Corrugating Machine
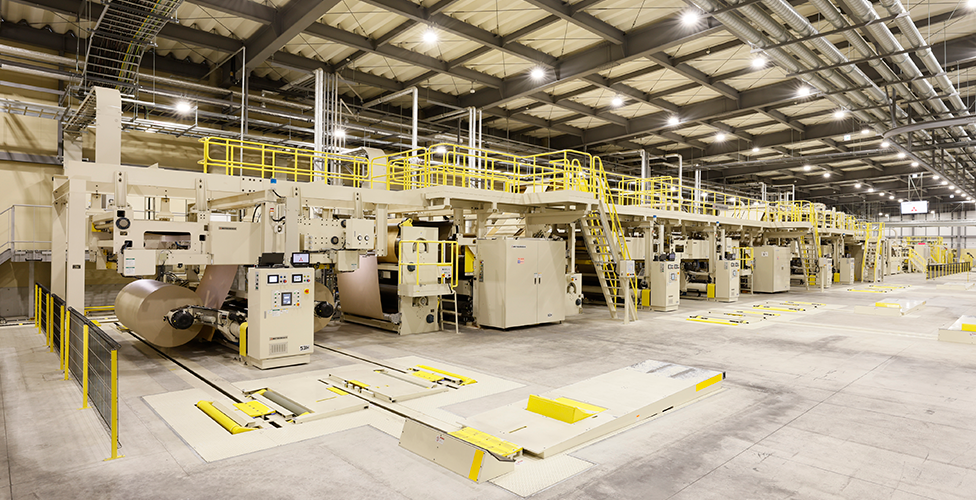
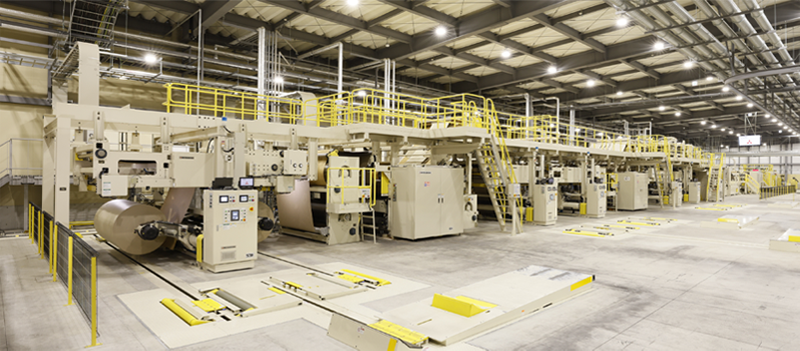
Distributors :
Realizing high quality and stable productivity required in the world.
Contributing to stabilizing quality of corrugated boards and increasing revenue.
Mitsubishi offers high-speed "STEADY STATER" concept corrugating machines, SH-400 series that boast the world's fastest speed of 400 meters per minute, as well as diverse lineups, including H series corrugating machines, which can realize optimum productions based on customers' needs. We will propose the best suitable machine according to customers' requirements such as labor saving, less maintenance, and environmental friendliness.
General Specifications
Model | SH-400 | H-350 |
---|---|---|
Maximum speed (Wet-end) | 450m per minute | 380m per minute |
Maximum speed (Dry-end) | 400m per minute | 350m per minute |
Maximum paper width | 2,800mm (110.24"), 2,500mm (98.43") | 2,800mm (110.24"), 2,500mm (98.43"), 2,200mm (86.61") |
Paper roll diameter | 450mm (17.72") - 1,524mm (60.00") | |
Overall length of machinery | approx.130m (426.51') | approx.115m (377.30') |
Cut-off classification | Double | Single |
Manufacturable corrugated board | Single wall / Double wall | |
Manufacturable flute | A · B · C · E · F · AB · CB · CE · BE · AA, etc. | |
Manufacturable paper weight | [Liner] 90g/m² - 440g/m² [Medium] 90g/m² - 280g/m² |
H-350 (Single Cut-off type)
SINGLE FACER
60H
60H Single Facer applies Belt Press System that Mitsubishi has more than 30 years experiences eliminating pressure-marks on corrugated boards. Motorized cartridge moving device is available to adapt as an option. Peripherally heated corrugating rolls are available upon customers' request.
