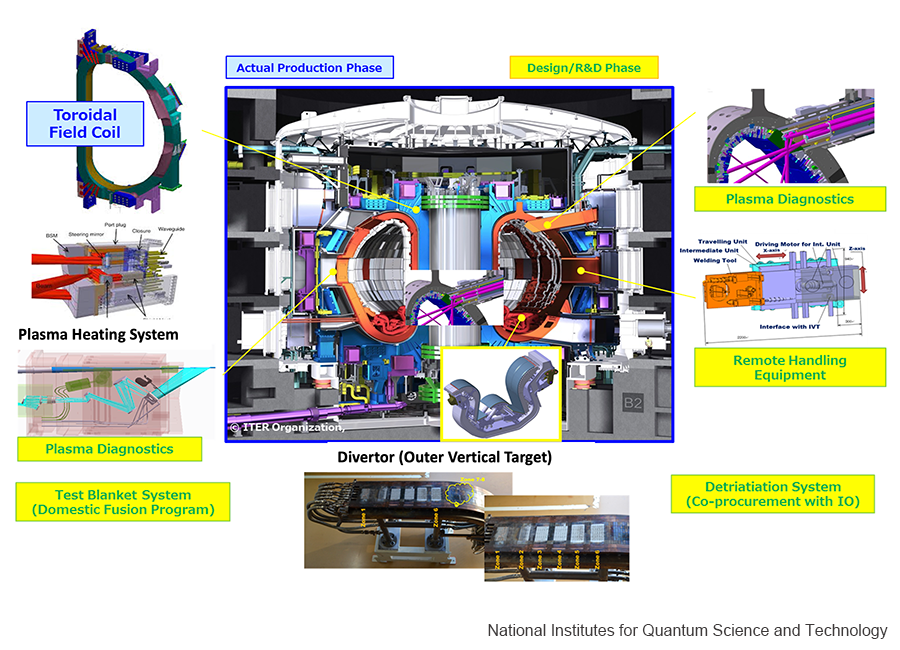
Related Links
Toroidal Field Coil
MHI’s Efforts for Toroidal Field Coil
Toroidal Field (TF) Coils are used by Tokamak type fusion systems to generate strong magnetic fields to stably confine the plasma with high densities and high temperatures. The reactor of ITER have eighteen TF Coils which positioned around the vacuum vessel to form plasma in the vessel. Each TF Coil for the ITER is 16.5m tall, 9m wide, and weight nearly 300 metric tons which is the largest niobium-tin (Nb3Sn) superconducting magnets in the world.
Gravity of TF coil alone
-
- Height
- 16.5m
-
- Width
- 9m
-
- Weight
- 300metric ton.
To ensure the stable confinement of plasma the ITER, a strict dimensional accuracy is required to manufacturing each of the TF Coils. One example of the requirements is the fit-up of the Inboard (AU) and Outboard (BU) which have several meters and metric tons to form TF Coils structures. The requirement is that the gap between them shall be controlled three-dimensionally within 0.5mm +/-0.25mm which is equivalent to the thickness of a sheet of paper. This requirement has been achieved through a series of manufacturing tests using scaled mockups and full scale mockups to establish the manufacturing processes specially designed for the TF Coils.
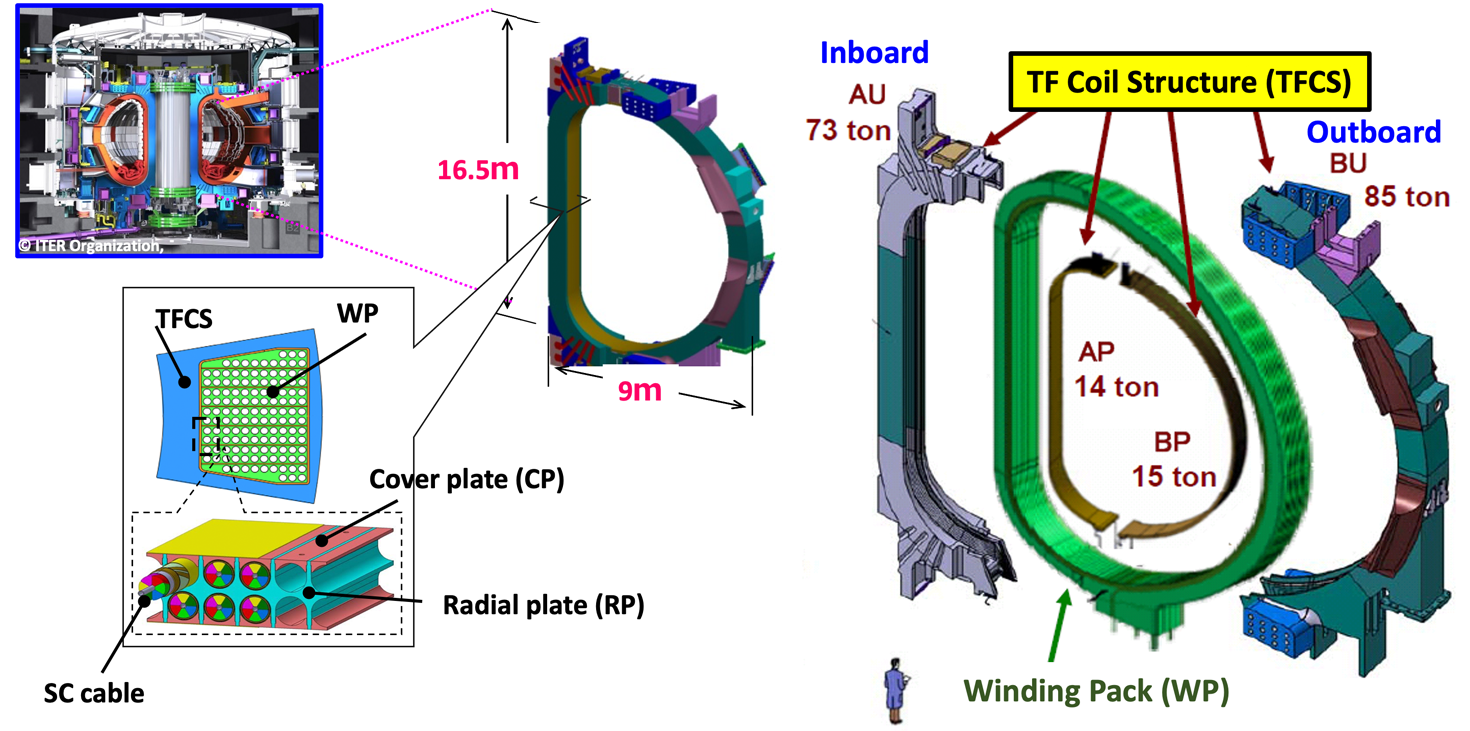
MHI’s Development of Human Resources and Expansion of Technology
MHI’s engineers have been engaged in the challenge of developing suitable manufacturable solutions to achieve ITER’s arduous requirements. Through their creative ingenuity and resilience as chosen outstanding engineers, they have achieved all of the ITER’s requirements by their manufacturing technologies applied for welding of TF Coil Structures, including.