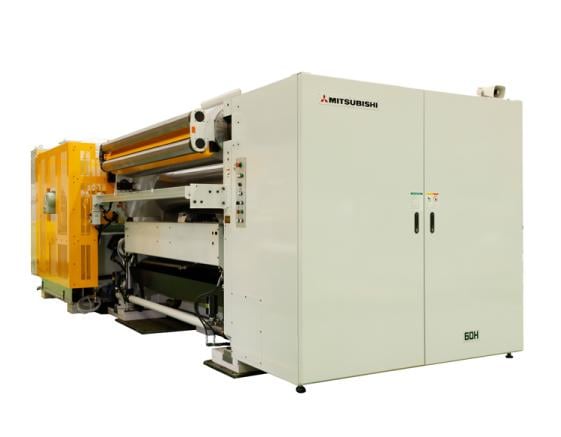
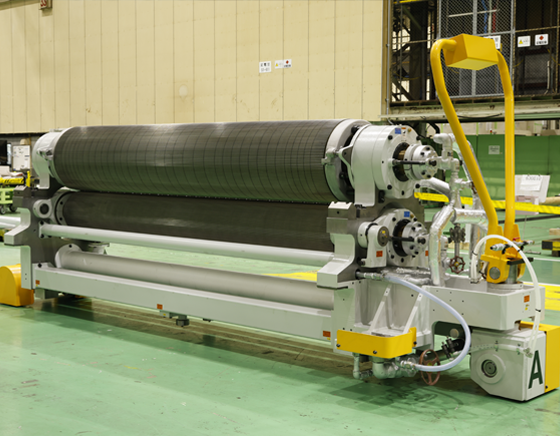
Advantages
Belt Press System realizes high-speed and stable lamination for various kinds of papers. The cartridge system makes it easier to produce a variety of flutes with one single facer. Furthermore, Mitsubishi has experience for high-speed production with micro-flute.
Main specifications
Please slide horizontally to view the table.
Model | 60H Single Facer |
---|---|
Maximum machine speed | 450m per minute |
Machine width | 1,800mm (70.87"), 2,000mm (78.74"), 2,200mm (86.61"), 2,500mm (98.43"), 2,800mm (110.24") |
Standard specifications |
|
- Specifications and designs are subject to change without prior notice and without any obligation on the part of manufacturer.
PREHEATER
61N/61H/51H, 62N/62H/52H
Wrap roll remote adjustment device and process control function are equipped as standard, the amount of preheating can be optimally controlled. Contributes to labor savings and improve corrugated board quality.
Preheater model 61NT
Advantages
A variety of preheat drum configurations with warp roll on each preheater are available depending on individual customer's needs for flutes and production speeds.
Main specifications
Please slide horizontally to view the table.
Model | 61N Liner Preheater | 62N Medium Preconditioner | 61NT Triple Preheater |
---|---|---|---|
Machine width | 2,500mm (98.43"), 2,800mm (110.24") | ||
Preheating drum standard diameter | 910mm (35.83") | 500mm (19.69") | 910mm (35.83") |
Preheating drum optional diameter | 750mm (29.53"), 1,100mm (43.31") |
750mm (29.53"), 910mm (35.83"), 1,100mm (43.31") |
1,100mm (43.31") |
Standard specifications |
|
|
|
Model | 61H/51H Liner Preheater | 62H/52H Medium Preconditioner | 61H/51H Triple Preheater |
---|---|---|---|
Machine width | 1,800mm (70.87"), 2,000mm (78.74"), 2,200mm (86.61"), 2,500mm (98.43") | ||
Preheating drum standard diameter | 910mm (35.83") | 500mm (19.69") | 910mm (35.83") |
Preheating drum optional diameter | 750mm (29.53"), 1,100mm (43.31") |
750mm (29.53"), 910mm (35.83"), 1,100mm (43.31") |
1,100mm (43.31") |
Standard specifications |
|
|
|
- Depending on required production speed, single or double type preheat drum will be selected. Specifications and designs are subject to change without prior notice and without any obligation on the part of manufacturer.