- Welding with no installed restraints
- Adoption of narrow-gap TIG welding and electron-beam welding processes to minimize weld deformation
- Continuous optimization of welding procedures through our robust development program
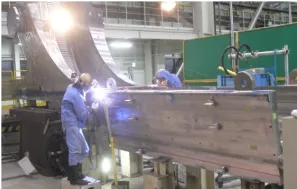
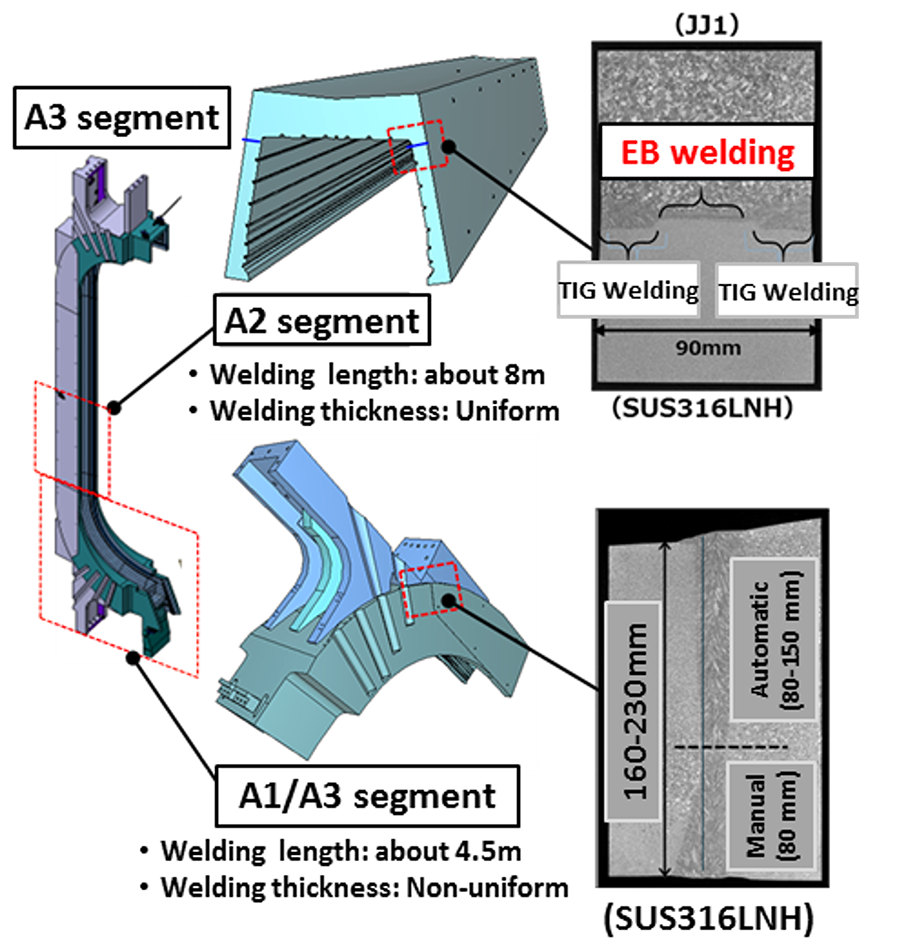
Welding and Machining of Radial Plate
To achieve the ITER’s requirements, MHI’s manufacturing technologies applied for welding and machining of the Radial Plates, including.
- Welding with no installed restraints
- Adoption of narrow-gap TIG welding and laser-beam welding processes to minimize weld deformation
- Application of fiber laser with intensity of 30kW
- Optimization of process conditions and procedures through our robust develop program to minimize deformation
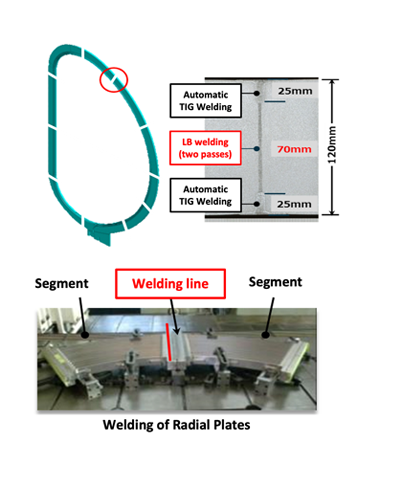
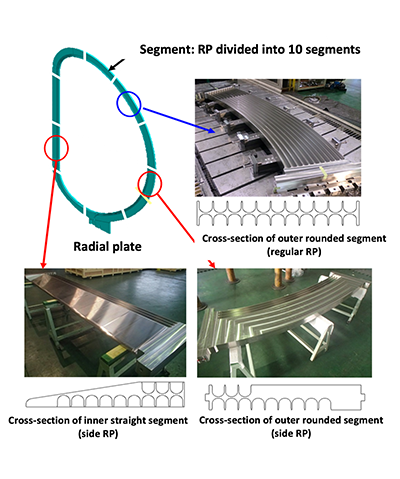
Assessment of Welding Deformation with Use of Numerical Analysis (FEM: Finite Element Method)
Based on experimental data obtained from our mockup testing, a lot of welding deformation analyses have been performed to verify our manufacturing processes. These analyzing efforts contributed to develop welding procedures for minimizing deformations. Applications of these welding procedures achieved the results to meet the challenging target deformation values of the ITER requirements.