MILL ROLL STAND
63N/53H
63N/53H Mill Roll Stand reduces operator work and makes it easier to change paper rolls.
Increase arm opening/closing & lifting speed and shorten the cycle time of paper roll change significantly.
Advantages
It realizes smooth web feeding with excellent tension control up to maximum diameter of paper roll (i.e. 1,524mm diameter roll) at all production speeds in case of light/heavy weight paper rolls.
Main specifications
Please slide horizontally to view the table.
Model | 63N Mill Roll Stand | 53H Mill Roll Stand |
---|---|---|
Machine width | 2,500mm (98.43"), 2,800mm (110.24") | 1,800mm (70.87"), 2,000mm (78.74"), 2,200mm (86.61"), 2,500mm (98.43"), 2,800mm (110.24") |
Maximum paper diameter | 1,524mm (60.00") | |
Minimum paper diameter | 330mm (12.99") for manual chucking 450mm (17.72") for auto chucking |
|
Standard specifications | Arm open/close method: Hydraulic cylinder |
Arm open/close method: Ball screw with hydraulic motor |
|
- Specifications and designs are subject to change without prior notice and without any obligation on the part of manufacturer.
AUTO SPLICER
63-1N/63-1J
63-1N Auto Splicer boasts faster paper splicing speed at 584m per minute for medium paper. Equipped with tension control system to prevent wrinkles and stabilize paper splice.
Advantages
It realizes stable and reliable splicing performance at variation of production speeds with light/heavy weight of paper rolls equipped with exit roll tension control device.
Main specifications
Please slide horizontally to view the table.
Model | 63-1N Auto Splicer for Liner | 63-1N Auto Splicer for Medium |
---|---|---|
Maximum splicing speed | 400m per minute | 584m per minute |
Machine width | 2,500mm (98.43"), 2,800mm (110.24") | |
Maximum paper width | 1,524mm (60.00") | |
Standard specifications |
|
|
Model | 63-1J Auto Splicer | |
---|---|---|
Maximum splicing speed | 693m per minute | |
Machine width | 1,800mm (70.87"), 2,000mm (78.74"), 2,200mm (86.61"), 2,500mm (98.43"), 2,800mm (110.24") |
|
Maximum paper width | 1,524mm (60.00") | |
Standard specifications |
|
- Specifications and designs are subject to change without prior notice and without any obligation on the part of manufacturer.
These maximum splicing speeds are shown when the options are selected.
GLUE MACHINE
65J
The rider roll is placed with the glue applicator roll horizontally to reduce glue splash significantly. The glue amount applied on corrugated boards can be controlled optimally using process commander.
Advantages
The application of positive cell of glue applicator roll brings constant glue amount, reduces glue splashing, and makes cleaning easily. Edge wiper for glue applicator roll is available as an option to reduce glue accumulation on heating plates.
Main specifications
Please slide horizontally to view the table.
Model | 65J Glue Machine |
---|---|
Maximum machine speed | 400m per minute |
Machine width | 1,800mm (70.87"), 2,000mm (78.74"), 2,200mm (86.61"), 2,500mm (98.43"), 2,800mm (110.24") |
Standard specifications |
|
- Specifications and designs are subject to change without prior notice and without any obligation on the part of manufacturer.
DOUBLE FACER
66N/56H
In order to operate various types of paper and flutes stably at high speed, Mitsubishi designs high performance 66N/56H Double Facer incorporating unique technical know-how. It applies non-crushing air bag system to realize stable bonding regardless of flutes and production speeds.
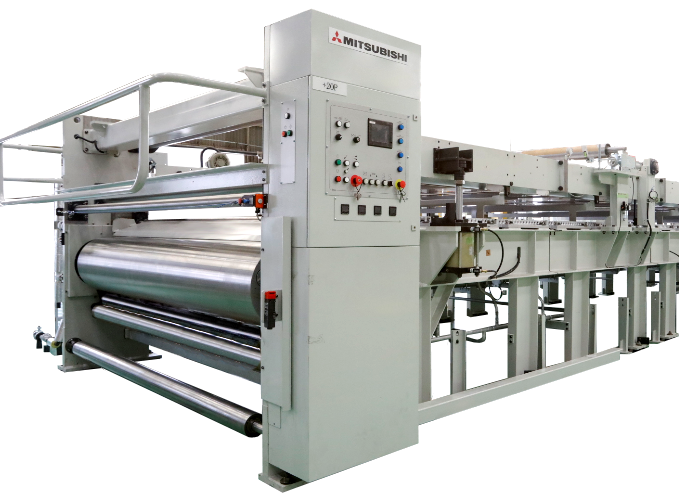
Advantages
The application of thin type heating plates increases heat efficiency and realizes quick heat response and less steam pressure than conventional. Air bag type loading system uniforms forming pressure on corrugated boards. Zero pressure is also available.
Main specifications
Please slide horizontally to view the table.
Model | 66N Double Facer | 56H Double Facer |
---|---|---|
Maximum machine speed | 400m per minute | 350m per minute |
Machine width | 2,500mm (98.43"), 2,800mm (110.24") | 1,800mm (70.87"), 2,000mm (78.74"), 2,200mm (86.61"), 2,500mm (98.43”) |
Standard specifications |
|
|
- Specifications and designs are subject to change without prior notice and without any obligation on the part of manufacturer.
SLITTER SCORER
67N/57H-V
67N Slitter Scorer is adapted tandem configuration and each station equips with two scorer shafts and one slitter shaft. Special scorer head is also available.
Advantages
Lower knives slit and the slitter heads are driven by servo motors, realizing to reduce defective sheets when order changes and to adjust knife height automatically.
Main specifications
Please slide horizontally to view the table.
Model | 67N Slitter Scorer | 57H-V Slitter Scorer |
---|---|---|
Maximum machine speed | 450m per minute | 400m per minute |
Machine width | 1,800mm (70.87"), 2,000mm (78.74"), 2,200mm (86.61"), 2,500mm (98.43"), 2,800mm (110.24") |
1,800mm (70.87"), 2,000mm (78.74"), 2,200mm (86.61"), 2,500mm (98.43") |
Maximum box-out | 8 boxes-out (See note 1) | 7 boxes-out |
Minimum slitting width | 190mm (7.48") | |
Minimum scoring width | 0mm (Minimum width on same shaft: 120mm (4.72")) | |
Standard specifications |
|
|
|
- 1In case of 2,800mm width machine.
- 2Specifications and designs are subject to change without prior notice and without any obligation on the part of manufacturer.
CUT OFF
58H
58H Cut Off is equipped with a pair of light-weighted knife cylinders with lower inertia to reduce energy consumption and achieve high production speed with high accuracy of cutting.

Advantages
It applies two sets of measuring wheels separately from Cut Off unit located at rotary shear and at infeed conveyor independently to warrant high accuracy of cutting.
Main specifications
Please slide horizontally to view the table.
Model | 58H Cut Off | |
---|---|---|
Maximum machine speed | 375m per minute | |
Machine width | 1,800mm (70.87"), 2,000mm (78.74"), 2,200mm (86.61"), 2,500mm (98.43") |
|
Standard specifications |
|
- Specifications and designs are subject to change without prior notice and without any obligation on the part of manufacturer.
STACKER
69J/59J
69J Stacker, jointly developed by Mitsubishi and Shizuoka-Koki, achieves minimum cycle time of 8 seconds.