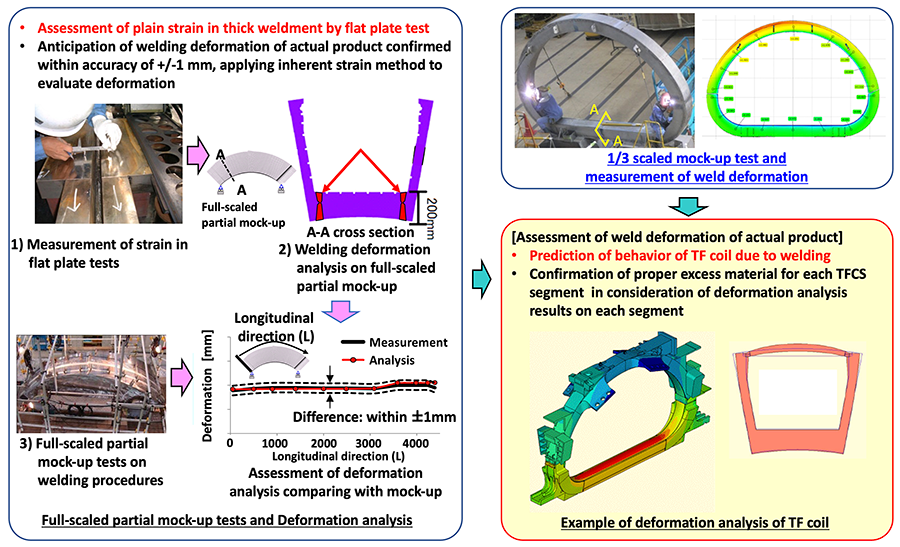
Press Release
- MHI Awarded Contract for Six Units of the Outer Vertical Target for the Divertor Used in the ITER in Southern France
-- Reputation of Leading Edge Mass Production Technology for High Difficulty Component, Contributing to the Realization of Fusion Energy -- - MHI Completes Four TF Coils for ITER
-- Units to Be Installed in the Experimental Fusion Reactor in Southern France, with Operations to Commence in 2025 -- - Ceremony Held to Mark Completion of First Toroidal Field Coil for ITER (Experimental Fusion Reactor)
-- World's Largest Superconducting Coil Signifies Major Progress in Fusion Reactor's Construction --
Divertor
Efforts to ITER Divertor
One of the key components necessary to maintain stable plasma confinement is the Divertor. This component is used to extract and remove nuclides including impurities spring outed from the in-vessel components, fused product, and un-fused fuels.
MHI is participating in the R&D of the outer vertical target (OVT) which forms part of the Divertor assembly. Full-scale Tungsten plasma facing unit (W PFU) test module was manufactured by MHI and qualified by the ITER organization. And a second full-scale W PFU test module and prototype of the OVT is ongoing to validate manufacturing processes and procedures.

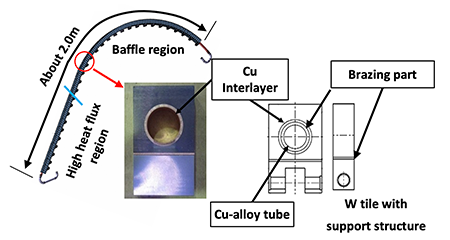
Plasma Facing Unit(PFU)
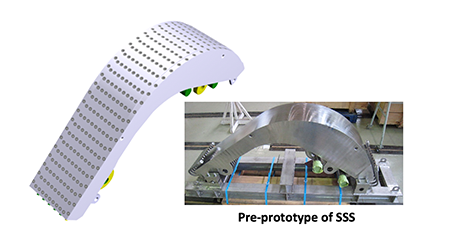
Steel Support Structure (SSS) for PFU
Development of High Heat Flux Components
Peak heat flux conditions onto the divertor straight target is around 10MW/m2 at nominal plasma operating conditions and up to 20MW/m2 as maximum heat flux expected during postulated transients, which are comparable with surface heat flux of spaceships bearing during reentry the atmosphere.
Divertor heat load
-
- Peak heat flux
- 10MW/m2
-
- Heat flux
- 20MW/m2
High heat flux tests
(HHF tests are conducted at the Efremov Institute in Russia)
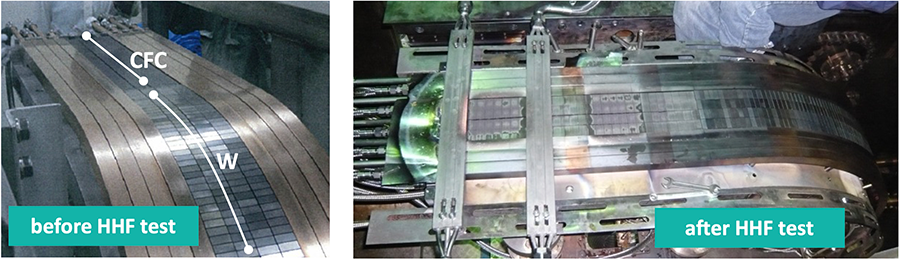
The CFC part which is detachment local brazing joint in W PFU had no damage after high heat flus (HHF) tests of 10MW/m2 x 1000 cycles and 20MW/m2 x 500 cycles.
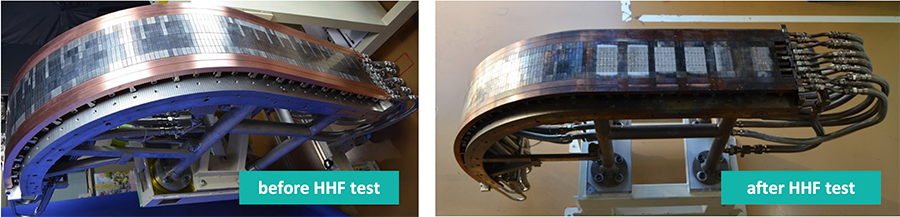
The joints in W PFU was confirmed their Integrity to satisfy the ITER requirements with no damage at 10MW/m2 x 5000 cycles and 20MW/m2 x 1000 cycles by three form back manufactured by MHI. It was a first time achievement in the world.
Welding of Dissimilar Materials (Welding of Cu-alloy to Stainless Steel)
The Cu-alloy tubes have been utilized with high thermal conductivity and high strength for the ITER divertor target parts. The steel support structure (SSS) attached the targets are fabricated from materials called XM-19 which is a kind of stainless steels and cooled by cooling water supplied its inside. The fabrication of the targets shall be required dissimilar weld joint processes to joint Cu-alloy tubes and stainless steel tubes by applicating our accumulated manufacturing experiences in nuclear power plant constructions.
Non-Destructive Inspection Applied to Brazing Joints (Boundary Surface of W-Cu-XM19 and Cu-Cu-alloy)
Ultrasonic non-destructive inspection techniques shall be required to verify the integrity of dissimilar metal brazing joints of W-Cu-XM19 and Cu-Cu-alloy by analyzing propagation properties of ultrasonic waves between material boundary surfaces with understanding their materials characteristics.