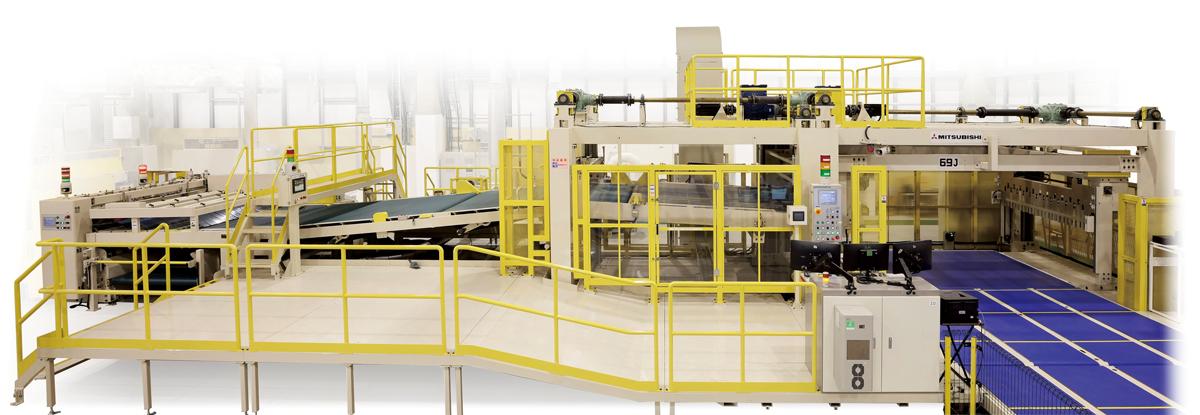
Advantages
69J/59J stackers are capable for reliable & accurate separation and high-quality stacking. Especially, in terms of the capability to handle short orders, they has been honored in Japanese market. It is one of the best stackers in the world.
Main specifications
Please slide horizontally to view the table.
Model | 69J Stacker | 59J Stacker |
---|---|---|
Maximum machine speed | 400m per minute | |
Machine width | 1,800mm (70.87"), 2,000mm (78.74"), 2,200mm (86.61"), 2,500mm (98.43") | |
Maximum sheet stacking height | 1,800mm (70.87") | |
Minimum stacking sheet width | 260mm (10.24") | |
Range of stacking sheet length | 500 - 3,000mm (19.69" - 118.11") | |
Standard specifications |
|
|
|
- Specifications and designs are subject to change without prior notice and without any obligation on the part of manufacturer.
PRODUCTION CONTROL SYSTEM
Sigma 2000N/3000
Sigma 2000N production control system maximizes the performance of corrugating machine and ensures easy operations with high productivity for frequent order changes and short paper cycles.
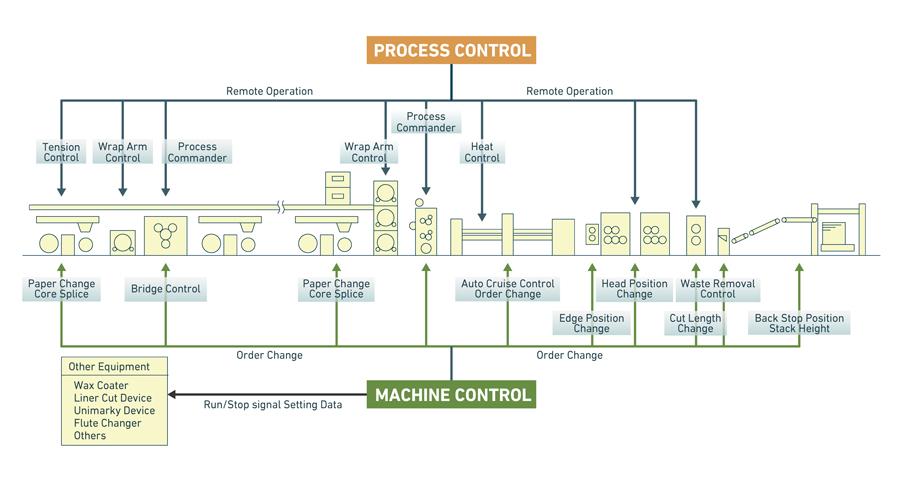
Main specifications
Please slide horizontally to view the table.
Model | Sigma 2000N / 3000 |
---|---|
Standard specifications |
|
- Specifications and designs are subject to change without prior notice and without any obligation on the part of manufacturer.
Defective Flute Detector (DFD) (Option)
The system is observing running corrugated board web and check the flute height measuring the flute shadow pitch by camera. If the pitch become abnormal, the production control system tracks its point and discharge it after Cut Off automatically without operator's intervention.
Main specifications
Please slide horizontally to view the table.
Model | Defective Flute Detector (DFD) |
---|---|
Standard specifications |
|
- Specifications and designs are subject to change without prior notice and without any obligation on the part of manufacturer.